Selecting the right flap check valve is crucial for ensuring the efficiency and safety of fluid systems in various industries, including oil and gas, water treatment, and chemical processing. These valves, known for their simplicity and effectiveness, prevent the backflow of fluid by using a flapping mechanism that opens and closes as needed. Their design, resembling a hinged door, offers low resistance and minimal pressure drop, which is essential for maintaining system integrity.
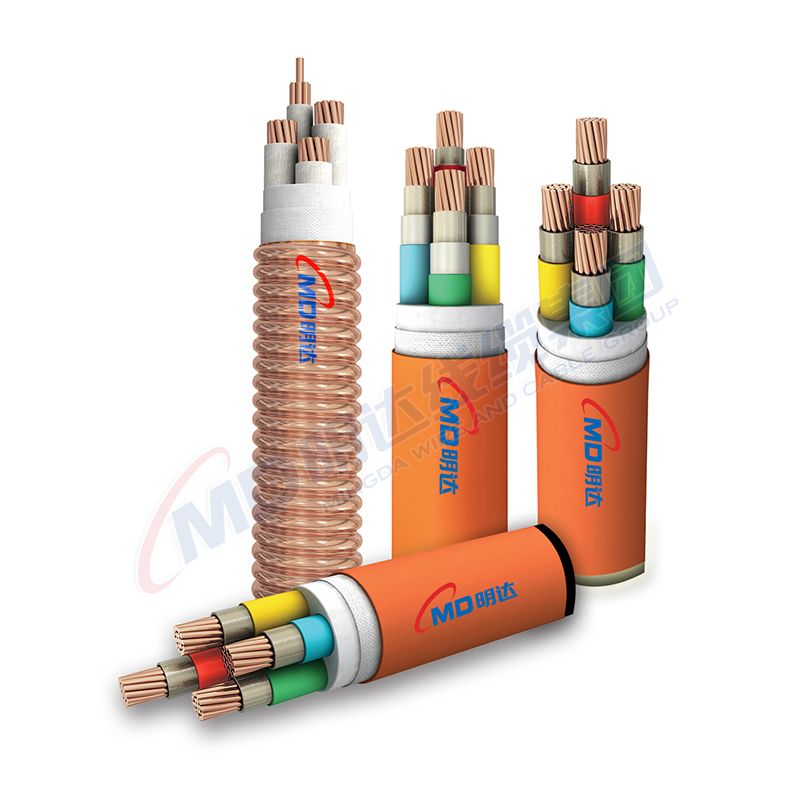
In-depth knowledge of flap check valves reveals a range of materials and configurations tailored to specific applications. Commonly constructed from materials such as stainless steel, cast iron, or bronze, these valves exhibit varying degrees of corrosion resistance and durability. Stainless steel flap check valves, for example, are particularly suited for corrosive environments due to their robust anti-corrosive properties, whereas cast iron variants might be preferable for general applications due to their cost-effectiveness and ample strength.
Flap check valves operate independently of external controls, relying on flow velocity and pressure differential to function. This autonomy simplifies maintenance and reduces potential points of failure—an attractive benefit for industries prioritizing reliability and safety. Furthermore, the design flexibility allows manufacturers to produce flap check valves in various sizes, accommodating everything from small-scale residential setups to massive industrial pipelines.
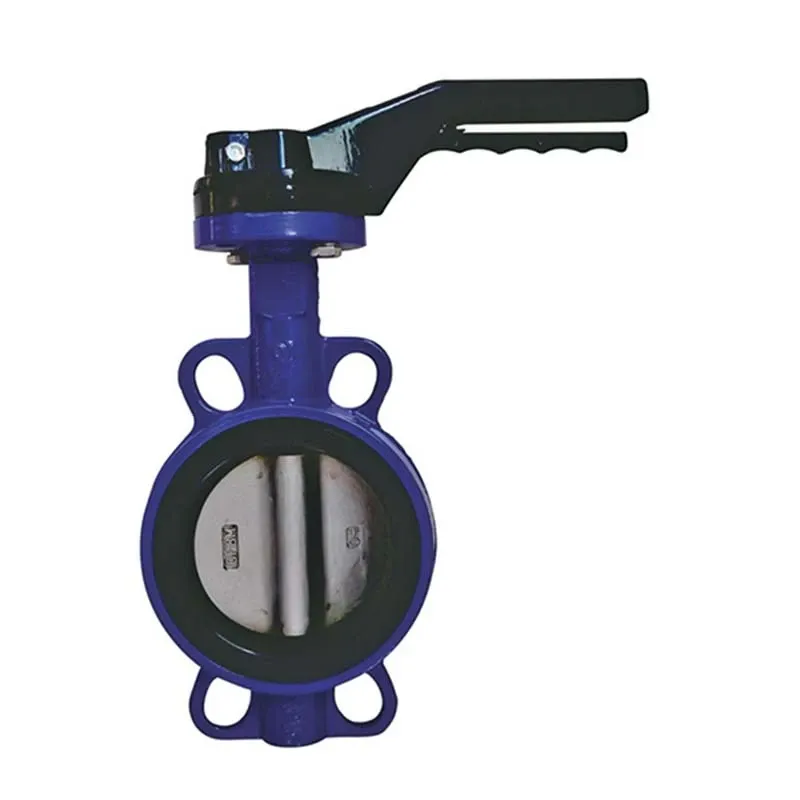
When selecting a flap check valve for a particular application, understanding the flow characteristics and pressure conditions is vital. Engineers often deploy computational fluid dynamics (CFD) simulations to predict how a specific valve will perform under different scenarios. These simulations provide insights into potential pressure losses, noise levels, and wear patterns, helping to optimize valve selection and placement within the system.
Additionally, innovations in valve technology are driving improvements in the performance and lifespan of flap check valves. Advances like enhanced elastomeric materials for valve seating and the integration of smart sensors offer real-time data on valve performance, increasing operational efficiency and allowing for predictive maintenance. These developments not only extend the lifecycle of the valve but also contribute to a reduction in overall maintenance costs and downtime.
flap check valve
The installation of a flap check valve must conform to best practices to ensure optimal performance. Incorrect installation can lead to issues such as water hammer or reverse flow, both of which can cause significant damage to the system. It is crucial to follow manufacturer guidelines, especially concerning the orientation and alignment of the valve. Routine inspections and testing should also form an integral part of the maintenance schedule, ensuring early detection of wear and potential seal failures.
Flap check valves also play an essential role in energy conservation within fluid systems. By preventing backflow without requiring external power sources, these valves help maintain system pressure, reducing the need for additional pumping energy. This attribute is particularly advantageous in large-scale operations, where energy savings translate directly into significant cost reductions and enhanced environmental sustainability.
Navigating the plethora of available options necessitates expert guidance from seasoned professionals who can interpret specific application needs and recommend the most appropriate valve solution. Trustworthy manufacturers and suppliers bring added value by providing technical support and ensuring compliance with industry standards, further ensuring the reliability and functionality of the valve in its operational environment.
In conclusion, the strategic use of flap check valves enhances system performance, mitigates risks, and supports the long-term sustainability of fluid handling operations. By leveraging advances in material science, design innovations, and industry expertise, businesses can optimize their fluid systems, ensuring safety, efficiency, and cost-effectiveness. Employing a flap check valve is not merely about selecting a component; it’s about fostering a system that reflects resilience, advanced engineering, and strategic foresight.