Gate valves, specifically the non-rising stem (NRS) variants, are pivotal components in numerous industrial and residential applications. Known for their durability and efficiency in shutting off the flow of liquids, they often serve as the go-to solution where space constraints present challenges. Leveraging detailed technical knowledge and industry insights, this article aims to illuminate the unique features and advantages of using gate valve NRS models in varied settings.
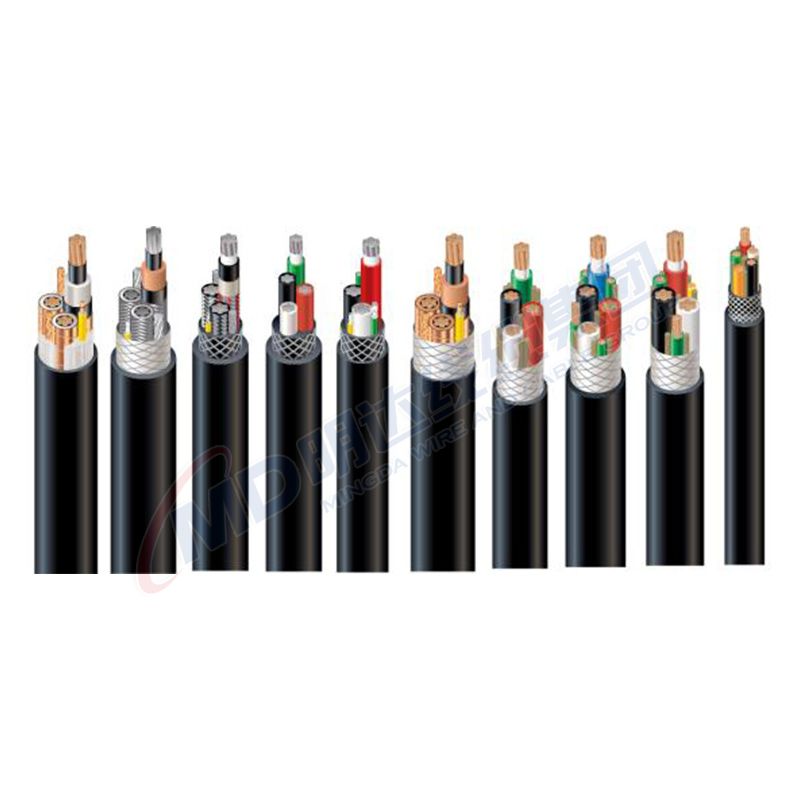
At their core, gate valves are designed to work in either a fully open or fully closed position. The non-rising stem feature distinguishes this category, where the stem does not travel up or down as the valve operates—a fundamental design that proves advantageous in cramped installations such as underground or in confined spaces where vertical space is a premium. By rotating the actuator, typically a handwheel, the valve disc moves parallel to the flow, enabling swift and precise control without necessitating additional room for stem travel.
Engineered for excellence, gate valve NRS models are constructed from robust materials, including stainless steel, cast iron, and ductile iron, ensuring longevity and minimal maintenance. Their corrosion-resistant properties make them ideal for applications involving corrosive fluids or exposure to harsh environmental conditions. Extensive testing and certification processes further solidify their reputation for reliability in critical infrastructure and industrial applications.
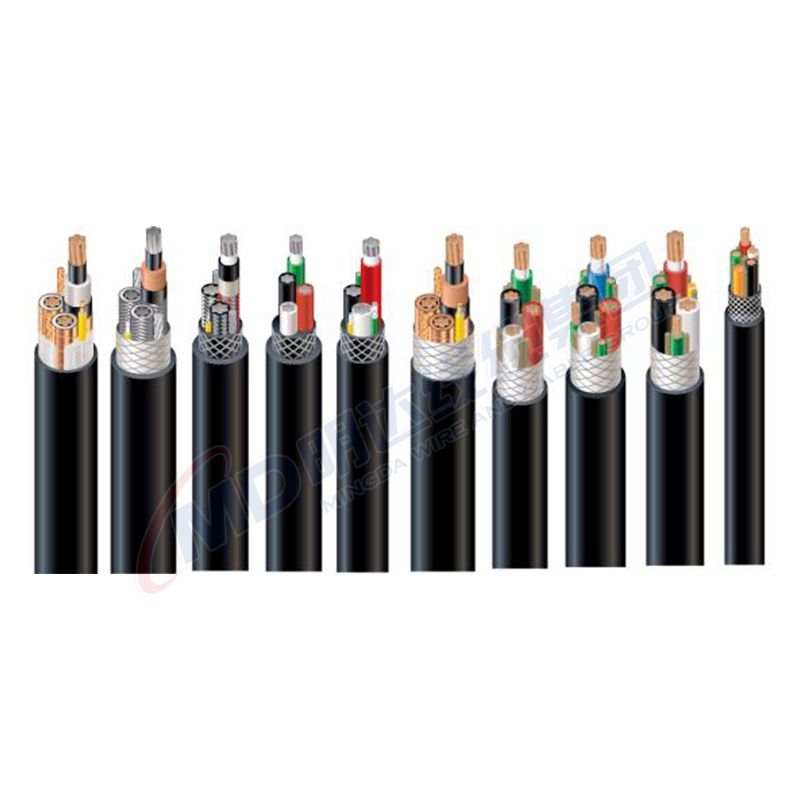
Professionals opt for gate valve NRS solutions in water treatment facilities, chemical plants, and fire protection systems, all demanding reliability and efficiency. Their ability to maintain consistent seal integrity across varying pressures and temperatures underscores their suitability for high-pressure environments. Additionally, the simplicity of the non-rising design contributes to reduced mechanical failure, a key factor in maintaining operational continuity in demanding industrial settings.
gate valve nrs
From an installation perspective, the compact nature of NRS gate valves simplifies the process, reducing costs related to labor and supporting structures. This efficiency is particularly beneficial in large industrial installations where optimizing space and resources is essential for operational efficacy. Furthermore, with fewer moving parts than alternatives, these valves minimize potential leak points, contributing to environmental and economic sustainability by reducing wastage.
Expertise in handling gate valve NRS systems also considers the ease of automation. These valves can be easily fitted with actuators for remote operation, integrating seamlessly into modern automated control systems. This adaptability is particularly valuable in industries where controlling fluid flow remotely is critical to maintaining system integrity and safety.
The knowledge and credible experience of industry specialists reinforce the trustworthiness of gate valve NRS implementations. Reports from field engineers and maintenance crews consistently highlight their performance under rigorous conditions, emphasizing resistance to wear, infrequent maintenance needs, and ease of inspection. This reliability aligns with industry standards set by authoritative bodies, ensuring compliance with safety and performance regulations critical in high-stakes environments.
In summary, gate valve NRS models offer a compelling solution for fluid control in contexts riddled with spatial and environmental challenges. Their robust design, resistance to harsh conditions, and adaptability in dynamic industrial landscapes validate their role as a trusted component in pipeline systems. As industries continue to innovate, the integration of these valves into smarter, more efficient infrastructure is only set to enhance operational effectiveness and environmental stewardship.