Navigating the myriad choices of wafer style check valves can be an intricate task, especially when so many aspects must align to meet specific project requirements. For those looking to optimize their systems for efficiency, reliability, and longevity, it's crucial to understand the unique characteristics and benefits of this essential component.

Wafer style check valves are known for their slim and compact build, which allows them to fit snugly between flanges without taking up extra space. This design makes them an ideal choice for systems where space is a premium commodity. Unlike traditional swing check valves, wafer style check valves are lighter, providing an effortless installation process. This attribute not only minimizes labor costs but also reduces wear on piping systems, thus prolonging their lifespan.
From an expertise standpoint, the wafer style check valve’s functionality is grounded in its simple yet effective design. These valves feature a disc that opens when the fluid pressure pushes against it and closes when backflow attempts to reverse the fluid path. This mechanism ensures a seamless operation with minimal pressure drop, enhancing overall efficiency. Engineers and system designers favor wafer style check valves for their ability to prevent backflow without the need for additional power or human intervention.
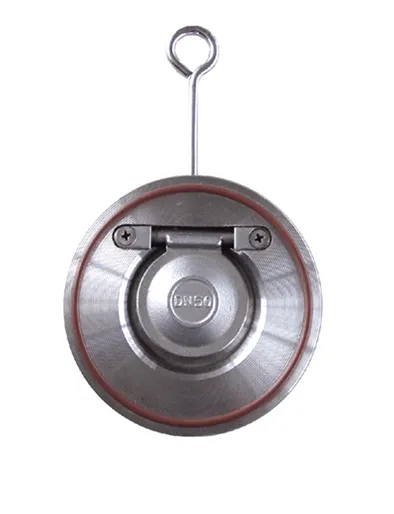
The material selection for wafer style check valves further enhances their practical benefits. Typically, these valves are made from durable materials such as stainless steel, ductile iron, or brass, each offering unique resistance to corrosion and temperature extremes. The choice of material is paramount, particularly in industries like chemical processing, oil and gas, and water treatment, where the valve's resilience to harsh environments directly impacts system safety and performance.
wafer style check valve
Authoritative voices in the field often highlight the importance of choosing a wafer style check valve with an appropriate pressure rating and size.
Misjudging these parameters can lead to poor performance and premature valve failure. Therefore, aligning the valve specifications with the system requirement ensures optimum performance. Industry experts often emphasize the need for comprehensive maintenance checks to prolong the functional life of the valve. A well-maintained valve not only guarantees reliability but also contributes to the sustainability of the entire system.
One common concern about wafer style check valves pertains to their sealing capacity, especially in applications with fluctuating pressures. However, advancements in valve technology have led to improvements such as the development of elastomer seats and precision-engineered discs, which provide enhanced sealing and reduce the risk of leakage even in challenging conditions. This innovation underscores the industry’s commitment to addressing customer pain points and improving overall trust in wafer check valve applications.
To address concerns regarding trustworthiness, many manufacturers offer robust warranties and have instituted rigorous quality assurance protocols. Reputable brands often provide detailed product documentation and testing certifications to reassure buyers of the valve's integrity and performance capabilities. As a standard practice, prospective buyers should consult these documents and perhaps reach out for independent reviews to ensure they are investing in a quality product that meets international standards.
In conclusion, wafer style check valves are a crucial component in various industrial applications, prized for their compact design, ease of installation, and reliable operation. Selecting the right valve involves understanding its design and material, ensuring compatibility with system requirements, and adhering to routine maintenance practices. By doing so, operators can achieve optimal system performance and mitigate the risks associated with backflow, thereby enhancing both safety and efficiency. The ongoing evolution and innovation within this field promise to further refine these valves, solidifying their status as a staple in flow control solutions.