The semi-lugged butterfly valve has emerged as a vital component in fluid control systems across diverse industries, including water treatment, chemical processing, and power generation. Known for their reliability and efficiency, these valves are crafted to provide precise control and longevity, making them a sought-after choice for engineers and technicians alike.
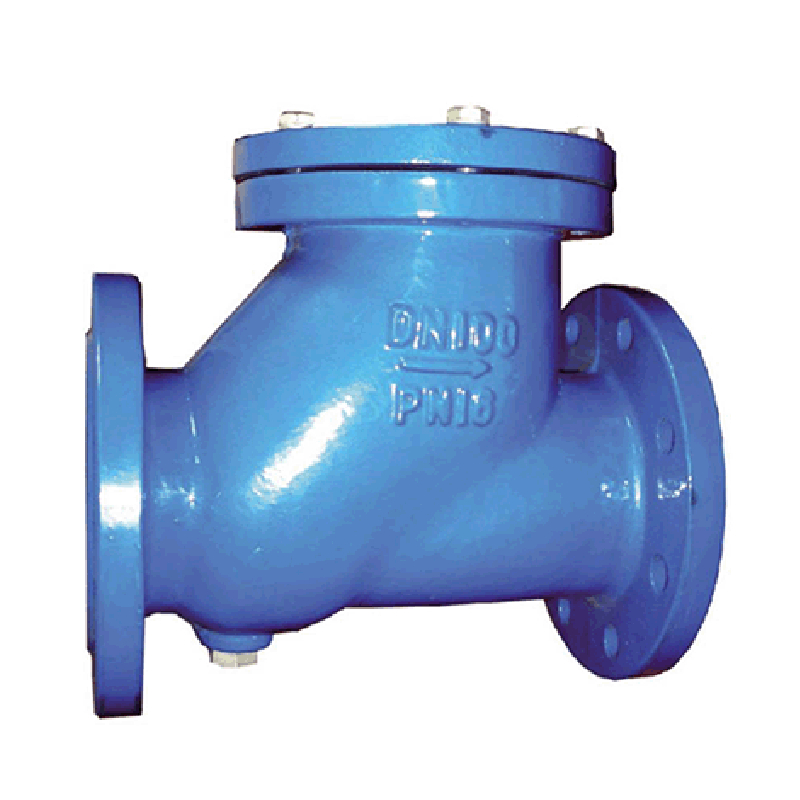
In an environment where performance and durability are paramount, semi-lugged butterfly valves offer a blend of simplicity and effectiveness. The design involves a flat circular disc positioned in the pipe, which rotates on a central axis. This straightforward mechanism allows for the regulation of flow, providing either a full shut-off or a variable passage of the medium. Unlike fully lugged butterfly valves, the semi-lugged variant typically features lugs only on one side, offering a lighter and often more cost-effective solution without compromising on function.
One of the main advantages of using semi-lugged butterfly valves is their installation ease. Given their lighter weight compared to fully lugged and flanged counterparts, they require less structural support, reducing overall installation costs. This feature makes semi-lugged butterfly valves ideal for systems where ease of maintenance and quick removal for inspection are crucial. These valves can be quickly replaced or repaired without shutting down the entire system, thus enhancing operational efficiency.
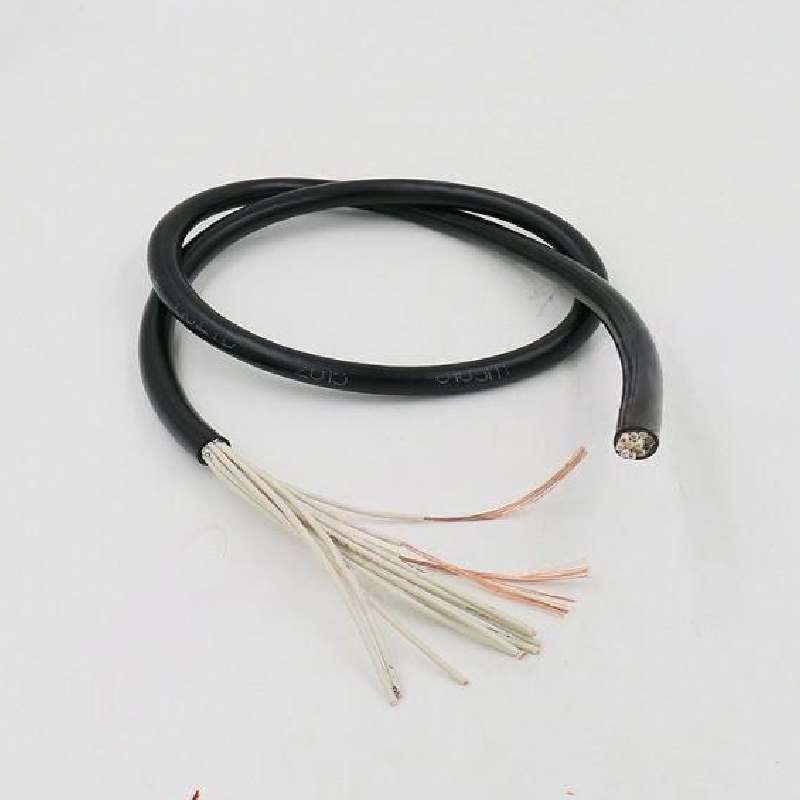
Durability is another critical factor. Constructed from high-quality materials such as stainless steel, carbon steel, or cast iron, semi-lugged butterfly valves are equipped to withstand harsh conditions and pressures. Such robustness makes them perfectly suited for industrial environments where the media may be corrosive or abrasive. The choice of materials also extends their operational lifespan, ensuring that the valve can function optimally over extended periods, thus reducing maintenance costs and downtime.
semi lugged butterfly valve
Moreover, the precision engineering of semi-lugged butterfly valves ensures minimal pressure drop when in the fully open position, maintaining system efficiency. This feature is particularly significant in applications requiring high-volume fluid transfer and where maintaining pressure levels is critical. The valves provide an excellent sealing mechanism, often employing resilient seats made from materials such as EPDM, NBR, or PTFE, which provide a tight closure to prevent leakages, thereby ensuring that the system remains secure.
Expert installation and sizing are essential to achieving the best performance from these valves. Incorrect sizing could lead to inefficiencies and potentially damage the system. Therefore, consulting with an expert who can assess the specific requirements of your system and recommend the appropriate semi-lugged butterfly valve is a wise investment. An experienced professional will ensure that the valve integrates seamlessly with existing infrastructure, thus enhancing overall operational effectiveness.
In addition to their mechanical benefits, using semi-lugged butterfly valves also supports sustainability initiatives. Their design requires fewer materials, thus minimizing environmental impact during the manufacturing process. Furthermore, their efficiency contributes to energy savings by reducing the amount of force needed to operate the valve, which is an essential factor for companies looking to reduce their carbon footprint.
In conclusion, the semi-lugged butterfly valve stands out as a reliable, efficient, and sustainable solution for modern industrial applications. Its ease of installation, durability, and operational efficiency make it a preferable choice for systems that demand precision and reliability. Ensuring the right fit and expert installation will leverage these valves' full potential, making them an invaluable asset to any fluid control strategy. As industries continue to evolve and place higher value on efficiency and sustainability, the role of the semi-lugged butterfly valve is poised to become even more significant in maintaining high standards of operational excellence.