Ductile iron check valves are a remarkable product in the world of fluid control systems. These valves play a pivotal role by preventing the backflow of fluids, thereby protecting plumbing systems and machinery from potential damage. Let's delve into the details to better understand their practical applications, unique features, and the essential considerations for choosing the best ductile iron check valve for specific needs.
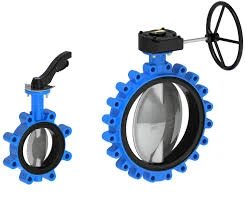
Ductile iron, an advanced form of cast iron, is fundamentally different from its traditional counterpart due to the presence of graphite in a nodular or spheroid form. This microstructure provides ductile iron with superior flexibility, strength, and impact resistance compared to regular cast iron. As a result, ductile iron check valves are distinguished by their durability and ability to withstand high pressure and temperature variations across numerous industrial applications.
In various industries, from water treatment facilities to chemical processing and oil refineries, ductile iron check valves offer reliability and efficiency. Their robustness makes them suitable for harsh environments, where they are exposed to corrosive materials and extreme operating conditions. This makes them highly valuable for ensuring safety and prolonging the lifespan of equipment.
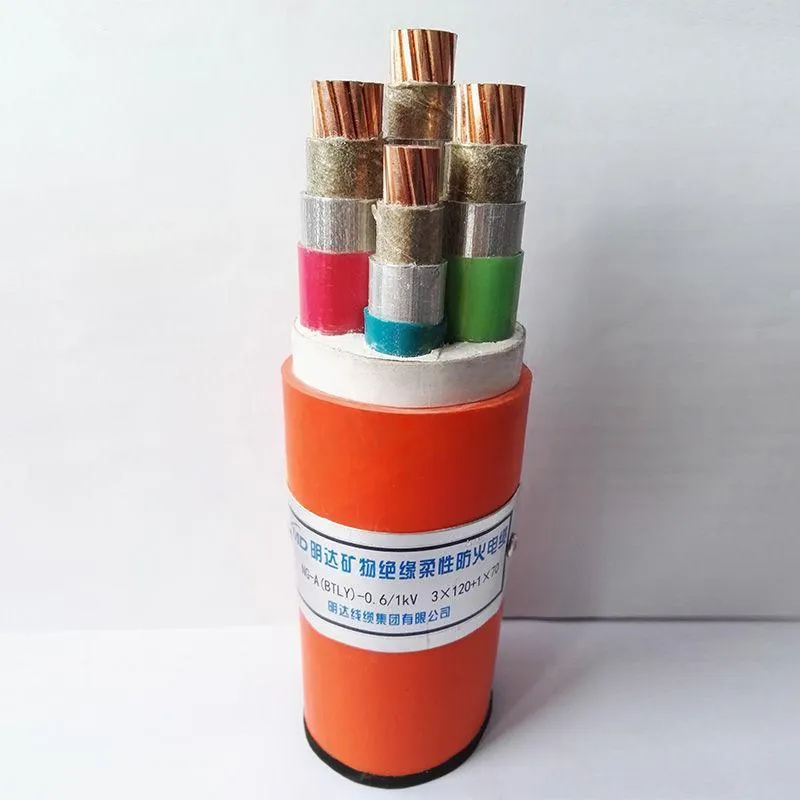
For those seeking to choose the best ductile iron check valve, specific parameters must be considered. The size and type of the valve are crucial, with options ranging from swing check to tilting disc, each suited for different applications and flow requirements. Swing check valves, for instance, are suitable for systems with a low flow velocity as they offer minimal turbulence. On the other hand, tilting disc check valves can manage higher flow rates and operating pressures efficiently.
Another key area of consideration is the coating and lining of the valve, which enhances its resistance to corrosive substances. An adequately coated valve can significantly prolong service life and maintain functionality in corrosive environments. Additionally, features such as low pressure drop are vital, ensuring that the valve does not hinder the system’s operational efficiency.
ductile iron check valve
Installation and maintenance aspects also contribute to the valve's overall performance and economic feasibility. Ease of installation is crucial as it impacts the downtime of operational activities. Furthermore, maintenance requirements should be minimal to ensure long-term sustainability without compromising safety and efficiency.
The expert consensus underscores the importance of compliance with international standards and certifications when selecting ductile iron check valves. Adherence to standards such as ANSI, ASTM, and ISO is a testament to the valve’s quality and reliability. These certifications serve to reassure that the product has undergone rigorous testing and meets the required safety and performance benchmarks.
The experience factor in utilizing these valves establishes their credibility within the industry. Case studies showcase their effectiveness, with countless industrial entities vouching for their performance and long-term benefits. From successful installation in municipal water systems to usage in large-scale manufacturing plants, the track record of ductile iron check valves speaks volumes about their dependability.
In conclusion, ductile iron check valves are an essential component in safeguarding systems from the detrimental effects of reverse flow, all the while ensuring operational efficiency and longevity. Their combination of durability, versatility, and economic feasibility makes them a prime choice across various industrial, commercial, and residential applications. As technological advancements continue to emerge, ductile iron check valves remain at the forefront, upholding unparalleled standards of safety and dependability in fluid control systems.