Air pressure valves are crucial components in a multitude of industries and applications, acting as the gatekeepers of pneumatic and hydraulic systems. Their essential function is to regulate, direct or control the flow of air by opening, closing, or partially obstructing pathways. Each air pressure valve is designed for specific conditions and purposes, making the selection process critical for optimal system performance.
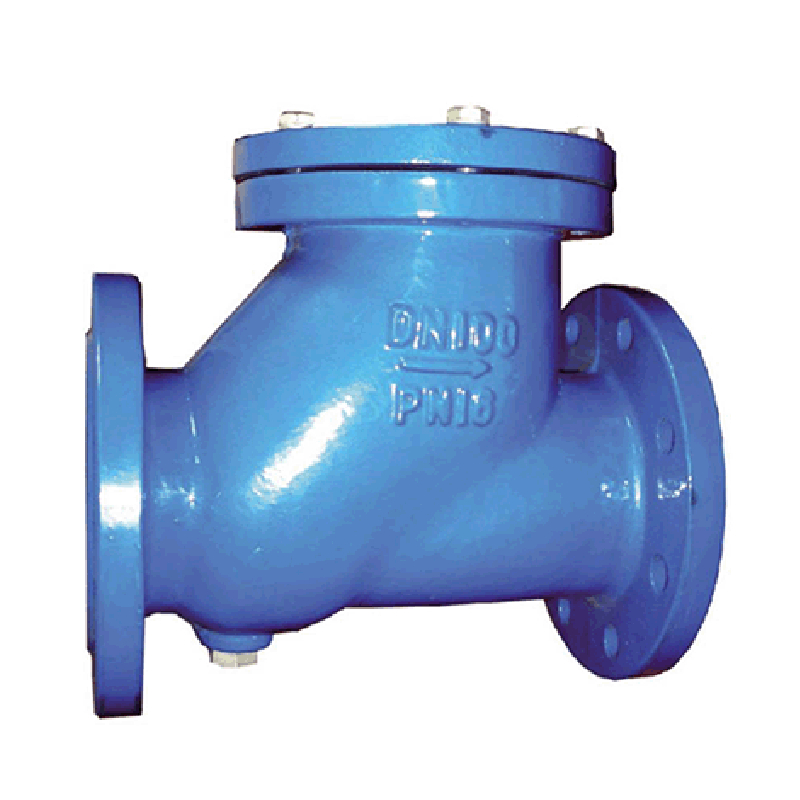
I recall a project I worked on in the aerospace industry where choosing the right air pressure valve was not just a matter of operational efficacy but also safety. An aircraft's pressurization system relies on air pressure valves to maintain cabin pressure, ensuring passengers' comfort and safety as the airplane ascends or descends. The precision required in these valves is a testament to their sophistication and critical importance in highly sensitive environments.
Diving deeper into the technicalities, air pressure valves are categorized into several types, each serving distinct roles—relief valves, reducing valves, shut-off valves, and sequence valves, among others. Relief valves, for instance, prevent systems from reaching unsafe pressure levels by opening at a predetermined set point and relieving excess pressure. On the other hand, reducing valves maintain a lower air pressure in a system to ensure equipment operates within specified limits. Understanding the nuanced roles of these valves underpins their expertise-oriented applications across industries.
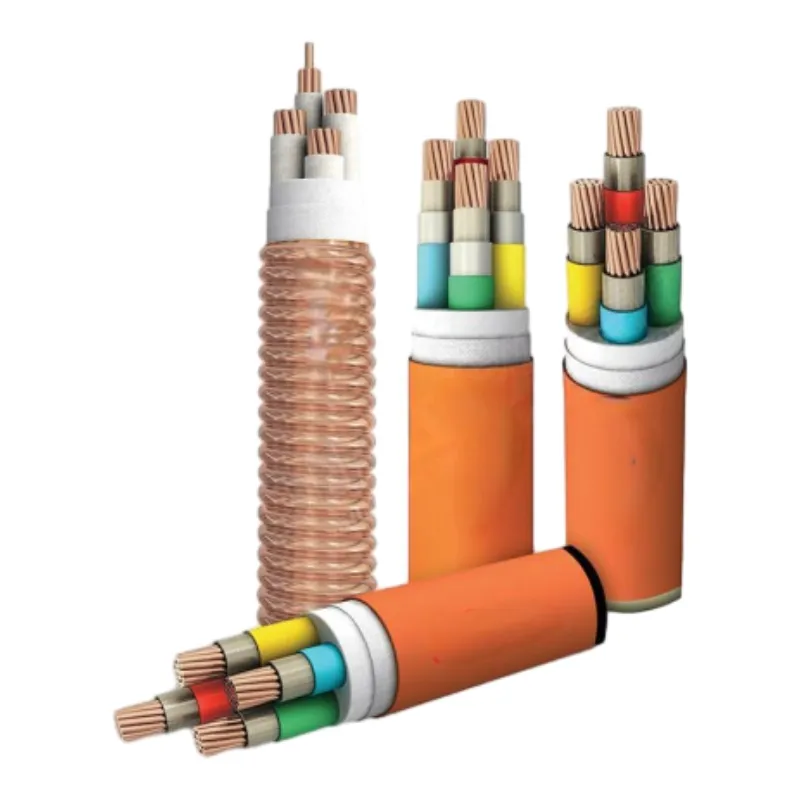
Expertise in selecting and maintaining air pressure valves is built on a foundation of authoritative knowledge. Understanding characteristics such as material compatibility, pressure rating, flow coefficient, and the operating environment is essential. For example, a valve made of stainless steel is preferred in corrosive environments, whereas lightweight aluminum might be suitable for less aggressive conditions. The valve's pressure rating must align with the system's maximum operating pressure to avoid catastrophic failures.
air pressure valve
Trustworthiness is an integral quality for both the valve and the provider. Precision-engineered valves from reputable manufacturers come with certifications and compliance with international standards such as ASME, API, or ISO. This reliability extends beyond product specifications; it encompasses the manufacturer's track record in innovation, customer support, and post-sale service. In the industrial equipment market, longstanding manufacturers like Parker Hannifin or Bosch Rexroth are often sought after due to their established credibility and wide-ranging expertise.
From an experience standpoint, proactive maintenance is the linchpin for extending the service life of air pressure valves. Regular inspections to identify wear, corrosion, or blockages can preempt malfunctions. Our ongoing maintenance contracts have frequently highlighted the importance of maintaining an inventory of critical spares, ensuring systems remain operational without extensive downtime in the case of a valve failure.
In conclusion, the significance of air pressure valves cannot be overstated within systems dependent on dynamic air flow control. Their selection and upkeep require a blend of experience, expertise, authoritativeness, and trustworthiness. Companies that prioritize these elements in their engineering and maintenance paradigms will enjoy enhanced operational safety, efficiency, and longevity of their equipment. By focusing on these pillars, we not only uphold the highest standards of quality and reliability but also build robust, trusting relationships with our partners and clients who rely on these integral system components.