Wafer and lugged butterfly valves are pivotal components in fluid control systems, playing an essential role in various industries, including oil and gas, water treatment, chemical processing, and HVAC systems. Understanding these valves' distinctive mechanisms, advantages, and selection criteria is crucial for professionals aiming to optimize system performance and ensure reliable operations.
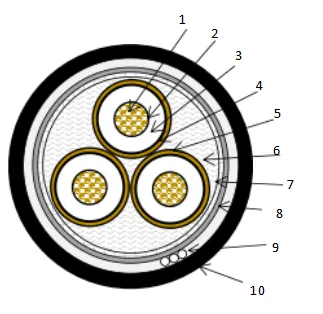
The wafer butterfly valve is known for its compact design, which allows for easy installation between two pipeline flanges. This feature translates into cost savings, as fewer materials and space are needed for assembly. However, its primary limitation lies in its lack of integral flange connections, which can be a liability if piping systems vibrate or are subjected to high-pressure conditions. Despite this, wafer valves are extremely effective for applications with low to medium pressure and where weight and space considerations are paramount.
In contrast,
the lugged butterfly valve offers enhanced stability and versatility. Equipped with threaded inserts, it functions effectively in systems where end-of-line service is required, and where dismantling parts of the pipeline might be necessary without causing disruption to the neighboring components. This makes lugged butterfly valves a preferred choice for systems with higher pressure requirements and those needing frequent maintenance activities. Although they are slightly more costly and heavier than their wafer counterparts, their ability to isolate sections of a piping system without complete shutdown justifies the investment in many industrial settings.

Professional expertise contributes significantly to selecting the appropriate valve type for specific applications. Engineers must consider various factors, including pressure rating, fluid properties, temperature, and potential chemical compatibility issues. The material of the valve components – typically made from metals like stainless steel or alloys, or polymers for corrosive environments – needs careful selection to avoid system failures. Tailoring the valve choice to these operational parameters can greatly enhance the lifespan and efficiency of the fluid control system.
wafer and lugged butterfly valve
Accurate installation and maintenance practices are vital for the performance and longevity of both wafer and lugged butterfly valves. Misalignment during installation can lead to issues like disc damage or sealing inefficiencies. Moreover, regular maintenance schedules should be in place to inspect for wear and tear, particularly in high-cycle applications where valves are operated frequently. This proactive approach ensures early detection of potential issues, preventing costly downtime and repairs.
From an authoritative perspective, standards and certifications, such as those from the American National Standards Institute (ANSI) or International Organization for Standardization (ISO), play a crucial role in guiding the quality and compatibility of butterfly valves in industrial applications. Trusting products and manufacturers that adhere to these standards assures users of the valve's reliability and safety.
Innovations in butterfly valve technology, such as advancements in smart sensors and automation integration, are further enhancing their utility. Smart valves equipped with sensors provide real-time data on valve positioning, pressure, and flow rates, offering operators enhanced control over system dynamics. Such technologies allow for predictive maintenance, reducing the need for manual inspections and increasing system uptime.
In conclusion, wafer and lugged butterfly valves are indispensable tools for efficient fluid control. Their selection, installation, and maintenance require a nuanced understanding of their operational context and demands. Industry professionals who equip themselves with this expertise can leverage these valves' benefits to achieve outstanding system performance and sustainable operations. As technology advances and new materials become available, butterfly valves are set to become even more integral in complex, automated, and high-demand environments, further underscoring the importance of informed and strategic valve selection.