In the realm of industrial and mechanical engineering, the double sphere union type rubber joint stands out as a pivotal component, delivering unmatched performance and reliability. These versatile components play a critical role in mitigating stress and vibration, which are common in pipeline systems due to various factors such as temperature fluctuations, pressure changes, and misalignment. With an increasing reliance on complex piping systems across industries, the double sphere union type rubber joint becomes indispensable for ensuring operational efficiency and longevity.
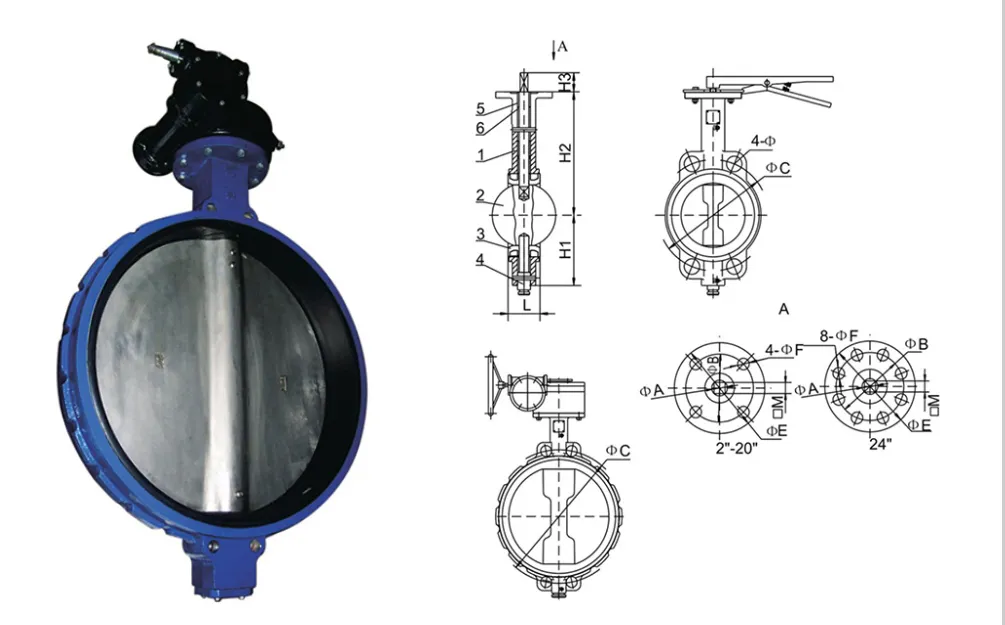
Characterized by its two spherical ends and union-type connections, this rubber joint offers remarkable flexibility and resilience. The spheres, typically crafted from high-quality rubber, allow the joint to absorb substantial axial, radial, and angular movements. This flexibility is crucial for accommodating shifts and constraints within the pipeline, preventing potential damage due to expansion, contraction, or seismic activity. Furthermore, the union type connections facilitate easy installation and maintenance—even in the most confined spaces—making them a preferred choice for engineers and technicians aiming for optimized performance.
From an expertise standpoint, the manufacturing of double sphere union type rubber joints demands precision engineering and superior material choice. The rubber used must possess excellent tensile strength, elasticity, and resistance to harsh environmental conditions like high temperatures, chemicals, and UV radiation. The incorporation of advanced technologies, such as computational stress analysis and fatigue testing, ensures these joints can withstand the rigors of demanding applications across various sectors—be it petrochemical plants, water treatment facilities, HVAC systems, or power stations.
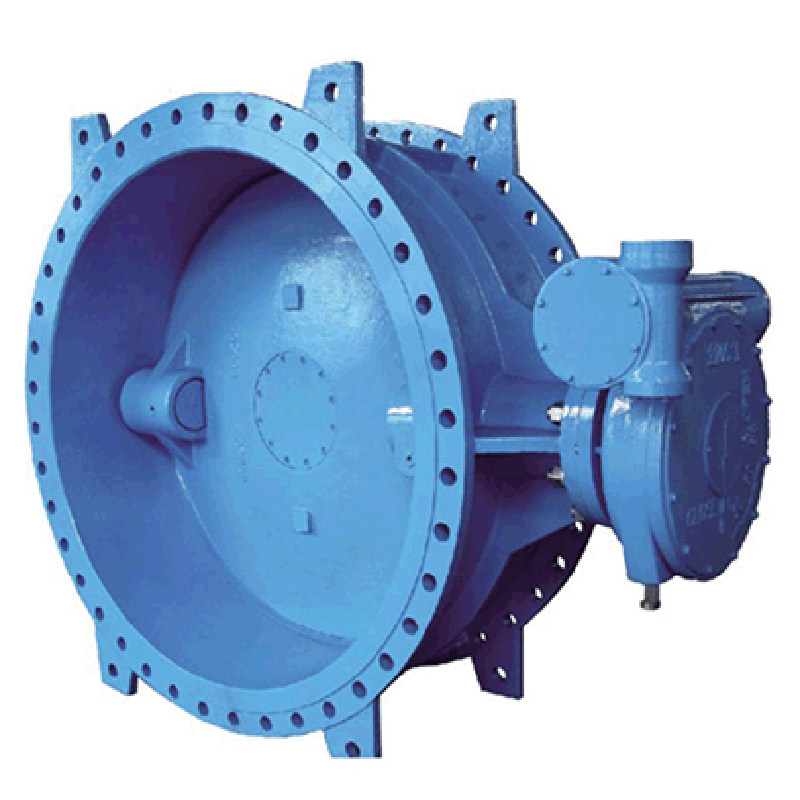
Furthermore, expertise in rubber formulation is crucial for enhancing the joint’s performance characteristics. Engineers often customize the rubber compounds to suit specific operational needs, balancing between elasticity and rigidity. This customization process may involve the use of natural rubber, nitrile, neoprene, or EPDM, each offering unique attributes such as oil resistance, weatherability, or thermal stability. Such customization not only prolongs the service life of the rubber joints but also guarantees compatibility with the conveyed materials, thus ensuring seamless operation.
double sphere union type rubber joint
The authoritativeness of the double sphere union type rubber joint design is reinforced through adherence to stringent industry standards and certifications. Manufacturers that align their production processes with international regulations, such as those set by ASTM (American Society for Testing and Materials) or ISO (International Organization for Standardization), offer products that guarantee quality and safety. Validation from these entities not only instills confidence in the product’s reliability but also attests to its performance under varied conditions.
With trustworthiness being a cornerstone in the selection of industrial components, double sphere union type rubber joints are meticulously tested for integrity and durability. Non-destructive testing methods, such as ultrasonic testing and radiography, assess the internal consistency and surface uniformity, eliminating any potential defects. These robust testing procedures are instrumental in verifying the joint’s capability to handle high-pressure loads and extensive cyclic operations without failure.
On-ground experience further sheds light on the indispensable nature of these components. Case studies often highlight scenarios where the incorporation of double sphere union type rubber joints has significantly reduced downtime and maintenance costs. In practical terms, these joints facilitate a seamless integration within existing systems, reducing operational stress and enhancing the efficiency of pipeline operations. Field engineers frequently report improved system stability and a marked reduction in mechanical failures, underscoring the joint’s role in extending system lifespans and improving ROI (Return on Investment).
In conclusion, the double sphere union type rubber joint epitomizes engineering excellence, offering unparalleled adaptability and robustness crucial for modern-day industrial applications. Its strategic design, backed by authoritative standards and rigorous testing protocols, renders it a reliable choice for complex piping systems. As industries progressively advance, these rubber joints will continue to play a critical role in safeguarding infrastructure and optimizing operational efficiency, marking them as a cornerstone of industrial ingenuity and reliability. When investing in pipeline components, professionals must prioritize these aspects to ensure consistent performance, reduce maintenance overheads, and enhance overall system reliability.