DIN metal seat gate valves stand as a cornerstone in industrial applications, particularly where durability and reliability are paramount. These valves, adhering to DIN standards, ensure precision in design and functionality, making them indispensable in a plethora of industries, including petrochemical, oil and gas, and water treatment sectors.
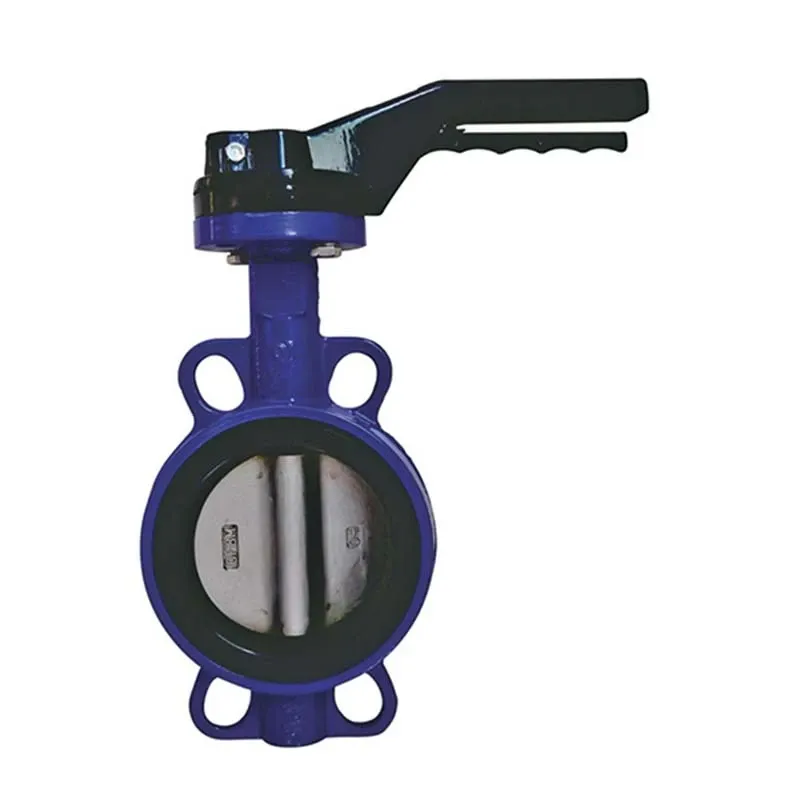
Crafted with robust materials, metal seat gate valves are prized for their ability to withstand high temperature and pressure conditions, providing longevity and minimizing the need for maintenance. What sets DIN metal seated gate valves apart is their adherence to stringent German Institute for Standardization (DIN) metrics, which assures users of a global benchmark in quality and interoperability.
In practice, these valves operate by lifting a gate out of the path of the fluid, allowing for minimal fluid resistance when the gate is fully opened. The metal seat ensures enhanced durability, making them suitable for operations that involve abrasive fluids or environments that pose a risk of erosion. When closed, the metal seats provide a tight seal, essential for ensuring safety and preventing leaks which could lead to costly downtime or accidents.
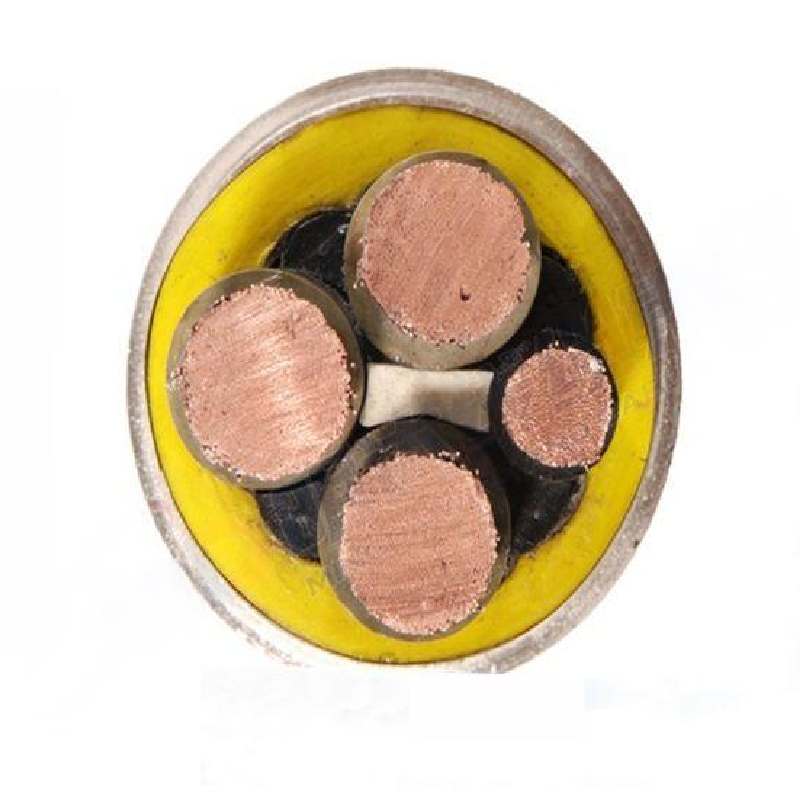
One of the core benefits of these valves is their adaptability to automation, which is increasingly becoming a necessity in modern industrial applications. By integrating actuators, operators can achieve enhanced precision and control, facilitating remote operation which is crucial for industries looking to optimize efficiency and safety.
Furthermore, for industries concerned about environmental compliance and risk mitigation, DIN metal seat gate valves are exemplary due to their robust sealing capabilities which prevent leaks— a common cause of environmental incidents. This sealing integrity is crucial in hazardous industries where the escape of potentially dangerous fluids could have significant implications not just for safety, but for a company’s reputation and compliance with regulations.
din metal seat gate valve
In terms of expert support and service life, DIN metal seat gate valves often come with comprehensive technical documentation that guide installation, operation, and maintenance. This documentation is crucial for engineers who require clear guidance to ensure optimal valve performance throughout its lifecycle. Specialists in valve technology advocate regular inspections and maintenance checks to extend the service life of these valves, asserting that predictive maintenance can prevent unexpected failures and prolong operational uptime.
The authority of DIN standards is not merely in their technical specifications but in their pervasive acceptability worldwide which simplifies international trade and application in global projects. The DIN standard acts as a quality guarantee, ensuring these valves meet high standards of precision and performance. Industries adopting DIN metal seat gate valves can trust in a product that not only meets but often exceeds industry expectations regarding reliability and efficiency.
Establishing trust in these products also comes from their ability to interface seamlessly with existing systems, whether it involves retrofitting in older installations or being implemented in cutting-edge projects. These valves are designed to harmonize with industrial pipelines, often available in various sizes and pressure ratings, thereby catering to a broad spectrum of industrial requirements.
Lastly,
it is essential to highlight the importance of selecting the right manufacturer when considering the purchase of DIN metal seat gate valves. A reputable manufacturer offers not only a superior product but also a wealth of expertise, from materials science to advanced engineering, which factors significantly into the performance of the valve. Manufacturers with a solid track record in producing DIN-compliant valves bring assurance through certifications and third-party verifications, further enhancing their credibility in the industry.
In summation, choosing DIN metal seat gate valves is a decision towards durability, reliability, and adherence to internationally recognized standards. Their robustness, coupled with the precision of DIN compliance, positions them as a worthy investment for industries where valve failure is not an option. With proper maintenance and the backing of an expert manufacturer, these valves ensure operational efficiency and safety, solidifying their role as an indispensable component in industrial operations.