Control valves are critical components in various industrial applications, each designed to efficiently regulate the flow of fluids, gases, or slurries through a system. As the unsung heroes of fluid dynamics, these devices ensure that processes run smoothly, safely, and within design parameters. This comprehensive guide delves into the nuanced world of control valves, highlighting the expertise, experience, reliability, and authority essential for making informed purchasing decisions.
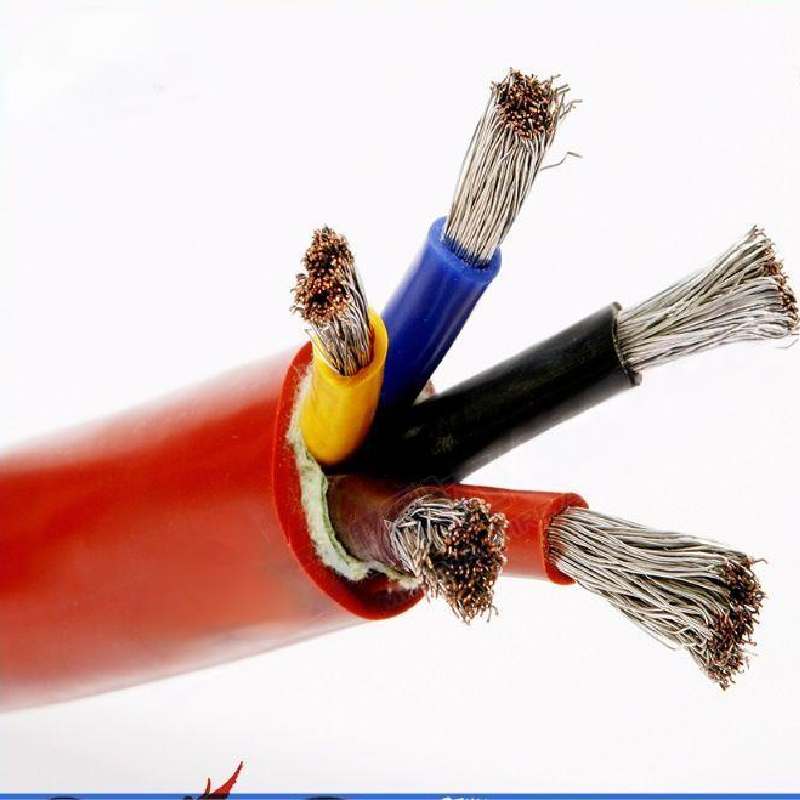
Control valves come in various shapes and sizes, each tailored to specific applications. A fundamental understanding of these categories—globe valves, ball valves, butterfly valves, and diaphragm valves—is vital for industry professionals seeking to optimize system performance. Globe valves, for instance, are widely appreciated for their excellent throttling capabilities and precise flow control, making them ideal for applications where accuracy is paramount. In contrast, ball valves, known for their durability and tight sealing, are preferable in applications requiring quick shut-offs and minimal leakage.
The expertise required to select and maintain the appropriate control valve cannot be understated. For instance, one must consider factors such as fluid characteristics, temperature, pressure drop, and desired flow capacity. Successful implementation relies heavily on understanding these parameters, as they influence valve sizing—a critical process that impacts performance and longevity. Oversized valves may result in poor regulation, while undersized ones can restrict flow and create pressure imbalances. Therefore, precise sizing, achieved through robust calculations and experience, is paramount.
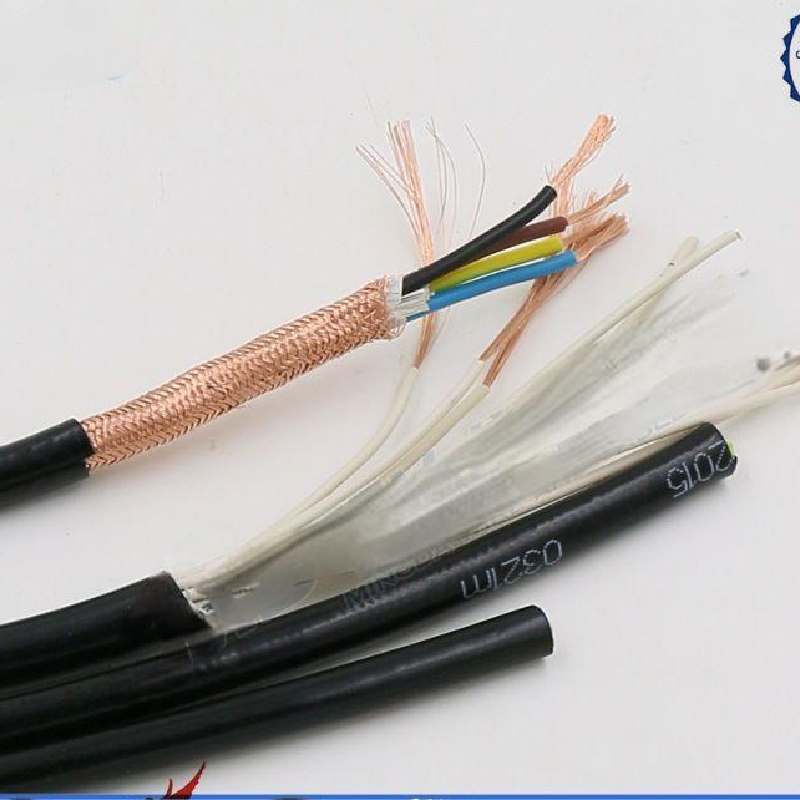
Moreover, the materials used for the construction of control valves define their applicability in specific environments. Corrosive fluids necessitate valves made from stainless steel, while abrasive slurries might require specialized coatings or hardened materials. Herein lies the authoritative knowledge necessary for industry leaders a deep comprehension of material science ensures they make investments that enhance durability and reduce lifecycle costs.
Control valve technologies have significantly advanced, incorporating smart technologies that align with Industry 4.
0 principles. Modern control valves are equipped with sensors and digital interfaces, allowing for real-time data analytics and predictive maintenance. These innovations lead to improved system reliability, as they provide insights into performance metrics and preempt potential failures. For professionals in the field, leveraging such technology not only optimizes operational efficiency but also fortifies their reputation as forward-thinking experts in fluid management.
control valve
Trustworthiness in control valve applications is reinforced by adherence to international standards and regulations, such as those set by the American National Standards Institute (ANSI) or the International Organization for Standardization (ISO). Compliance with these standards ensures that products are vetted against rigorous safety and quality criteria, offering peace of mind to users.
Furthermore, real-world experience often dictates the optimal choice of control valves far more effectively than theoretical knowledge alone. Industry veterans know that integrating field-tested solutions minimizes unforeseen issues during operation. For example, a well-designed control valve can withstand harsh environmental conditions, as exemplified in oil and gas applications where valves endure extreme pressures and temperatures.
Manufacturer reputation plays a substantial role in establishing product credibility. Companies with decades of innovation in control valve design and a commitment to research and development consistently produce superior products. Their expert engineering teams work alongside clients to tailor solutions, resulting in performance enhancements and operational success stories across diverse sectors like power generation, chemical processing, and water treatment.
To conclude, understanding the multifaceted nature of control valves, from selection and maintenance to material choice and cutting-edge technological integration, is essential for any professional in the industrial sector. It requires a synthesis of experience, specialized knowledge, and authoritative insight into both the technical and practical dimensions of valve operation. Only then can optimal performance and trustworthiness be consistently achieved, ensuring processes remain efficient, safe, and sustainable for years to come. With rigorous evaluation and strategic investment in quality control valves, professionals can drive innovation and success within their respective industries.