Rubber joint expansion, an innovative product in the realm of industrial engineering, has become instrumental in various sectors due to its unparalleled flexibility and durability. These joints are not just components but are the lifeline of many piping systems, especially where vibration dampening and expansion control are required.
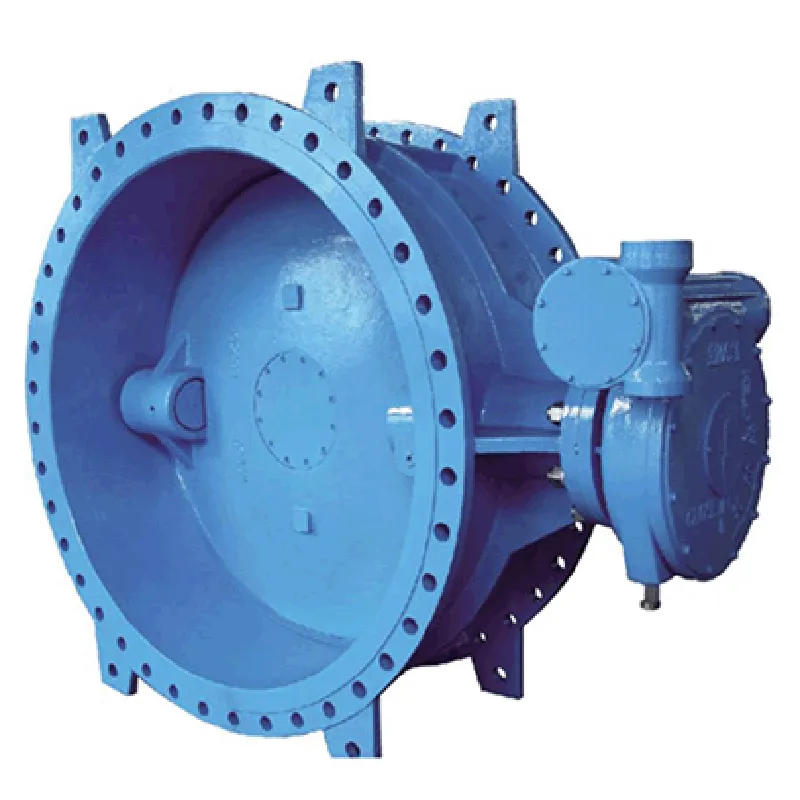
To understand the true essence of rubber joint expansion, it's essential to explore its practical applications across industries. In the world of HVAC systems, these joints allow for thermal expansion and contraction, which aids in maintaining system integrity by mitigating potential damage from temperature fluctuations. Their ability to absorb sound and vibration is particularly valuable in environments where machinery noise reduction is crucial.
In the oil and gas sector, rubber joint expansions are critical for safe pipeline operations. Given the extreme conditions and pressure variations within these pipelines, rubber joint expansions play a vital role in enhancing the longevity and reliability of the infrastructure. By compensating for pipe movements and deviations, they reduce the risk of leaks and ruptures, offering significant safety benefits.
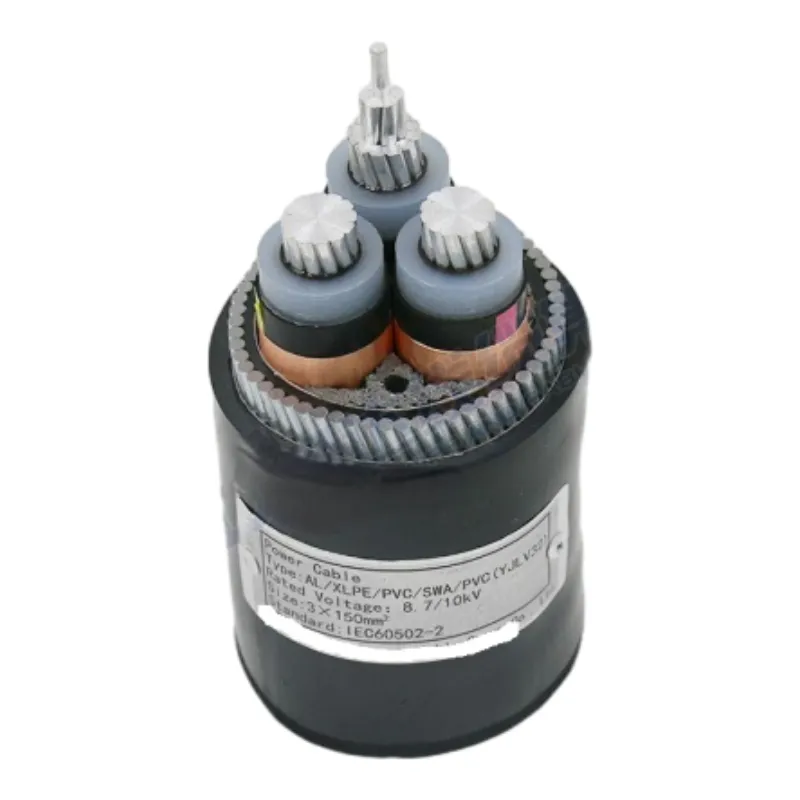
The water and wastewater industries also highly value rubber joint expansions. In these sectors, the joints manage thermal expansion, water hammer incidents, and mechanical vibration. This is particularly relevant where there are varying environmental conditions affecting the pipelines. The ability of rubber joint expansions to adjust to different pressures and directions of flow makes them indispensable to ensuring continuous operation without failures.
Experience reveals that the choice of rubber material is a cornerstone in the functionality of expansion joints. Selecting the right type of rubber—whether EPDM, NBR, or others—depends heavily on the medium that passes through the system and the specific environmental conditions encountered. For example, EPDM is lauded for its suitability in hot and cold water applications due to its excellent resistance to heat, ozone, and aging. NBR, on the other hand, is preferred where oil resistance is a priority.
rubber joint expansion
From an expertise standpoint, it's crucial to comprehend the installation nuances of rubber joint expansions. Proper installation prevents undue stress and potential damage to the joint and the piping system. This includes ensuring the joint is not overly stretched or compressed during installation and that the correct bolt torque is applied. These precautions enhance the lifespan of the joint and optimize performance.
Additionally, the authoritative insights from industry experts emphasize regular maintenance and inspection. Over time,
the wear and tear on a rubber joint can lead to compromised performance. Routine checks help detect early signs of fatigue or degradation, allowing for timely interventions before the situation demands costly repairs or replacements.
Trustworthiness in manufacturing rubber joint expansions is non-negotiable for brands looking to cement their reputation in the market. This is where adherence to international standards like the ASTM and ISO can highlight a manufacturer’s commitment to quality and safety. Certifications from reputable bodies reassure customers of the products' reliability which, in turn, fosters customer loyalty.
One must not overlook the future of rubber joint expansions, as technological strides promise to revolutionize this sector. The integration of smart sensors into expansion joints could provide real-time data and analytics, alerting operators to potential issues before they escalate. This preemptive approach would set a new benchmark for operational safety and efficiency.
In conclusion, the role of rubber joint expansions in various industries cannot be overstated. Their significance lies not only in their practical applications but also in the meticulous attention to material selection, installation practices, and routine maintenance that together ensure enduring performance. As industries evolve, rubber joint expansions will undoubtedly continue to adapt, meeting new demands with resilience and flexibility.