Metal seat gate valves represent a pinnacle in industrial fluid control systems, embodying reliability and durability for handling demanding environments. These valves are renowned for their ability to withstand high pressures, temperatures, and abrasive materials, making them a preferred choice across various sectors such as petrochemical, power generation, and wastewater management. Understanding the nuanced capabilities and applications of metal seat gate valves can significantly bolster a facility’s operational efficiency.
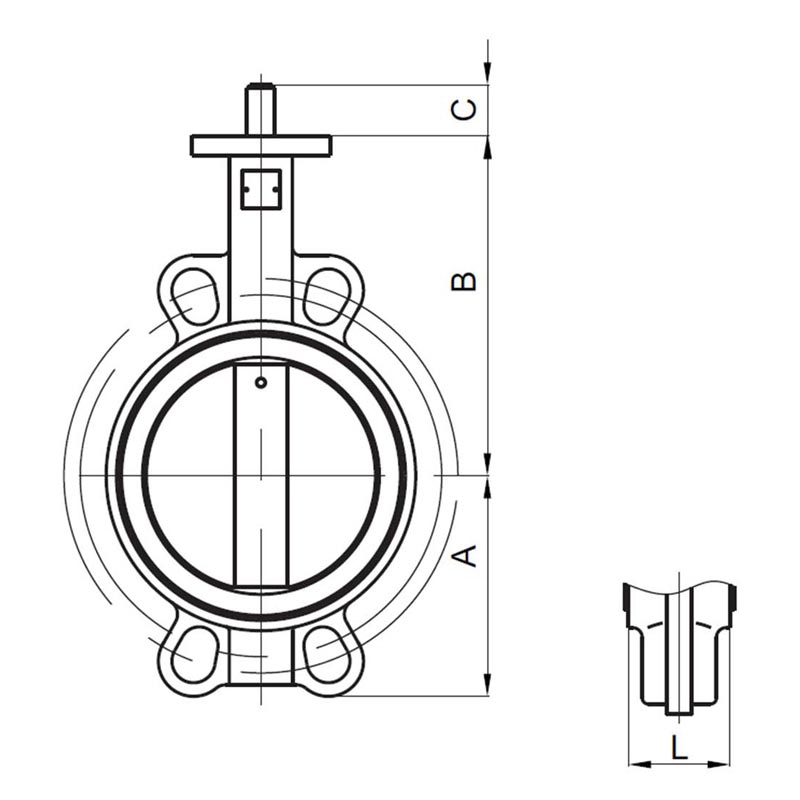
One of the key advantages of metal seat gate valves lies in their robust construction. Unlike their soft-seated counterparts, metal seat valves utilize strong alloy materials, which allow them to resist wear and tear even under extreme conditions. This resilience ensures a longer service life and reduces the frequency of maintenance interventions, which is a crucial consideration in operations where maintaining uptime is paramount. Furthermore, the use of metallic seats in these valves ensures a tight, reliable shutoff essential for preventing leaks that could lead to costly downtimes or safety hazards.
In terms of application, metal seat gate valves excel in environments where high-temperature fluids are present. For instance, in the petrochemical industry, where processes often involve the movement of corrosive and viscous materials, the durability of metal seats ensures optimal performance and safety. Additionally, these valves can withstand severe temperature fluctuations which can otherwise compromise valve integrity. Hence, facilities can maintain operational continuity without the need for frequent replacements or repairs.
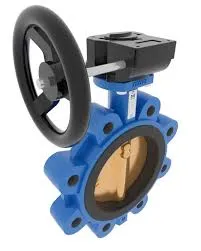
From an expertise standpoint, selecting the appropriate metal seat gate valve demands a keen understanding of the materials and engineering design. For industries dealing with highly corrosive media, materials such as stainless steel or Hastelloy might be preferable due to their superior resistance to chemical attack. Similarly, in high thermal stress applications, employing valves with coatings designed to manage heat expansion can prevent seat deformation, aligning with the precision necessary for industrial processes.
Another critical factor is the valve’s sizing and pressure rating. Professionals must accurately evaluate the operational parameters and select a valve that can seamlessly handle the expected load without foregoing efficiency or safety. An authoritative knowledge of fluid dynamics and engineering principles can assist in making informed decisions that not only optimize performance but also comply with industry regulations and standards.
metal seat gate valve
Trustworthiness in metal seat gate valves also involves understanding and adhering to stringent manufacturing standards. Reputable manufacturers ensure that their products meet international certifications, which are essential for assuring buyers of the integrity and reliability of the valves they are purchasing. These certifications often encompass performance testing, material evaluation, and safety compliance, thus enhancing the buyer’s trust in the product’s efficacy for their specific applications.
Furthermore, a trusted metal seat gate valve supplier typically offers extended warranties and comprehensive after-sales support, highlighting their confidence in the product’s performance and longevity. This support can be a deciding factor for facilities seeking reliable partners to maintain the smooth operation of their systems.
In terms of real-world experience, case studies often provide compelling evidence of metal seat gate valves’ effectiveness. For instance, power plants employing such valves have reported significant reductions in maintenance downtime, translating into cost savings and improved productivity. Furthermore, industries faced with stringent environmental regulations have found that metal seat valves help maintain compliance due to their leak-proof nature, thus mitigating the risk of environmental harm.
Ultimately, the selection of metal seat gate valves is not merely a transactional decision but a strategic one, emphasizing the balance between cost, performance, and long-term operational goals. Engaging with expert consultants and leveraging authoritative resources can aid in navigating the complexities associated with these valves, ensuring a decision that is both informed and strategically sound.
In conclusion, metal seat gate valves are a cornerstone of industrial fluid control, and their adoption can represent a significant upgrade in a facility’s capacity to handle demanding operational conditions. Their robust nature, combined with expert insights into their application, material selection, and compliance, makes them indispensable to industries aiming to enhance efficiency, safety, and reliability.