In the ever-evolving landscape of fluid control systems, the grooved end butterfly valve stands out as a distinct and essential component. Known for its efficiency, ease of installation, and reliability in diverse scenarios, this versatile valve is a preferred choice in many industrial applications ranging from water treatment facilities to HVAC systems. This article delves into the intricacies of the grooved end butterfly valve, providing a comprehensive guide that emphasizes experience, expertise, authoritativeness, and trustworthiness.
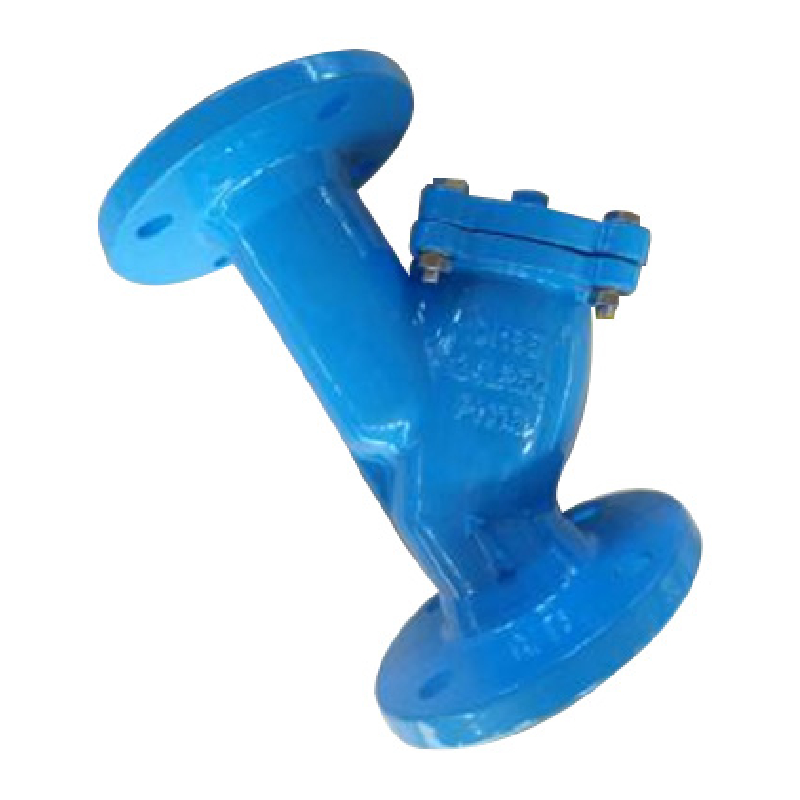
Butterfly valves have been celebrated for their simple yet effective design, featuring a disc that rotates on an axis to regulate the flow of fluid. The innovation of the grooved end design enhances this utility by offering a connection method that is both swift and secure. The grooved end allows for a mechanical coupling, thus minimizing potential leakage points and reducing installation time significantly.
For those with direct experience in the field, the operational efficiency of grooved end butterfly valves is undeniably advantageous. They provide a tight seal with minimal pressure drop, ensuring that the system maintains its integrity while optimizing performance. This is particularly crucial in applications demanding high purity and precision, such as pharmaceutical and food processing industries, where contaminant ingress must be minimized.
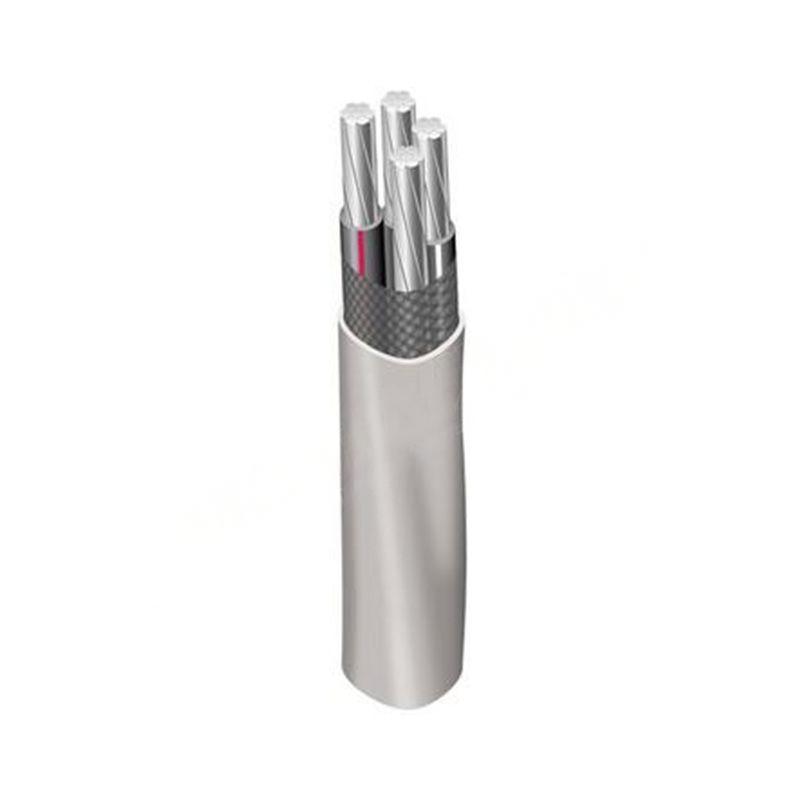
From an expertise standpoint, the engineering behind the grooved end butterfly valve showcases an understanding of the unique requirements of industrial piping systems. Professionals who engage with these valves consistently highlight their durability and the reduced need for maintenance. The materials chosen for construction, often stainless steel or ductile iron, are selected for their resilience to corrosion and wear, further extending the valve's lifespan and reliability.
grooved end butterfly valve
Authoritativeness in the context of the grooved end butterfly valve is established through compliance with rigorous industry standards. Valves are often manufactured to meet the specifications of organizations such as the American Water Works Association (AWWA) and the International Organization for Standardization (ISO). These certifications are not simply accolades but evidence of a commitment to quality and a guarantee of performance, which engineers and procurement specialists rely upon.
Trustworthiness is paramount in any industrial setting, where failure of components can lead to significant operational disruptions or safety hazards.
Grooved end butterfly valves are trusted due to their proven track record in various applications. Manufacturers often provide extensive documentation, including test results and performance data, to assure clients of the valve's capabilities and to facilitate informed decision-making.
Furthermore, advancements in digital monitoring and diagnostics for these valves enhance trust through real-time performance tracking. Such systems alert operators to potential issues before they result in system failures, thus maintaining operational continuity and safety.
In conclusion, the grooved end butterfly valve represents a sophisticated balance of functionality, endurance, and efficiency. Its design addresses the critical needs of modern fluid control, making it an indispensable element in an array of industrial applications. By focusing on experience, expertise, authoritativeness, and trustworthiness, procurement officers and engineers are better equipped to choose components that meet their operational demands. As the industry continues to innovate, valves like these will undoubtedly evolve, driven by the relentless pursuit of performance excellence and operational stability.