Choosing the Right Slurry Knife Gate Valve for Your Operations
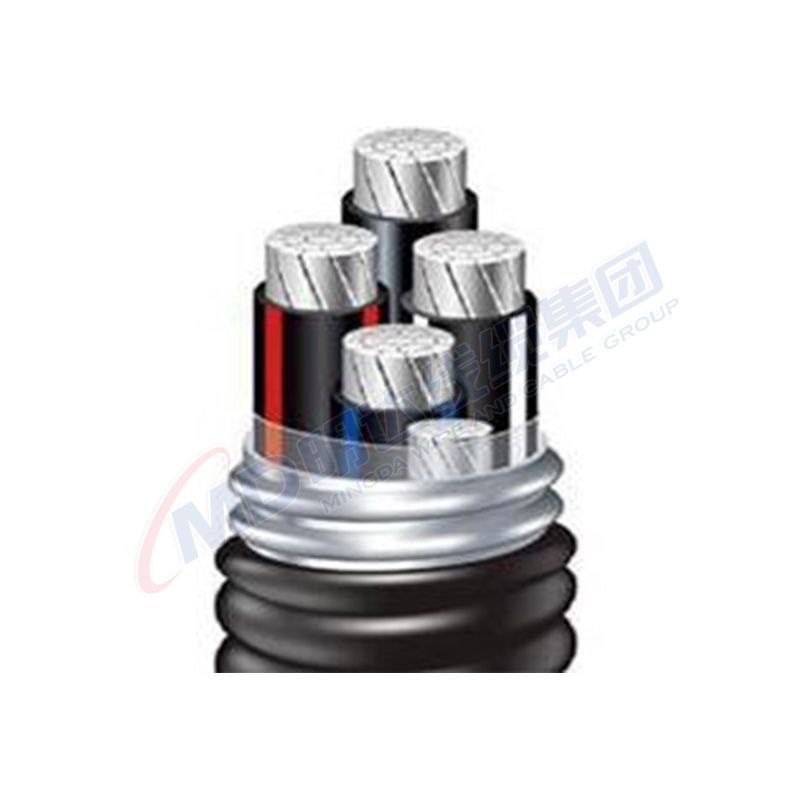
In industrial settings where slurry transport is a staple, the importance of a reliable slurry knife gate valve cannot be overemphasized. These valves are specifically engineered to handle the abrasive and challenging nature of slurry, which often includes a mix of liquids and solid particles. As such, selecting the appropriate valve is crucial to ensure seamless operations, minimize downtime, and extend the lifespan of your equipment. Drawing from years of field experience and technological expertise, this article explores the critical factors to consider when choosing a slurry knife gate valve, guiding you towards making an informed decision anchored in authoritativeness and trustworthiness.
First, consider the composition and concentration of the slurry you are dealing with. A diverse range of industries, from mining to wastewater treatment, use slurry knife gate valves.
Each application has unique fluid properties that influence the choice of valve material. For instance, highly abrasive slurries laden with coarse particles necessitate a valve made from robust materials, such as stainless steel or hard metal alloys. In contrast, applications involving corrosive slurries might require corrosion-resistant coatings or linings like elastomers or polymers to ensure longevity and reduce the need for frequent maintenance.
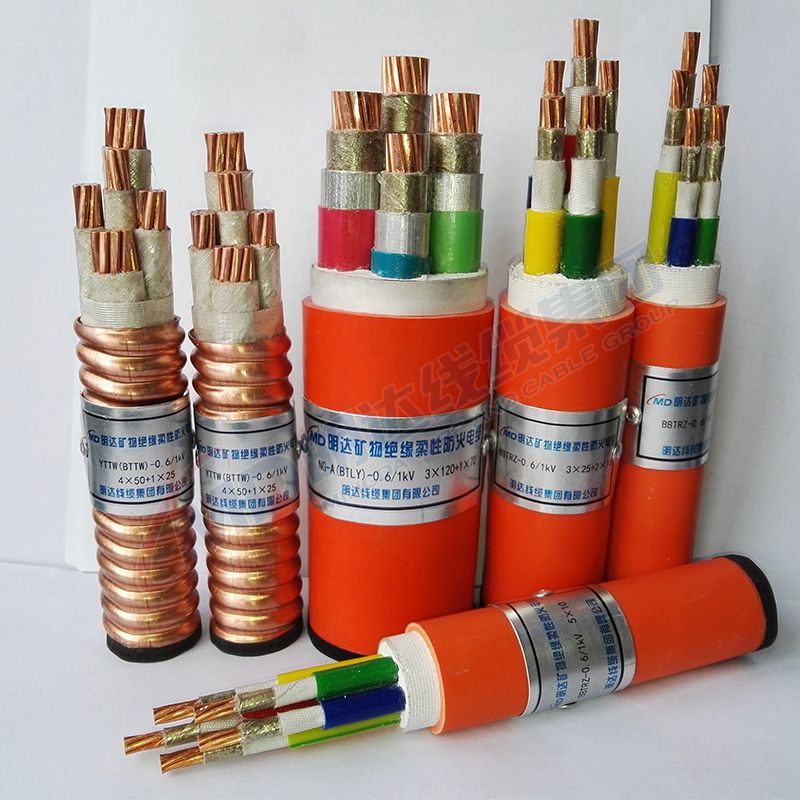
Equally crucial is understanding the valve’s pressure and temperature ratings. Slurry systems operate under various pressures and temperatures, and a valve that cannot withstand these conditions will result in performance failure. Check the maximum allowable working pressure (MAWP) of the valve, ensuring it fits within your operational parameters. Moreover, consider whether the valve can operate efficiently under extreme temperature conditions, be it hot or cryogenic temperatures, as this impacts the seal integrity and overall mechanical performance.
The design of the knife gate valve itself is another aspect warranting careful consideration. A streamlined design with minimal traps for particles will prevent clogging and reduce wear and tear. Some innovations feature a shearing action that cuts through solids, providing a tight seal even in the presence of fiber-laden slurries. Choose a design that matches your operational needs while enhancing performance and reducing maintenance.
slurry knife gate valve
Ease of maintenance is yet another critical factor. Valves that are difficult to service can lead to costly downtime, affecting overall productivity. Opt for valves with simple design features, such as replaceable seats and seals, which facilitate convenient in-field maintenance and repair. Furthermore, self-cleaning valves can significantly decrease maintenance time and effort, ensuring that your system remains operational for extended periods.
The credibility of the manufacturer and supplier also matters profoundly. Manufacturers with a proven track record in producing quality knife gate valves are generally more trustworthy. Look for certifications and endorsements that attest to the manufacturer's commitment to quality, such as ISO certifications or industry awards. It's also advisable to seek testimonials or case studies from other companies operating in similar environments, providing you with a peer-reviewed basis for your decision.
In the age of digital innovation, the availability of smart features in slurry knife gate valves can offer added advantages. Advanced monitoring capabilities enable real-time diagnostics and performance data retrieval, facilitating predictive maintenance and operational efficiency. Investing in a valve with integrated technology may offer long-term benefits in maintenance scheduling and reducing unexpected failures.
Ensuring that your choice of slurry knife gate valve aligns with these considerations will not only safeguard operational efficiency but also bolster the reliability and trustworthiness of your industrial processes. Given the complexity and varied nature of slurry applications, thoughtful selection and regular consultation with experts in the field can immensely benefit your facility. Always remember that the initial investment in a high-quality valve pays off significantly through sustained performance and reduced operational hiccups.