The importance of choosing the right ball valve for any industrial application cannot be overstated. Ball valves, with their compact design, efficiency, and reliability, hold a pivotal role in operations ranging from residential water systems to complex, high-pressure industrial settings. Delving into the intricacies of ball valves requires an understanding rooted in comprehensive experience and professional expertise, focused on ensuring technical performance and long-term trustworthiness.
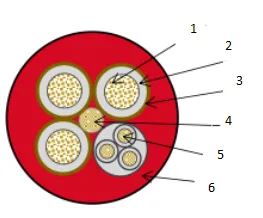
Ball valves, primarily utilized for on-off service, are designed with a pivoting ball to control the flow of liquid or gas through it. Their operation is straightforward, involving a simple quarter-turn motion to open or close the mechanism. This simplicity in design lends itself to fewer internal components, thereby reducing the potential for failure. But beyond their basic design sits a remarkably robust array of factors that influence their effectiveness and reliability in commercial or industrial settings.
Expertise in material selection is crucial when it comes to optimizing the performance of ball valves. Stainless steel, for instance, offers superior strength and resistance to corrosion, making it ideal for most industrial applications. For applications involving highly corrosive materials, other options like titanium or advanced alloys may be more suitable. The selection of materials directly impacts the valve's lifespan and reliability, which are key metrics in assessing performance over time.
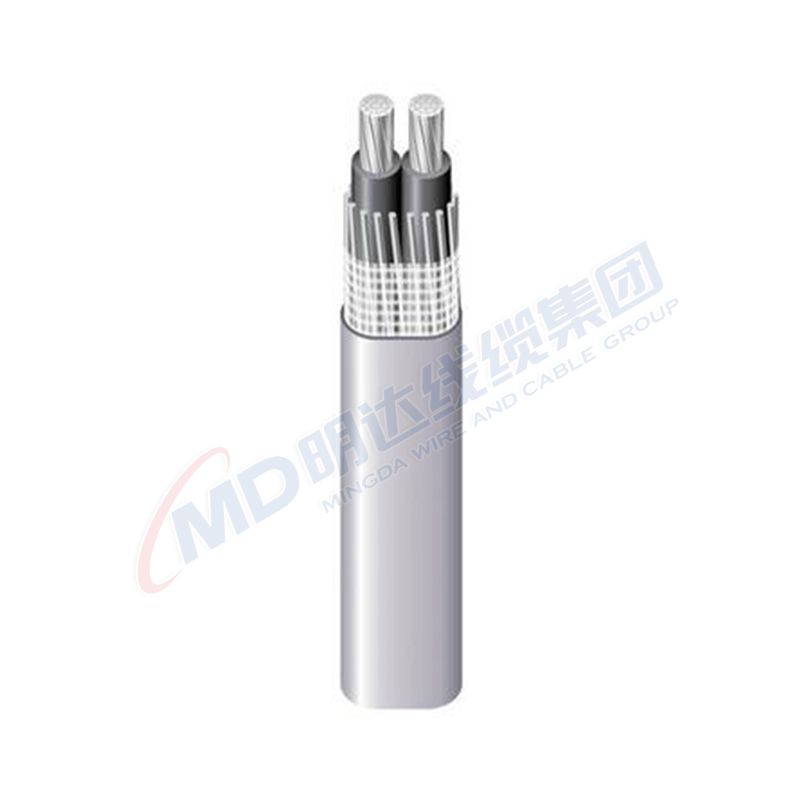
The internal components, including the seats and seals, also play a critical role in the valve's durability and effectiveness. Seats made from PTFE (polytetrafluoroethylene) provide excellent chemical resistance and low friction, making them ideal for applications involving aggressive media. However, in high-temperature or high-pressure applications, reinforced or alternative materials may be necessary to maintain integrity and performance without degradation.
From an engineering perspective, the sizing and configuration of the ball valve must not be overlooked. Proper sizing ensures the valve will handle the required pressure and flow rate, avoiding scenarios where the valve is either under or over-specified. Misjudging these parameters can lead to critical operational failures or inefficiencies. This underscores the importance of engaging with a knowledgeable supplier or engineer who comprehends the specific needs and constraints of your application.
ball valve
Moreover, a sterling example of trustworthy products in the industry is those certified with international standards such as ISO 9001 and API specifications. These certifications indicate that the ball valve has undergone rigorous testing and quality control, ensuring reliability and superior performance. This level of authority in certification elevates the dependability of the valve in critical operations, thereby instilling confidence among users.
Installation practices and maintenance also define the long-term success of ball valves in industrial settings.
A common pitfall involves improper installation, which can lead to leakage or mechanical failure. Training personnel adequately in installation protocols and regular maintenance inspections can mitigate such risks. Regular check-ups allow for the identification of wear and tear, ensuring prompt replacements of damaged components to prolong the lifespan of the valve.
In the ever-evolving landscape of industrial solutions, innovation remains at the forefront. Advances in ball valve technology now include features such as cavity fillers and fire-safe designs. Cavity fillers eliminate the possibility of space between the ball and the body, reducing the chance of residue accumulation, which can lead to contamination or operational disruption. Fire-safe designs, on the other hand, ensure that the valve can sustain operations or safely shut-off in case of a fire, providing an additional layer of safety in volatile environments.
A discerning look at the ecological impact also falls within responsible expertise and authority. Many industries now turn to environmentally friendly options, demanding valves produced with sustainable processes and having minimal environmental footprints. This consideration not only aligns with corporate social responsibility but also meets the increasing regulatory demands imposed on many industrial sectors.
Ultimately, investing in the right ball valve requires an informed balance of expertise, practical experience, and adherence to industry standards. Such investment pays dividends in minimized downtime, enhanced safety, and uninterrupted performance. By prioritizing authoritative choices and trustworthy practices, businesses and consumers alike can ensure efficient operations in even the most demanding environments.