In the ever-evolving landscape of industrial automation, the pneumatic ball valve has emerged as a critical component, offering seamless control and efficiency. This article delves into the intricacies of pneumatic ball valves, underscoring their indispensability in modern engineering and manufacturing processes.
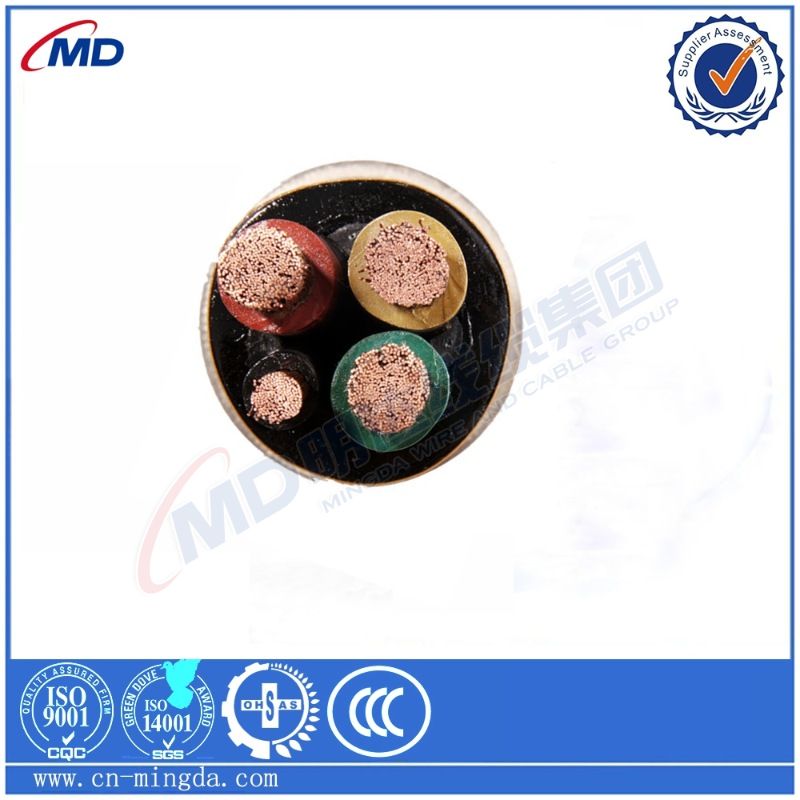
Pneumatic ball valves are heralded for their precision and durability, making them a staple in industries where fluid control is paramount. Unlike manual valves, pneumatic ball valves leverage compressed air to operate, offering automated control that is both quick and reliable. This ability to automate not only streamlines operations but significantly reduces human error, enhancing overall efficiency and safety.
From a technical standpoint, the design of pneumatic ball valves is a testament to engineering excellence. The ball mechanism, typically made of robust materials like stainless steel or brass, rotates to allow or block fluid flow. This simple yet effective design ensures a tight seal, reducing the risk of leaks. Additionally, the pneumatic actuator, the component responsible for converting compressed air into mechanical motion, can be precisely controlled, allowing for variable valve positioning. This precision ensures that fluid can be controlled at varying levels, crucial for applications requiring exact flow rates.
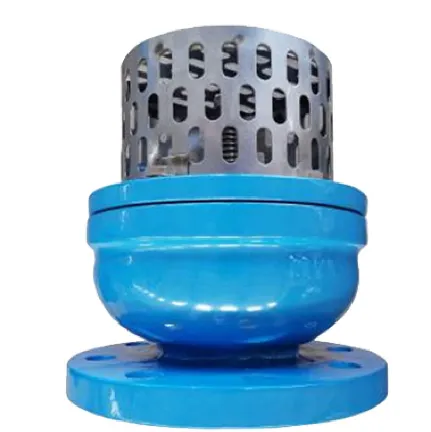
The expertise required to manufacture and implement pneumatic ball valves cannot be overstated. Precision engineering ensures that each valve functions optimally under significant pressure, a necessity given that these valves are often used in high-stakes environments such as chemical processing plants and water treatment facilities. Manufacturers invest heavily in research and development, testing each valve under stringent conditions to guarantee resilience and performance. This rigorous testing and quality assurance process stages pneumatic ball valves as highly reliable components trusted by engineers worldwide.
pneumatic ball valve
Authoritativeness in the field is reflected through the adherence to industry standards and certifications. Leading manufacturers of pneumatic ball valves abide by standards set by organizations such as the American Petroleum Institute (API) and the American Society of Mechanical Engineers (ASME). Such certifications assure buyers of the product’s credibility, providing peace of mind that their operations are supported by components that meet the highest industry benchmarks.
Trust is a cornerstone in industries where pneumatic ball valves play a critical role. Given the environments in which these valves operate—often involving hazardous or sensitive materials—trust in their ability to perform consistently is non-negotiable. Engineers and operators place faith in these valves to maintain the integrity of complex systems, relying on their reputations to prevent costly downtimes or, worse, catastrophic failures. Therefore, transparency in manufacturing processes and diligent customer support fortifies this trust, ensuring long-lasting relationships between manufacturers and clients.
Practically, the application of pneumatic ball valves traverses a myriad of industries. In oil and gas, they regulate the flow of crude oil and natural gas efficiently. In wastewater management, they control the treatment processes crucial for environmental protection. In the pharmaceutical sector, their precise regulation assists in maintaining the purity and quality of products. Each application underscores the versatility and adaptability of pneumatic ball valves, cementing their role as a vital tool in modern industrial applications.
In conclusion, the pneumatic ball valve exemplifies the principles of Experience, Expertise, Authoritativeness, and Trustworthiness. From their sophisticated design and engineering to rigorous testing and industry compliance, these valves demonstrate unrivaled reliability and precision. For businesses seeking to enhance their operational efficacy and safety, investing in pneumatic ball valves is not merely an option—it is a necessity. As industries continue to evolve, the role of these valves will only become more pronounced, driven by an ever-increasing demand for precision, safety, and efficiency.