Navigating the world of industrial valves, the actuated gate valve stands out as a pinnacle of engineering innovation, combining functionality with high performance. Essential in sectors ranging from oil and gas to water treatment, these valves are crucial for controlling the flow of liquids and gases. Understanding their unique advantages and applications can pave the way for more informed purchasing decisions and enhanced operational efficiency.
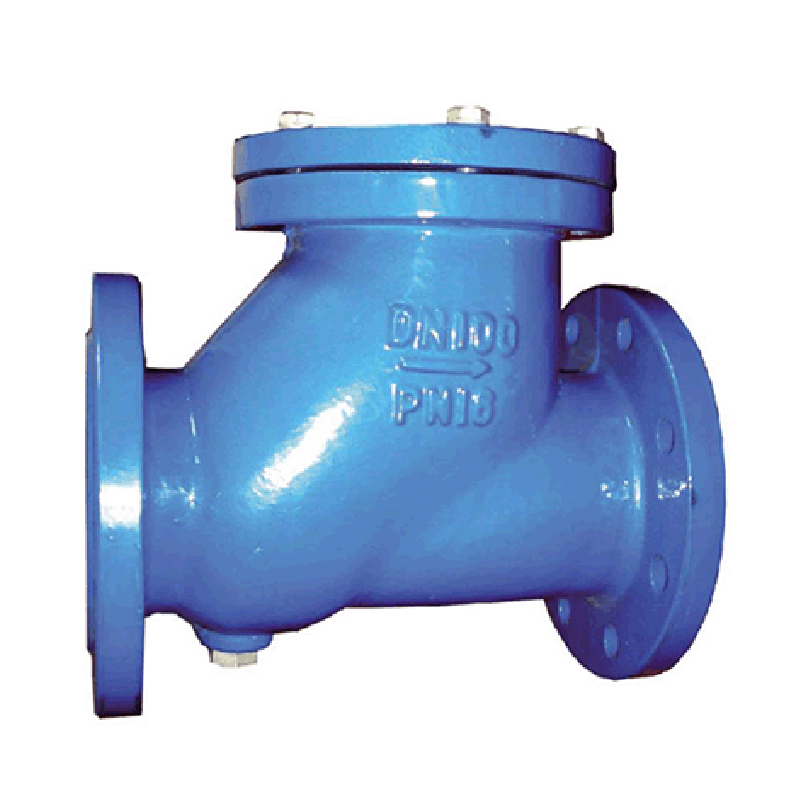
Actuated gate valves are distinct for their ability to offer precise flow control with minimal pressure drop when fully opened. This feature makes them ideal for applications where maintaining system pressure without sacrificing control is critical. The valve functions by utilizing an actuator, which automates the movement of the gate (a solid barrier inside the valve) to either allow or prevent flow. This automation eliminates the need for manual operation, increasing both safety and efficiency.
One key advantage of actuated gate valves is their adaptability to different environments and requirements. The actuators can be powered by various sources, including electric motors, pneumatic systems, or hydraulic units. Each power source offers distinct benefits; for instance, electric actuators are excellent for precise control, pneumatic actuators provide rapid response, and hydraulic units deliver high force in compact designs. This versatility ensures that actuated gate valves can be integrated into diverse systems, from remote pipelines to high-demand processing facilities.
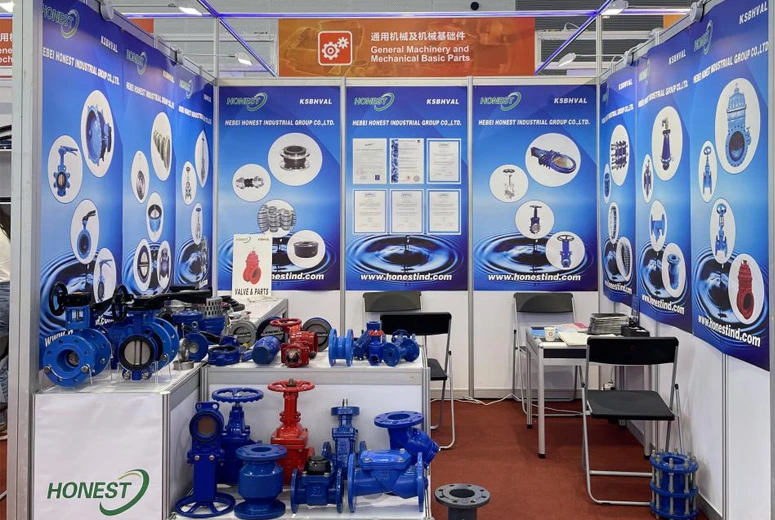
The materials used in manufacturing actuated gate valves also reflect their robustness and reliability. Often constructed from stainless steel, cast iron, or exotic alloys, these valves are built to withstand harsh environments, chemical exposure, and temperature extremes. Choosing the right material is crucial,
as it directly affects the valve's longevity and performance. Experts recommend a stringent analysis of the operating environment before selecting the valve material to ensure compatibility and prevent premature failure.
Another significant aspect of actuated gate valves is the availability of different designs tailored to specific applications. For instance, rising stem gate valves are preferred when visual position indication is necessary, while non-rising stem versions are suitable for space-constrained installations. Additionally, the choice between wedge-shaped or parallel gate designs allows for further customization based on the application's pressure and flow requirements.
actuated gate valve
In terms of maintenance and reliability, actuated gate valves excel by requiring minimal upkeep compared to their manually operated counterparts. Their automated nature reduces wear and tear associated with manual operation, and many models incorporate self-diagnostic features that alert operators to performance issues before they escalate. Furthermore, the ease of integration with digital control systems allows for seamless monitoring and operation within larger automated networks, enhancing both control and accountability.
When considering the purchase of actuated gate valves, the expertise and reputation of the manufacturer play a critical role. Leading manufacturers often provide not only high-quality products but also comprehensive support services, including installation guidance, maintenance training, and troubleshooting assistance. Engaging with suppliers who offer these value-added services ensures that investments in actuated gate valves yield long-term benefits.
Trust in the technology is underscored by numerous real-world applications and case studies demonstrating the successful deployment of actuated gate valves in complex scenarios. Industries have consistently reported improved operational performance, reduced downtime, and lower maintenance costs due to the reliable function of these valves. This collective data strengthens confidence and advocates for the widespread adoption of actuated gate valves across various sectors.
In conclusion, actuated gate valves represent a sophisticated blend of precision engineering and practical application. Their versatility, coupled with advancements in actuation technology, makes them an indispensable component in modern industrial setups. By choosing the appropriate valve type, material, and actuator, businesses can significantly enhance their operational efficiency and ensure seamless flow control within their systems. The future of fluid control undeniably hinges on the continued development and integration of actuated gate valves, solidifying their role as a cornerstone of industrial operations.