Flexible rubber joints, an essential component in modern industrial applications, have significantly revolutionized the way systems handle vibration, noise, and thermal expansion. As industries evolve, the demand for these components has surged due to their unique ability to provide durability and flexibility in various operating environments.
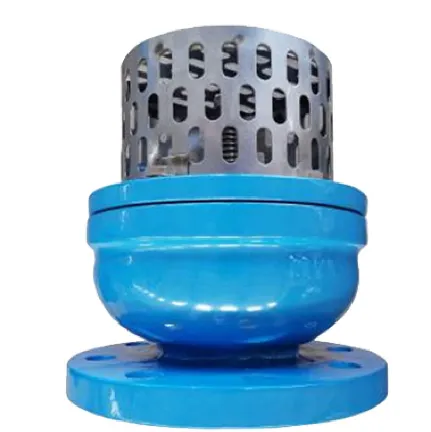
Understanding the core functionality of flexible rubber joints begins with recognizing their composition. Typically, these joints are made of high-quality elastomers, reinforced with synthetic fibers or metallic inserts, to enhance their performance under diverse conditions. This composition is not only strategic but scientifically engineered to address specific industrial needs such as equipment connection, vibration dampening, and misalignment accommodation.
From an experience standpoint, industries ranging from petrochemical to HVAC have extensively implemented flexible rubber joints. Their utility lies in their ability to absorb movements and stresses that would otherwise compromise rigid piping systems. For example, in the large-scale operations of chemical plants, these joints effectively compensate for system expansion and contraction due to temperature fluctuations. Technicians in these fields have reported significant reductions in maintenance downtimes and repairs, attributing this to the joints’ ability to diminish stress on connected equipment, thereby prolonging the overall system lifespan.
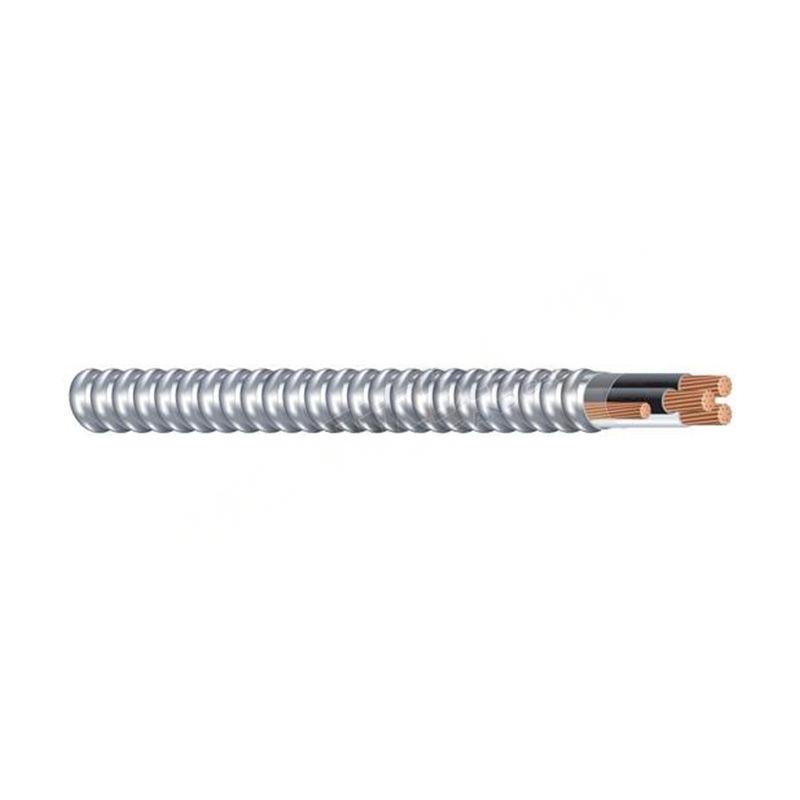
Expertise in the selection and application of these joints is paramount. Professionals in this domain emphasize the critical assessment of factors such as temperature range, pressure rating, chemical compatibility, and mechanical load when choosing the appropriate joint. Incorrect specifications can lead to premature failure, compromising not only the system’s efficiency but also safety standards. Therefore, manufacturers and suppliers often offer comprehensive guidelines and consultations to ensure the precise tailoring of products to specific applications.
flexible rubber joint
The authority of flexible rubber joints is reinforced by industry standards and certifications. Products that conform to standards such as ASTM, ISO, or EN are subject to rigorous testing and quality controls, ensuring they meet predefined criteria of reliability and safety. This adherence not only boosts confidence among end-users but also affirms the product’s performance consistency across different applications. Notably, several industry leaders recount successful integration stories where certified rubber joints have withstood challenging conditions, providing a testament to their robustness and reliability.
Trustworthiness in flexible rubber joints stems from the transparency and integrity of their production processes. Reputable manufacturers prioritize sustainable practices, sourcing materials that ensure minimal environmental impact while maintaining high-performance standards. Moreover, they provide extensive product documentation, customer support, and warranty options, enhancing consumer confidence. Users frequently commend these practices, acknowledging the reliability and trust they instill in the products they deploy.
In conclusion, the strategic deployment of flexible rubber joints offers myriad benefits across various industries. Their expert design and application not only alleviate operational stresses but also contribute significantly to the overall efficiency and safety of mechanical systems. As production technologies and standards continue to advance, flexible rubber joints will remain pivotal, serving as a testament to innovation in industrial solutions.