For professionals and industries dependent on managing fluid systems, the choice of components like air valves plays a crucial role in ensuring operational efficiency and safety. In particular, the di air valve has emerged as a vital component in varied applications, from HVAC systems to industrial pipelines.
Understanding its function, benefits, and selection criteria is essential to leveraging its full potential.
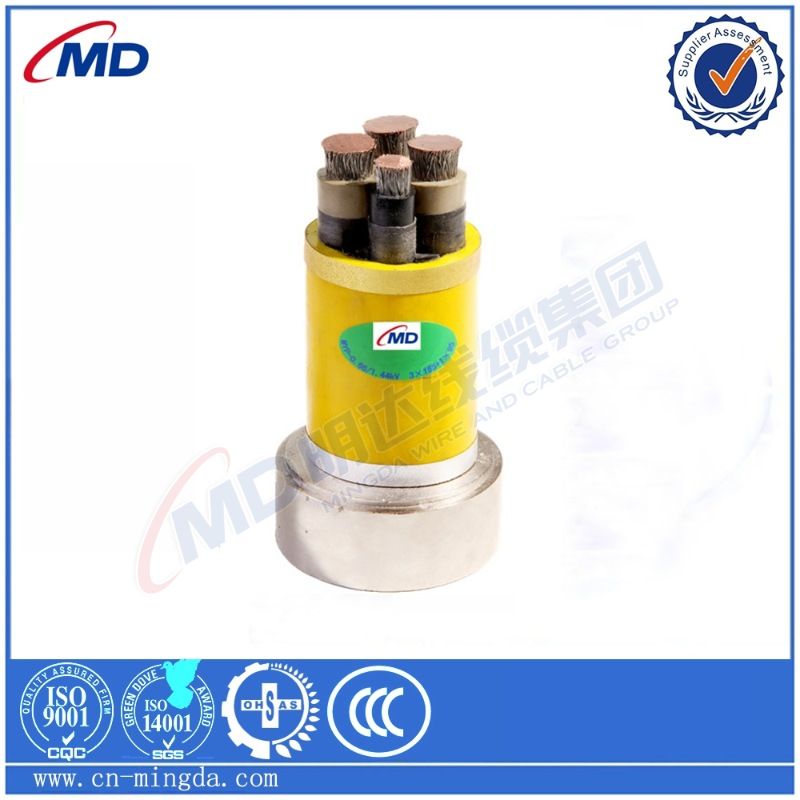
First, it's important to clarify what distinguishes a di air valve from other types. Designed specifically for dynamic situations, the di air valve excels in managing pressure and accommodating changes in volume within closed systems. Unlike static valves, it responds actively to fluctuations, ensuring that excess air is expelled and that vacuum conditions do not compromise the system's integrity. This dynamic response makes it indispensable in systems where pressure changes are frequent and can lead to inefficiencies or equipment damage if not properly managed.
Incorporating real-world experiences from industries utilizing these valves provides practical insights into their benefits. For instance, many HVAC engineers have reported significant improvements in system longevity and energy efficiency after retrofitting their setups with di air valves. By preventing airlock and maintaining optimal fluid levels, these valves help HVAC systems to operate more smoothly, reducing wear and tear on constituent components. This, in turn, lowers maintenance costs and extends the equipment's lifecycle.
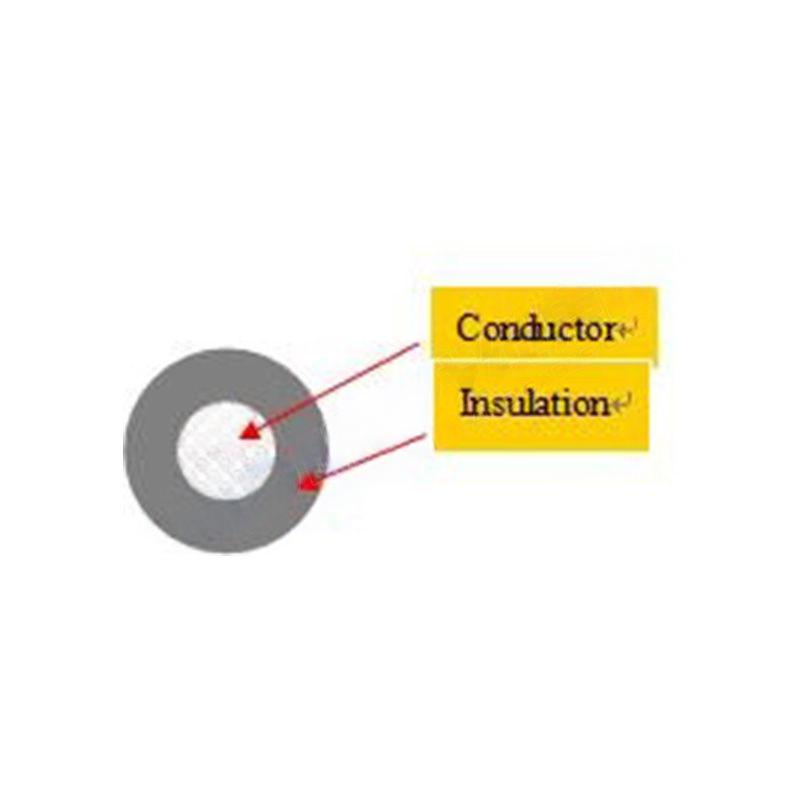
From an expertise standpoint, selecting the right di air valve is contingent upon understanding specific system requirements. Professionals recommend conducting a thorough analysis of the system's operational parameters, including maximum and minimum pressures, fluid composition, and temperature ranges. Additionally, attention must be paid to the valve's construction materials, which should be compatible with the system's fluid type to prevent corrosion and ensure durability. Materials like stainless steel and durable polymers are often preferred for their resilience and longevity.
di air valve
On the authority front, industry standards and certifications provide a benchmark for quality and reliability in di air valves. These standards, set by organizations such as the American Society of Mechanical Engineers (ASME) and the International Organization for Standardization (ISO), ensure that valves meet rigorous safety and performance criteria. Manufacturers who adhere to these standards not only demonstrate their commitment to quality but also offer customers a level of assurance in the valve's performance. It's advisable to select products with certifications that align with the operational and safety requirements of your specific application.
Trustworthiness in the context of di air valves is built through a combination of product transparency, customer support, and a strong track record. Companies that offer detailed product documentation, including data sheets and installation guides, enable users to make informed decisions. Additionally, it's beneficial to choose manufacturers that provide comprehensive after-sales support, including installation advice and troubleshooting assistance. Positive customer reviews and case studies that highlight the valve's performance in similar applications can also enhance confidence in the product's capabilities.
In conclusion, leveraging the advantages of di air valves requires a combination of practical experience, technical expertise, adherence to industry standards, and trust in the manufacturer's support and product transparency. By addressing these four key indicators—Experience, Expertise, Authoritativeness, and Trustworthiness—users can ensure their selection of di air valves maximizes system efficiency, safety, and reliability. As these valves become a staple in modern fluid systems, embracing these best practices will not only optimize performance but also contribute to sustainable and cost-effective operations.