In the ever-evolving world of industrial valve technology, the wafer type butterfly valve stands out as a unique and highly efficient innovation. Its compact design and versatility make it an excellent choice for a myriad of applications, including water treatment, chemical processing, and various manufacturing industries. However, understanding its dimensions is crucial for maximizing its performance and ensuring optimal integration into fluid control systems.
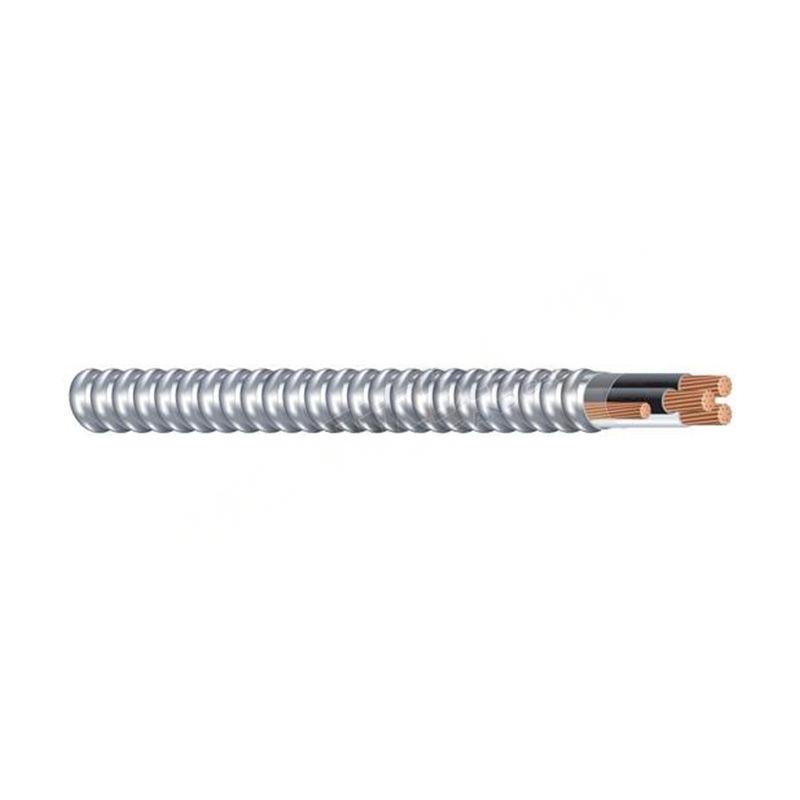
Wafer type butterfly valves are prized for their simple yet effective structure. Unlike other variants, the wafer design does not require studs or nuts for installation. Instead, it is positioned between flanges using bolts. This not only streamlines the installation process but also significantly reduces the amount of space needed. The absence of extended flanges on either side allows for a more streamlined setup, making it ideal for installations where space is at a premium.
When discussing the dimensions of wafer type butterfly valves, it's important to acknowledge the key measurements that impact their performance. These include the valve body diameter, flange bore, face-to-face distance, and disk diameter. Each plays a critical role in ensuring the valve functions correctly within a piping system without leaks or pressure drops.
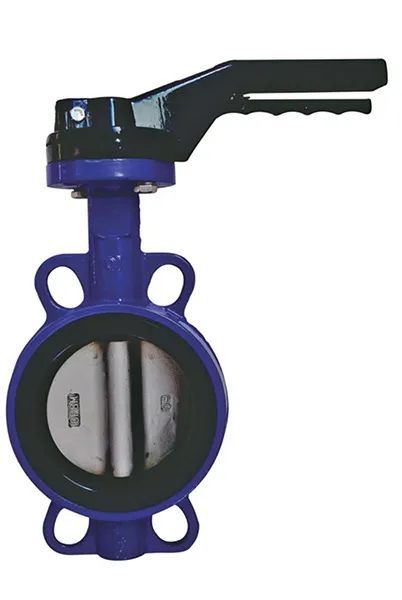
The body diameter of these valves typically ranges from a few inches to several feet, depending on the intended application and flow requirements. One of the key benefits of a wafer type butterfly valve is its lightweight construction compared to other valve designs, which significantly reduces the load stress on the piping system - a notable advantage in large-scale industrial applications like oil refineries and desalination plants.
The flange bore size must match the piping dimensions to ensure the valve operates efficiently within the system. Mismatched dimensions can lead to increased turbulence, pressure loss, or even catastrophic failure of the piping system. Therefore, precise measurement and specification adherence are crucial in this aspect.
Another critical dimension is the face-to-face distance. This measurement is standardized, allowing for easy replacement or upgrades without substantial modifications to the existing pipe system. Depending on industry standards such as ASME or ISO, these measurements often vary, so attention to detail is essential when selecting a valve for a specific application.
wafer type butterfly valve dimension
The disk diameter also plays a pivotal role. A well-designed disk minimizes energy loss and provides efficient flow control, quickly adjusting to changes in pressure or flow demand. In scenarios dealing with high pressure or corrosive fluids, disks are often coated with protective materials like Teflon or rubber. This prolongs the valve’s life and ensures consistent performance under challenging conditions.
The choice of material for the valve construction is equally important. Stainless steel, cast iron, and PVC are popular materials used in the construction of wafer type butterfly valves, each offering distinct advantages based on the media being controlled. For example, stainless steel is ideal for applications requiring high strength and corrosion resistance, whereas PVC is often used for lighter, non-corrosive environments.
In addition to its structural advantages, a wafer type butterfly valve's quick opening and closing capabilities make it a preferred choice in emergency shutoff applications, where speed and reliability are paramount. The ability to rapidly control flow rates enhances process efficiency and contributes to safer operational conditions.
Selecting the right wafer type butterfly valve requires a balanced consideration of dimensions, materials, and specific operational needs. As a seasoned industry professional, recognizing the nuances of these valves from an experiential standpoint allows for informed decision-making, ensuring that the chosen valve not only fits the physical parameters but also aligns with expected performance outcomes.
Synchronizing these components within an SEO framework requires a blend of technical precision and industry insight. By engaging this knowledge, professionals secure top-tier valve systems aligned with stringent modern demands, driving operational success and enhancing overall process efficiency.