In the ever-evolving world of industrial valves, the wafer style butterfly valve emerges as a crucial player, bridging innovation and practicality. For industries ranging from water treatment to chemical processing, these valves provide an optimized solution for flow regulation that balances efficiency, durability, and cost-effectiveness.
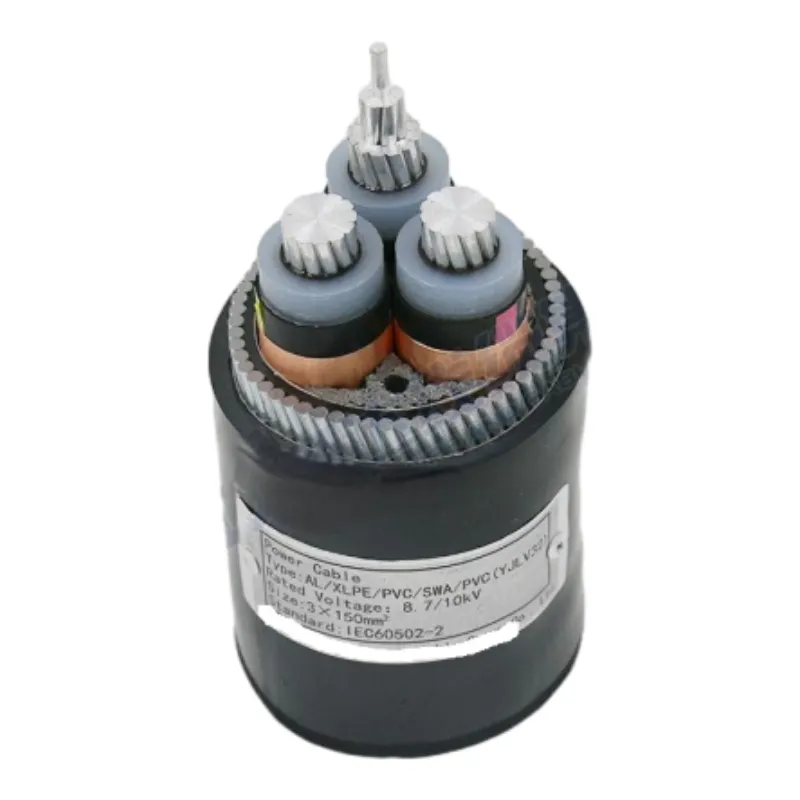
Wafer style butterfly valves are engineered with a slim profile that makes them an ideal choice for tight spaces and applications where weight is a concern.
Unlike flanged valves, the wafer style does not have bolt holes that go through the valve. Instead, it is designed with holes to align between pipe flanges, which are fastened against the valve without requiring additional support structures. This attribute makes the wafer butterfly valve lighter and generally more economical.
Experience using wafer style butterfly valves reveals their strengths in various applications. In water treatment facilities, for instance, operators have praised their ease of installation and maintenance. The lightweight design minimizes stress on piping structures and can significantly reduce material and labor costs. Additionally, the valve’s ability to open and close with a simple quarter-turn motion ensures efficient regulation of flow, which is vital in processes where water levels and quality must be precisely controlled.

Chemicals and process industries also benefit from the flexibility and reliability of wafer style butterfly valves. The valves are manufactured using materials that withstand corrosive or abrasive materials. Brands like Bray and Emerson have developed high-performance discs and seats that ensure long-term durability even in the most demanding environments. Users have reported improved operational efficiency thanks to the valve’s quick response and minimal pressure drop, boosting overall plant productivity.
From a technical standpoint, the expert design of wafer style butterfly valves is apparent in their streamlined construction, which minimizes pressure loss and maximizes flow capacity. The sophisticated designs typically include a resilient seated construction with an elastomer-lined body that ensures a tight seal to prevent leaks. This construction also allows for bidirectional service, providing flexibility in installation and application versatility.
wafer style butterfly valve
Companies manufacturing wafer style butterfly valves maintain a reputation for technical expertise and quality assurance, which instills confidence among users. Brands like Crane, Keystone, and Val-Matic adhere to rigorous manufacturing standards that comply with international quality certifications such as ISO 9001 and API. This commitment to quality is reflected in comprehensive testing protocols, including hydrostatic pressure and seat leakage tests, ensuring each valve meets the highest performance criteria before reaching the market.
Trust in wafer style butterfly valves is further solidified by the industry’s continued push toward innovation and customer-centered improvements. Modern advancements such as integration with smart technology now allow for remote monitoring and control, which adds a layer of operational efficiency and safety. Users can instantly identify and address potential issues through connected systems, reducing downtime and maintenance costs.
The authority of wafer style butterfly valves in the industrial market stems from decades of proven performance, customer satisfaction, and ongoing innovation. As industries increasingly prioritize sustainable and efficient operations, choosing reliable components like these valves is crucial. The enhanced control and durability they offer align perfectly with contemporary needs, supporting progress toward greener and more resilient infrastructures.
In conclusion, the wafer style butterfly valve sets the standard for versatility and efficiency in industrial applications. Its compact design, ease of installation, cost-effectiveness, and robust performance under challenging conditions make it an invaluable asset. As manufacturers and engineers continue to advance these valves' capabilities, they remain a testament to ingenuity in engineering and a cornerstone for efficient industrial flow management solutions.