Wafer type butterfly valves have long emerged as a versatile and essential component in fluid control systems across a myriad of industries. As industries continuously evolve, the precision and efficiency of these valves have set the gold standard in engineering excellence, making them indispensable in modern-day applications.
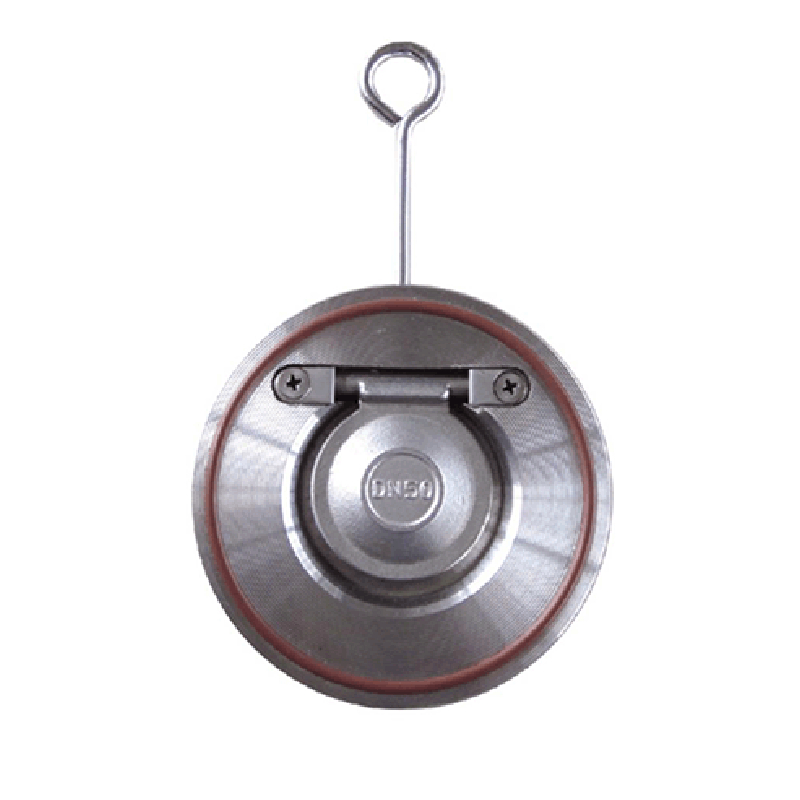
A wafer type butterfly valve is distinctively characterized by its slim, lightweight design and two-sided flanged ends, which allows for easy installation between pipes of various dimensions. Unlike lug type butterfly valves, wafer valves do not have threaded inserts, emphasizing their compact design that prevents complex installations, thus reducing costs and maintenance time significantly.
In the realm of experience, wafer type butterfly valves have demonstrated unparalleled adaptability in diverse operational conditions. Whether navigating high-pressure water supplies or delicate chemical processing tasks, their sealing integrity stands robust against leaks. Users have consistently noted the enhanced durability and prolonged lifespan of these valves, crediting advancements in seal materials and disc design for the sustained performance.
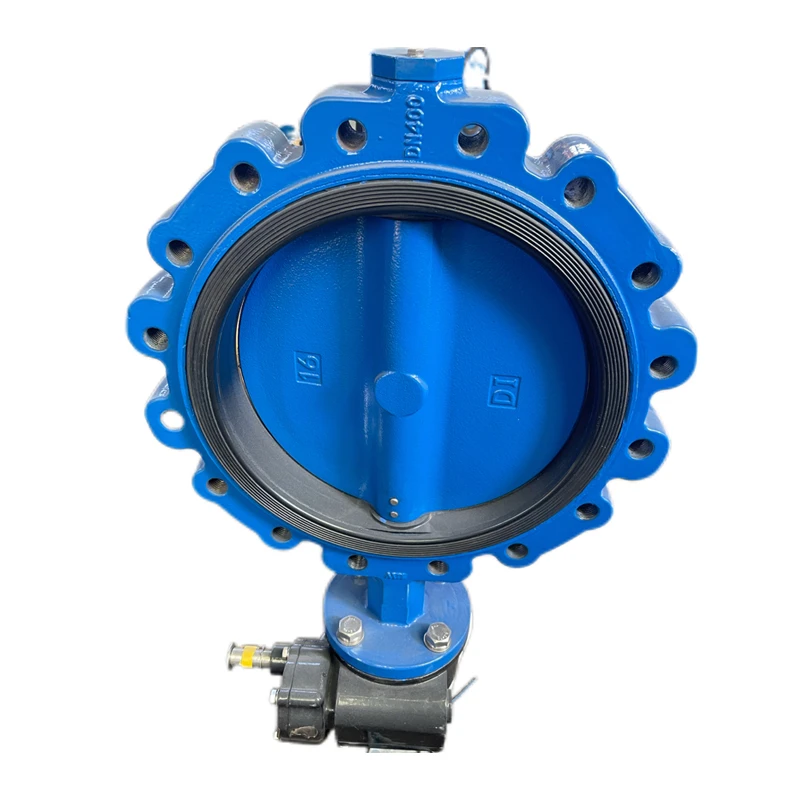
From an expertise perspective, engineers are frequently drawn to the wafer type butterfly valve for its engineering ingenuity. The central disc, pivotal in operation, is precision-engineered to rotate within the pipeline, effectively regulating flow with a mere quarter turn of the actuator. This innovative actuation design minimizes wear and tear, thus extending the functional life of the valve—a crucial consideration for industries seeking cost efficiency and reliability.
wafer type butterfly valve
The authority that wafer type butterfly valves command in fluid control systems is closely tied to both their proven track record and dynamic application range. Experts often cite their capacity to operate in tight spaces without compromising performance as a primary advantage over other valve types. Their presence in sectors such as water treatment, oil and gas, and chemical manufacturing underscores their pivotal role in ensuring the safe and efficient management of fluid systems. The breadth of their application across different industrial settings reinforces their status as an authoritative choice in flow control.
Trustworthiness is integral to any component used in critical systems, and here, wafer type butterfly valves excel. Made from high-grade materials such as stainless steel, ductile iron, or PVC, these valves assure users of exceptional reliability and resistance to corrosive elements. Moreover, the development of modern coatings and linings has further enhanced their operational efficacy and environmental resilience. Industries that operate within strict regulatory frameworks particularly value the consistent compliance and quality assurance that wafer type butterfly valves provide.
As technology continues to advance, the evolution and innovation of wafer type butterfly valves are poised to keep pace. Research advancements in material science are anticipated to further bolster their performance in extreme environments, aiming to address challenges related to temperature, friction, and chemical exposure. In addition, the integration of smart technology could advance their functionality, offering predictive maintenance insights, real-time monitoring, and automated adjustments—transforming these trusted components into intelligent solutions for tomorrow’s industrial challenges.
In summary, wafer type butterfly valves remain an archetype of engineering innovation and reliability, embodied by their efficiency, adaptability, and durability. By meeting the demanding needs of various industries through expert craftsmanship and authoritative performance, they continue to earn the trust and respect of engineers and users globally, epitomizing a seamless blend of tradition and technology in modern fluid control dynamics.