Rubber joint flanges have emerged as versatile and essential components across various industries,
including plumbing, power generation, and marine. Their primary role in any system is to absorb vibrations, provide flexibility, and compensate for misalignments. These dynamic components ensure the seamless transfer of fluids, gases, or other substances without disruption. Due to the intricate applications they cater to, selecting the right type and quality of rubber joint flange becomes crucial for ensuring efficiency and long-term reliability.
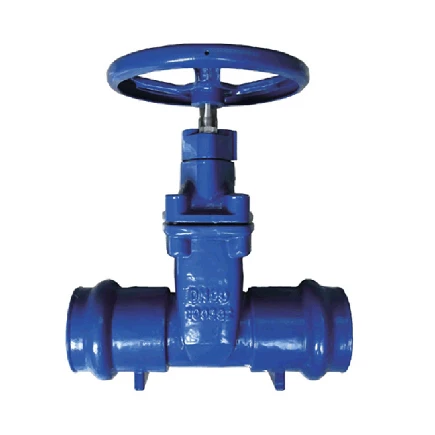
Experience is often the best teacher when it comes to understanding the value of rubber joint flanges. Many industries have shared their insights on the efficiency gains and operational stability offered by these components. Facilities dealing with high-pressure fluids, for instance, have noted a significant reduction in wear and tear when rubber joint flanges are employed. A real-world example involves a power generation plant that replaced its metallic couplings with rubber joint flanges. The result was a marked decrease in system downtimes and maintenance requirements, allowing for more consistent energy production. These authentic experiences underline the practicality and effectiveness of rubber joint flanges in demanding environments.
From an expertise perspective, understanding the mechanics behind rubber joint flanges emphasizes their significance. Unlike rigid connections, a rubber joint flange offers flexibility that accommodates movement in various directions such as axial compression, elongation, and angular deflection. This flexibility is particularly beneficial in applications where thermal expansion or mechanical vibrations are prevalent. Moreover, the rubber material exhibits excellent resistance to abrasion and weathering, ensuring longevity under severe operational conditions. For industries relying on precise fluid dynamics, such as chemical processing plants, the introduction of rubber joint flanges enhances the overall safety and efficiency of the system by mitigating the risks of leaks and ruptures.
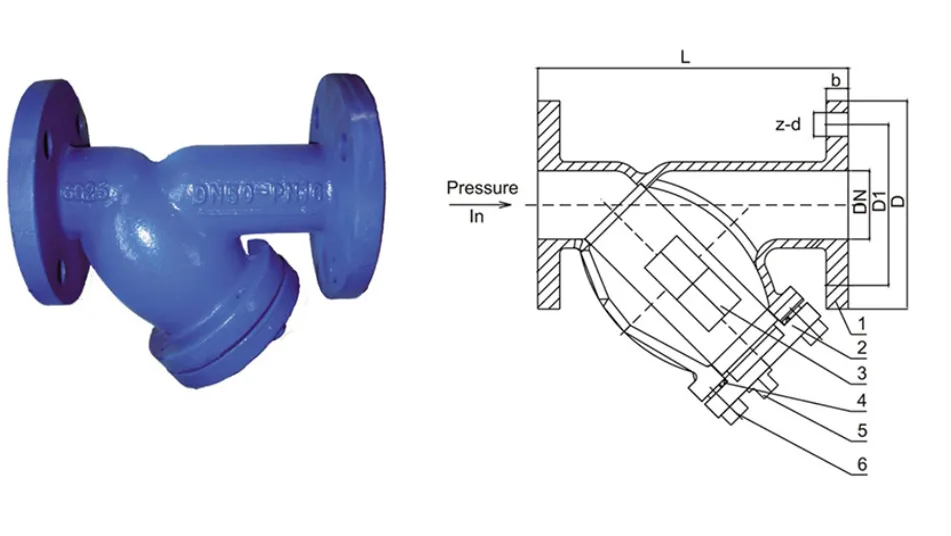
The authoritative standing of rubber joint flanges is further solidified by numerous industry standards and approvals that dictate their use. Various global bodies, including the American Society for Testing and Materials (ASTM) and the International Organization for Standardization (ISO), outline the specifications for these components to ensure they meet rigorous safety and performance criteria. For professionals and decision-makers, aligning with these standards guarantees that the flanges will operate reliably under specified conditions. Compliance with such authoritative guidelines not only safeguards the integrity of operational systems but also fortifies trust among stakeholders and customers.
rubber joint flange
Trustworthiness is particularly pivotal in industries where the slightest malfunction could lead to catastrophic consequences. The construction of rubber joint flanges focuses on reliability and quality, using materials like EPDM, NBR, or Neoprene, which provide exceptional resistance to heat, oil, and chemicals. When engaging with suppliers or manufacturers, transparency regarding material sourcing, production processes, and testing is essential. Customers benefiting from this trust often report not just operational efficiencies but also stronger relationships with reliable suppliers, which is indispensable for long-term business success.
For the technical evaluation of rubber joint flanges, several key considerations should guide the selection process. These include the operational pressure and temperature, material compatibility with specific substances, and the potential environmental conditions where the flanges will be deployed. Understanding these parameters helps in choosing an appropriate design that will optimize performance and longevity. For example, in marine applications, where saltwater exposure is a concern, selecting a rubber compound with superior resistance to corrosion will significantly enhance durability and performance.
Ultimately, the integration of rubber joint flanges into industrial systems is a testament to their unmatched ability to solve complex challenges while ensuring operational continuity. Their ability to accommodate movement, absorb vibrations, and provide leak-proof connections makes them indispensable. Through firsthand experiences, expert insights, and recognition from authoritative bodies, these components have gained a robust reputation for trustworthiness. Industries looking to enhance operational efficiency and reliability can rely on rubber joint flanges as vital cogs in their mechanical processes, ensuring both safety and success.