Grooved end butterfly valves stand at the forefront of modern fluid control systems, boasting unique attributes that cater to various industrial applications. Unlike traditional valves, these components offer a flexible and efficient solution for controlling the flow of liquids and gases. Their design simplicity combined with enhanced functionality makes them a preferred choice in sectors ranging from water treatment to oil and gas.
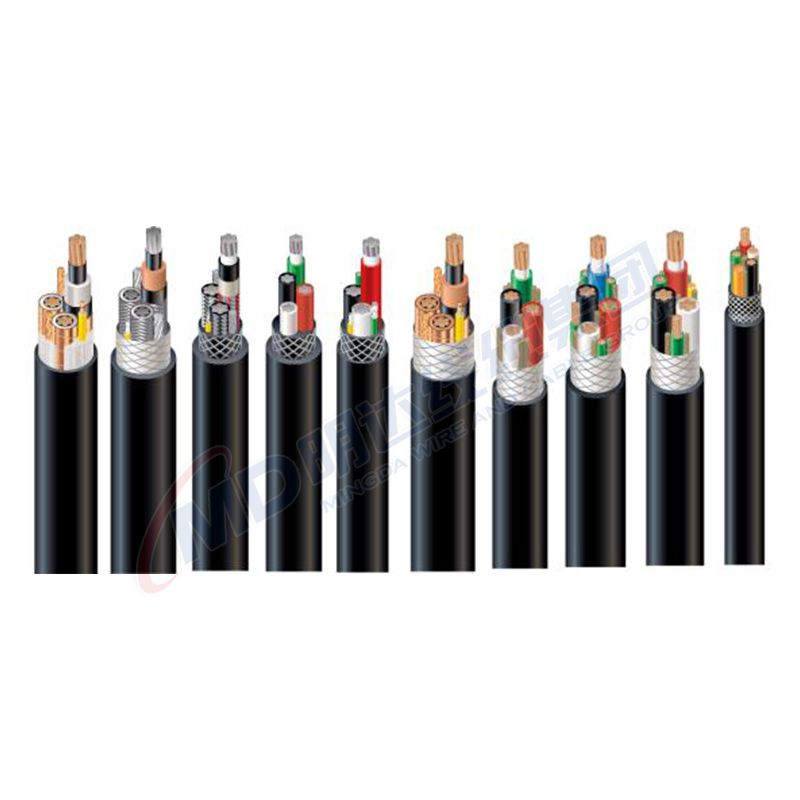
One of the distinct advantages of grooved end butterfly valves is their ease of installation. The grooved end design allows for quick and straightforward coupling, reducing labor costs and minimizing downtime during maintenance. This feature is particularly beneficial in time-sensitive industries where operational efficiency is paramount. By employing a standardized grooved connection, these valves can be seamlessly integrated into existing pipeline infrastructures without the need for extensive modifications.
Durability is another hallmark of the grooved end butterfly valve. Constructed from robust materials such as stainless steel, ductile iron, or other corrosion-resistant alloys, these valves are engineered to withstand extreme environmental conditions. This makes them suitable for applications where exposure to harsh chemicals, high pressure, or temperature fluctuations is common. Their long operating life ensures that industries can rely on consistent performance without frequent replacements, which is crucial for maintaining productivity and reducing lifecycle costs.
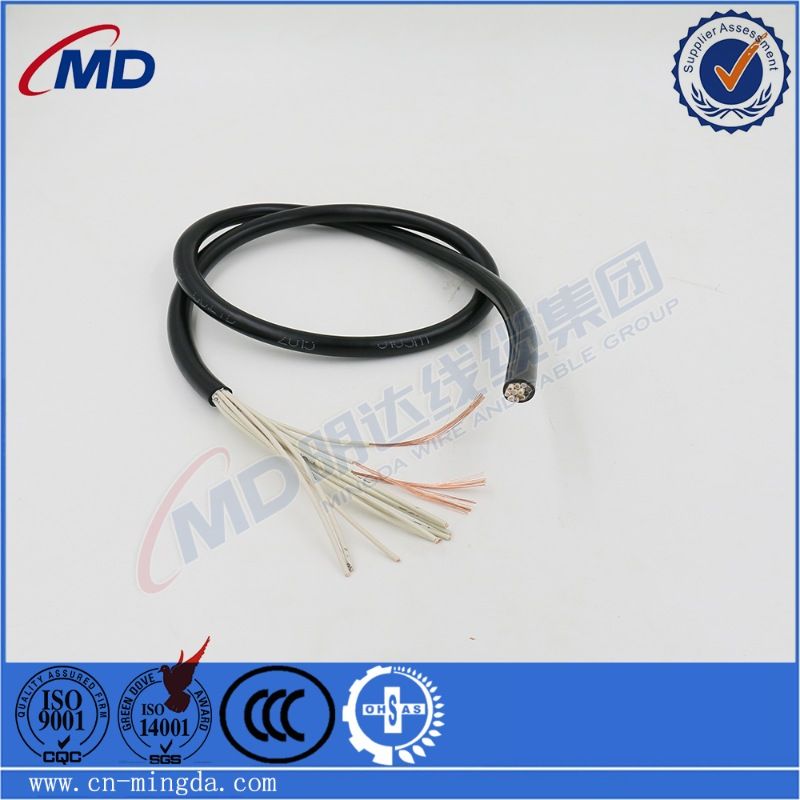
The operational simplicity of grooved end butterfly valves is an often-overlooked advantage that significantly enhances user experience. With a quarter-turn operation, they provide precise control over flow rates, allowing for quick adjustments as per process requirements. This simple mechanism not only minimizes the potential for user error but also reduces training time for personnel responsible for valve operation. Furthermore,
the butterfly design ensures minimal pressure drop, enhancing the efficiency of fluid systems.
grooved end butterfly valve
From an expertise perspective, manufacturers of grooved end butterfly valves leverage cutting-edge technologies to enhance functionality and reliability. Innovations such as advanced sealing technologies ensure leak-proof operation, even under high-pressure conditions. Engineers continuously refine the aerodynamics of the valve disc to improve flow characteristics and reduce wear, further solidifying their position as leaders in fluid control solutions.
Authoritativeness in this sector is backed by rigorous testing and adherence to international standards. Leading manufacturers subject grooved end butterfly valves to comprehensive quality assurance checks, including pressure testing, endurance testing, and material verification. Compliance with standards such as ISO, ANSI, and API assures users of the valves' reliability and suitability for critical applications. This authoritative validation is critical for industries where safety and precision are non-negotiable.
Trustworthiness is inherently built into the lifecycle of grooved end butterfly valves through transparent certifications and customer-centric warranties. Many reputable manufacturers offer extended warranties that reflect confidence in their product quality and after-sales support. Furthermore, detailed documentation accompanies each valve, providing users with essential information regarding installation, maintenance, and troubleshooting. This transparency fosters trust and long-term relationships with clients, reinforcing the manufacturer's commitment to quality and service.
In conclusion, grooved end butterfly valves epitomize innovation and reliability in fluid control systems. Their unique combination of easy installation, durability, operational efficiency, and technological advancements makes them an indispensable tool across various industries. By adhering to stringent quality standards and prioritizing customer satisfaction, manufacturers ensure these valves not only meet but exceed user expectations. As industries continue to evolve, the demand for efficient and robust fluid control solutions will undoubtedly propel grooved end butterfly valves to even greater prominence in the future.