Pneumatic butterfly valves have revolutionized fluid and gas flow management systems across a multitude of industries. Not merely an industrial accessory, these devices ensure seamless operations in environments that prioritize efficiency, reliability, and precision. Their rising prominence is not just a testament to innovative engineering but also a reflection of their adaptability in various application-specific challenges.
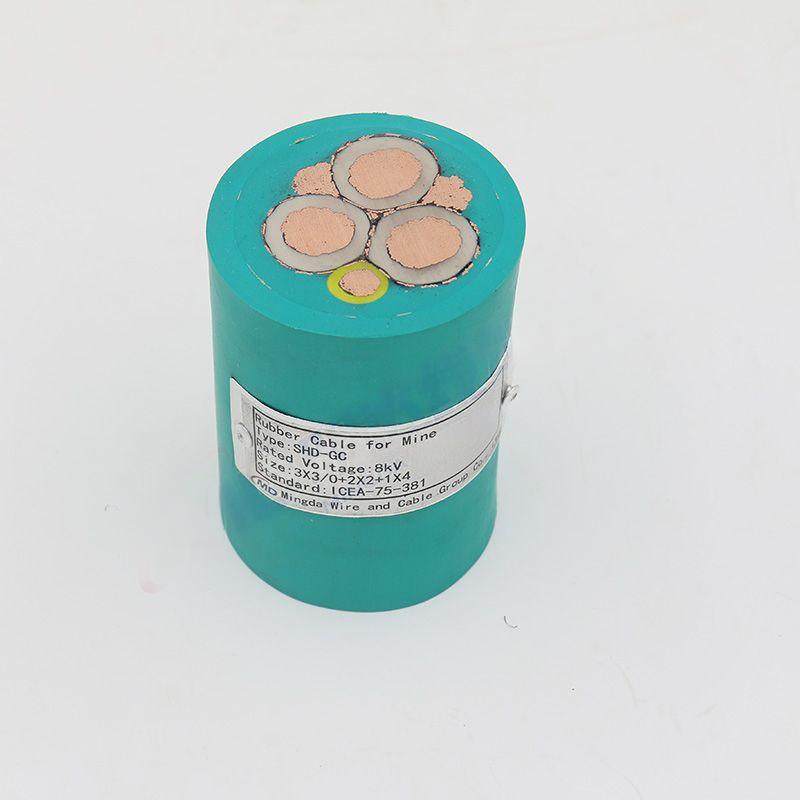
Experience in diverse industrial settings affirms that pneumatic butterfly valves outperform many traditional alternatives. For instance, in the field of water treatment facilities, they operate with remarkable efficiency. The streamlined design of the valve disc and its ability to rotate to a full 90 degrees allows for quick shut-off operations. Unlike gate valves that might take multiple turns to fully open or close, the pneumatic butterfly valve minimizes system downtime and extends operational continuity, a critical factor in facilities where every second counts.
From an expertise perspective, understanding the materials used in the construction of these valves is essential. The choice of materials such as stainless steel, cast iron, or PVC hinges on the specific application demands. For chemical processing plants, materials resistant to corrosion and chemical reactions ensure longevity and safety, vital aspects when dealing with hazardous substances. The engineering behind these valves also incorporates advanced sealing mechanisms. Enhanced sealing ensures zero leakage—a crucial consideration for industries where even minimal leakage can result in significant losses or dangers. This expertise in material science and engineering design underscores their effectiveness in high-stakes environments.

The authoritativeness of pneumatic butterfly valves is evident in their widespread adoption and rigorous performance requirements stipulated by industry standards. Adhering to standard certifications such as those from the American Society of Mechanical Engineers (ASME) and the International Organization for Standardization (ISO) further speaks to their quality and reliability. These certifications not only confirm the valves' capacity to perform under prescribed conditions but also assure buyers and engineers of their durability and robustness.
pneumatic butterfly valve
Trustworthiness in pneumatic butterfly valves is augmented by testimonies and case studies from trustworthy industry leaders who have successfully integrated these components into their systems. Companies in the oil and gas sector, for example, rely heavily on pneumatic butterfly valves for their offshore and onshore plants. Their ability to sustain high pressure and operate within stringent safety parameters is crucial. Real-world applications have shown that these valves significantly reduce maintenance costs and operational inefficiencies, a trust built through consistent performance and safety assurance.
For enterprises venturing into the selection and application of pneumatic butterfly valves, several factors must be considered to optimize the benefits thereof. It is vital to assess the operational requirements, including pressure and temperature ratings, to ensure that the selected valve meets the necessary specifications. Engaging with manufacturers who offer technical support and customization ensures that the valves are tailored to the unique requirements of each system. Moreover, leveraging automation—for instance, through integration with SCADA systems—can enhance the operational efficiency of these valves, allowing for real-time monitoring and remote control. This integration is particularly beneficial in reducing the manpower required for manual valve operation, thereby minimizing human error and enhancing overall system precision.
In conclusion, pneumatic butterfly valves stand as a paragon of modern fluid dynamics control, serving a diverse range of industrial applications with efficacy and precision. They are a balanced amalgamation of innovative design, material expertise, authoritative standards compliance, and operational trustworthiness. As technologies advance and industry needs evolve, these valves not only meet but exceed the expectations set upon them, rendering them an indispensable asset in the toolkit of any modern industrial operation. Understanding and leveraging their capabilities can lead to enhanced operational outcomes, reinforcing their status not simply as mechanical components, but as pivotal partners in industrial success.