Navigating the complex terrain of fluid systems requires an in-depth understanding of various components, and the swing check valve flange type is no exception. These critical devices play an essential role in controlling fluid flow, preventing reverse flow, and ensuring system integrity, particularly in industries such as oil and gas, water treatment, and chemical processing.
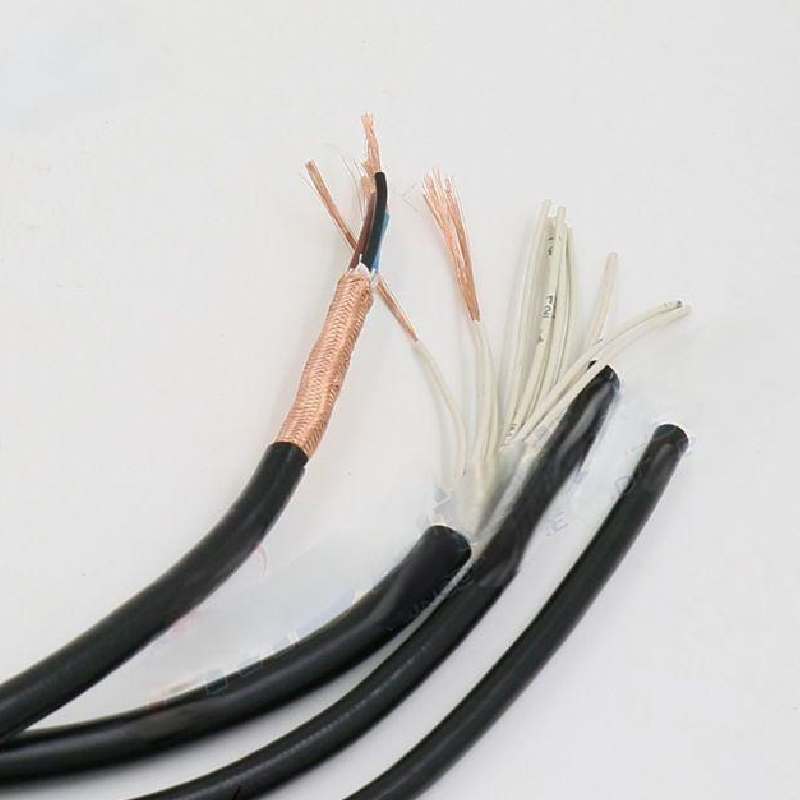
One of the standout benefits of a swing check valve flange type lies in its ability to provide reliable backflow prevention. Unlike other check valves, the swing check variant operates using a swinging disc that allows fluid to flow forward while sealing shut to prevent backward flow. This mechanism operates without manual intervention, reducing the need for constant supervision and lowering maintenance costs.
The flange type design enhances the versatility of the swing check valve. Flanges provide a robust connection between the valve and piping, offering superior strength and support compared to other connection types. This is particularly beneficial in applications with high pressure or where vibration and thermal expansion are concerns. The flange connection ensures a tight seal and makes maintenance more manageable due to easier access for inspection or replacement.
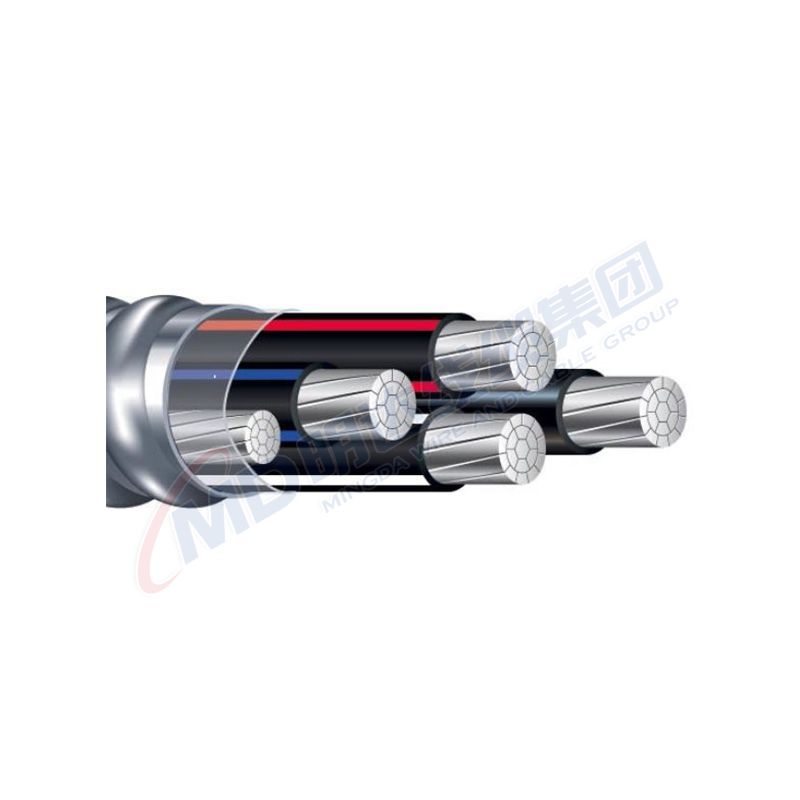
For industries dealing with corrosive fluids, choosing the right material for a swing check valve is crucial. High-quality manufacturers offer flange-type swing check valves made from stainless steel, ductile iron, or other specialized alloys. These materials ensure durability and longevity, even in the harshest of environments. A valve constructed from the right material can significantly enhance system reliability and reduce lifecycle costs, a point of consideration for systems operating over large distances or in remote locations.
Operational efficiency is a core aspect of the design of swing check valve flange types. Their streamlined build and function-oriented design minimize pressure drop across the valve, ensuring system efficiency is not compromised. In high-demand settings, even a slight reduction in pressure can lead to increased energy consumption. Therefore,
selecting a valve that maintains pressure integrity becomes imperative.
swing check valve flange type
A critical component of the expertise surrounding swing check valves is the sizing and installation process. Precise calculation of parameters—like flow rate, pressure, and fluid characteristics—is vital for optimized valve performance. Experts emphasize the need for thorough planning during the design phase to determine the exact specifications required. This assures not only efficient operation but also extends the operational lifespan of the entire system.
Adhering to industry standards and certifications is indispensable for ensuring valve quality and safety. Flange-type swing check valves are expected to comply with standards from bodies like the American Society of Mechanical Engineers (ASME) or the American Petroleum Institute (API). These certifications not only validate the product’s quality but also assure purchasers of its performance credibility.
Maintaining trustworthiness in valve performance is tied to routine testing and inspection. Periodic checks for signs of wear, such as issues with the swinging mechanism or flange integrity, help identify potential failures before they compromise system reliability. Establishing a regular maintenance and inspection protocol not only mitigates risks but can also yield substantial savings over time by preventing unexpected downtime.
Choosing a provider with a reputable history and proven customer satisfaction is essential. Verified reviews, case studies, and client testimonials are invaluable tools when selecting a swing check valve flange type. They provide insight into a manufacturer's track record, allowing purchasers to make informed decisions backed by other industry leaders’ experiences.
In conclusion, the swing check valve flange type stands as a pillar of integrity and efficiency in fluid systems. Its design complements high-demand environments, enhances system resilience, and ensures uninterrupted operation. Combining expertise with judicious selection and ongoing maintenance can elevate the performance of these valves, providing value far beyond initial implementation.