Industrial globe valves are an essential component in the effective management and control of flow in various industrial applications. These valves, characterized by their spherical shape, allow for precise flow regulation, making them ideal for scenarios where accuracy and durability are paramount. With my extensive experience in the field of industrial valve solutions, I can assure that understanding the interplay of design, material selection, and application greatly influences the effectiveness and longevity of globe valves.
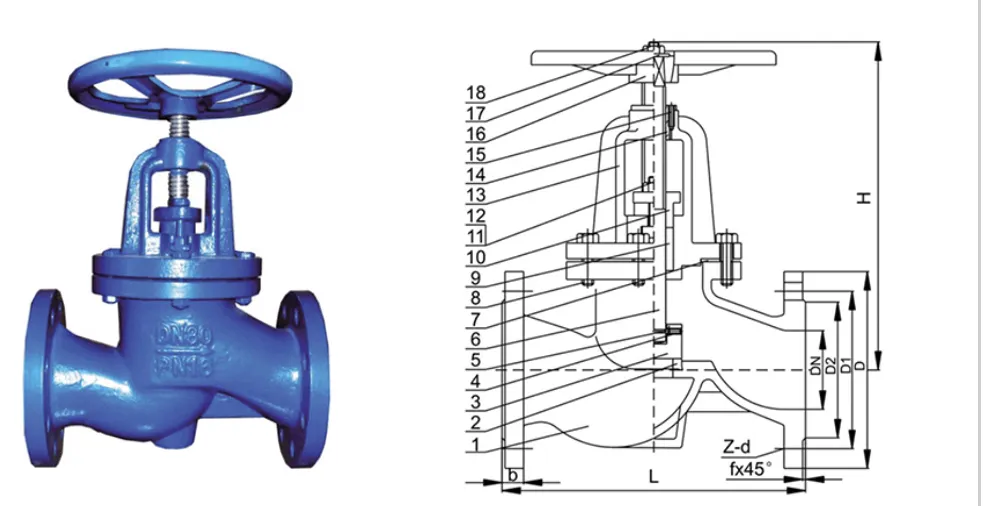
The distinctive construction of industrial globe valves incorporates a movable disk element and a stationary ring seat within a generally spherical body, a design that facilitates significant throttling capabilities. This configuration not only allows for finer control over fluid flow but also minimizes leakage risk, a critical factor in industries such as oil and gas, petrochemical, and water treatment. Expertise in selecting the correct design type, such as Z-type, Y-type, or angle-type globe valves, can greatly enhance performance tailored to specific industry needs.
Recognizing the authoritative standards that govern the manufacture and application of industrial globe valves is crucial for ensuring their reliability and safety. Adherence to norms set by organizations such as the American National Standards Institute (ANSI) and the American Petroleum Institute (API) ensures that these valves meet stringent quality and performance criteria. These standards dictate aspects ranging from pressure ratings to material compatibility, emphasizing the importance of selecting valves that conform to these benchmarks for optimal safety and efficacy.
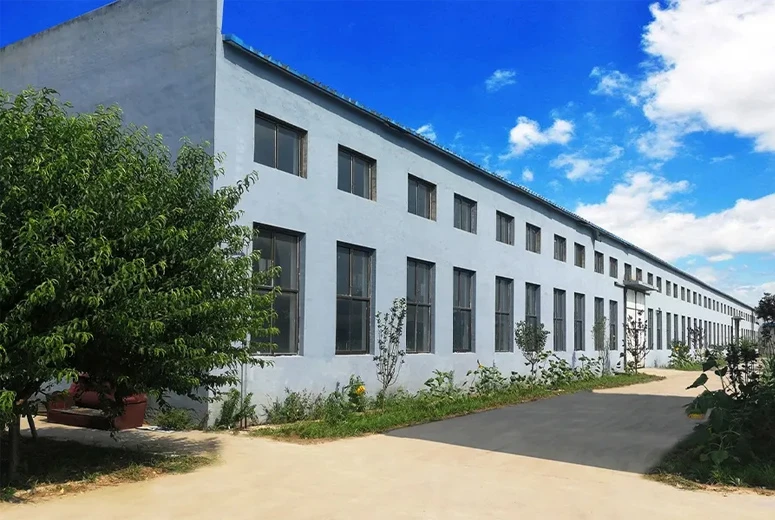
Trustworthiness in industrial globe valve applications predominantly stems from the materials used in their construction. Typically, these valves are fabricated from robust materials such as stainless steel, bronze, or cast iron, which provide excellent resistance to corrosive substances and high temperatures. Selecting a valve made from the appropriate material not only extends its operational life but also prevents costly downtime due to premature failure. In high-stakes environments, such as chemical processing plants, ensuring material compatibility with the working fluid is vital to maintain process integrity and avert potential hazards.
industrial globe valve
The adaptability of industrial globe valves to a multitude of processes signifies their viability as a primary control solution in various situations. Their capacity to function effectively in high-pressure environments as well as accommodate a broad range of temperatures and flow rates makes them invaluable in ensuring process efficiency and safety. As such, selecting the right valve for your system is not just about meeting immediate operational requirements but also about future-proofing against evolving industrial challenges and innovations.
One cannot overlook the importance of regular maintenance and inspection in maintaining the performance and safety of industrial globe valves. Regular examination for wear and tear, ensuring the integrity of seals and seats, and adhering to maintenance schedules can prevent failures and extend the life of these integral components. Leveraging expert services for maintenance can help detect potential issues before they escalate, thus preserving both asset longevity and operational efficiency.
In conclusion, when choosing an industrial globe valve, a comprehensive understanding of its design principles, adherence to authoritative standards, material selection, and maintenance requirements is essential. These factors collectively ensure that the valve will perform optimally, offering precise flow control while minimizing risks. For industry leaders aiming to enhance their operational systems, investing in high-quality, reliable globe valves offers an invaluable advantage, combining exceptional performance with assured safety.