Industrial valves, a crucial component in various sectors, play an indispensable role in controlling, regulating, and directing the flow of fluids. Their significance is underscored in industries ranging from oil and gas to water treatment and pharmaceuticals. These seemingly inconspicuous devices are engineered and manufactured with precision to meet the demanding needs of modern industry while ensuring safety, efficiency, and reliability.
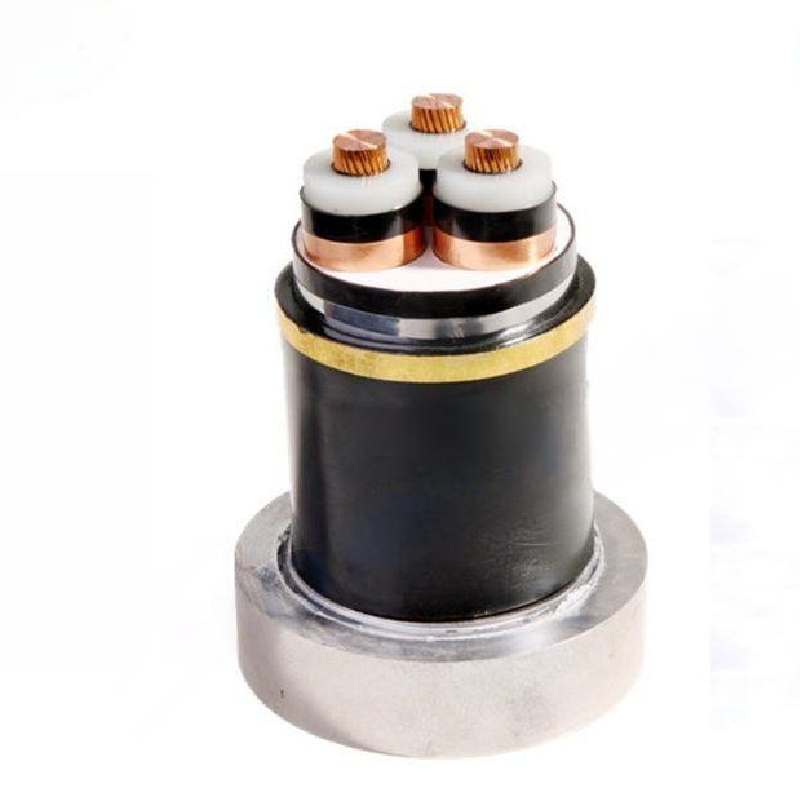
The production of industrial valves combines precision engineering, material science, and rigorous testing. High-quality valves are crafted from robust materials such as stainless steel, carbon steel, and brass to withstand extreme pressures, temperatures, and corrosive environments. Manufacturers employ advanced technologies like CNC machining and 3D modeling to ensure the accuracy and consistency of valve components.
Expertise in valve selection is critical for optimal performance. Each application demands specific valve types—such as gate, globe, ball, butterfly, or check valves—each offering distinct advantages. For instance, ball valves, known for their tight seal and rapid shut-off, are often used in high-pressure applications. In contrast, butterfly valves offer a lightweight solution with fast operation, ideal for large volume flow systems. The intricacies of valve mechanics require a thorough understanding of the system's dynamics and fluid properties, ensuring that the right valve is chosen for the task.
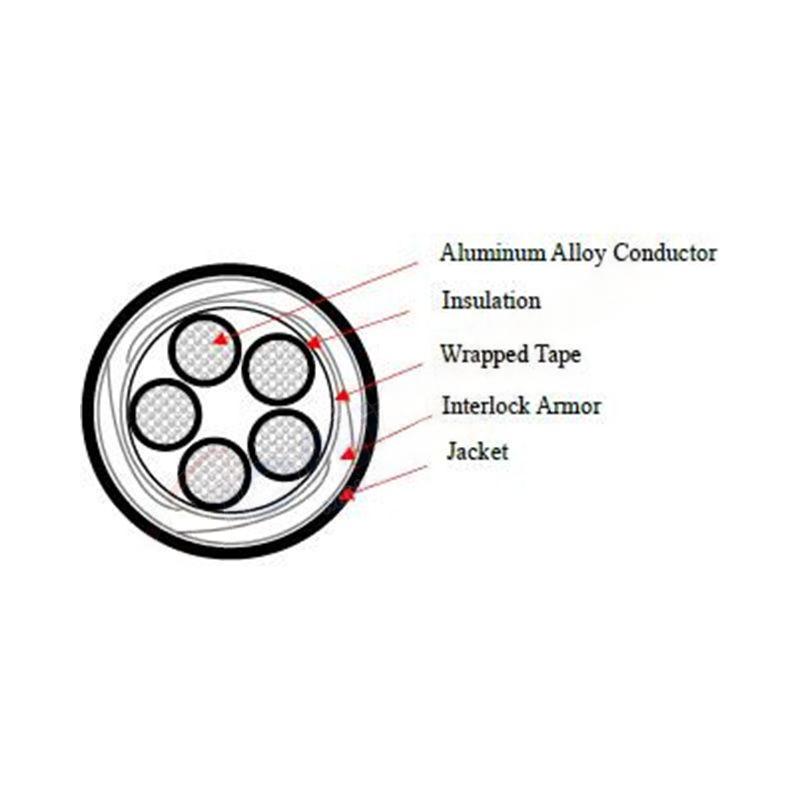
Authoritative sources within the industry emphasize the importance of compliance with international standards and certifications. Bodies such as the American Petroleum Institute (API), the International Organization for Standardization (ISO), and the American Society of Mechanical Engineers (ASME) provide frameworks that guarantee valve quality, safety, and efficiency. Manufacturers that adhere to these standards are recognized as industry leaders, providing assurance to clients through documented reliability and performance.
industrial valve
Trust in industrial valves is further established through rigorous testing procedures. Pressure testing, leakage testing, and lifecycle longevity testing are integral to the production process. Valves are subjected to these stringent assessments to simulate real-world conditions, ensuring they perform as expected when deployed. This attention to detail in testing is fundamental to building confidence among end-users, who rely on these components for critical applications.
From an end-user perspective, maintenance and regular inspection of industrial valves are vital to extending their lifespan and maintaining optimal functioning. Proper training in the handling and operation of these devices should not be overlooked, as improper use can lead to system failures, loss of production, and even safety hazards. Established companies offer comprehensive training programs and technical support to assist clients in maximizing the lifespan and efficiency of their valve investments.
Innovations in valve technology continue to enhance their performance and adaptability to complex industrial environments. The integration of smart technology—featuring sensors and remote monitoring—allows for real-time data analysis and preventative maintenance, reducing downtime and operational costs. These advancements hold significant potential for enhancing energy efficiency and environmental sustainability.
As industries evolve, the demand for reliable and efficient industrial valves grows. Choosing the right valve not only enhances system performance but also underscores a commitment to safe and sustainable industrial operations. For businesses looking to stay ahead, investing in high-quality valves and adhering to best practices in their deployment and maintenance is an essential strategy for long-term success.