In the world of industrial components, rubber check valves have emerged as a critical solution for managing fluid flow systems. These devices, known for their simple yet efficient design, are pivotal in ensuring unidirectional flow, preventing backflow, and minimizing potential damage to fluid transfer systems. This article delves into why these valves are indispensable in various industries, highlighting their real-world applications, professional insights, authoritative perspectives, and reasons for trust.
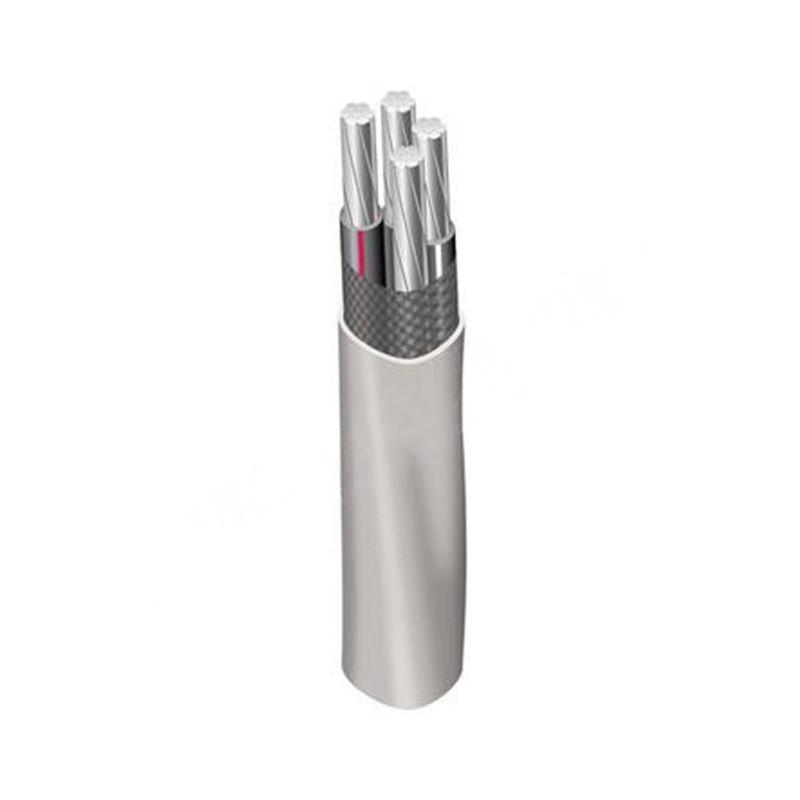
Rubber check valves consist of a straightforward mechanism a rubber diaphragm or flap that opens to allow fluid to pass through and closes when the flow reverses, thus preventing backflow. This simplistic design is not only effective but also economical, making these valves a preferred choice across various sectors. Their operation requires no external force, relying instead on the pressure of the fluid itself to function—a factor that significantly reduces maintenance costs and potential mechanical failures.
One of the most significant applications of rubber check valves is in wastewater management systems. Professionals in this field appreciate the reliability these valves offer, as they operate efficiently even under adverse conditions, such as high levels of suspended solids or variable flow rates. This capability is critical in preventing sewer backflows, which can cause extensive damage and pose significant health risks. By installing rubber check valves, municipalities and industries can ensure sanitary systems run smoothly and sustainably.

Another area where rubber check valves shine is in the pharmaceutical industry, where maintaining a sterile and contamination-free environment is paramount. These valves are often used in the production lines of liquid medicines, where their non-reactive rubber components prevent chemical reactions that could compromise the product's integrity. Additionally, their ability to function without additional power sources makes them ideal for maintaining uninterrupted operations, even during power fluctuations.
rubber check valve
From an authoritative viewpoint, various standards and certifications back the use of rubber check valves, such as those from the American Water Works Association (AWWA) and the American Society for Testing and Materials (ASTM). These certifications ensure that the valves meet rigorous safety and quality metrics, reinforcing trust among industry professionals and end-users. Systematic quality checks during the manufacturing process further enhance their credibility, ensuring each unit's performance and safety.
The expertise behind the engineering of rubber check valves cannot be overstated. Manufacturers incorporate advanced techniques to ensure durability and adaptability to various fluid types, from gases to viscous liquids. The selection of rubber material is crucial, with options like EPDM, Nitrile, and Viton being selected based on the application compatibility, temperature, and chemical exposure anticipated during their use. This material selection process ensures longevity and reliability, even in the most demanding environments.
From a trustworthiness perspective, investing in rubber check valves is a sound decision due to their minimal maintenance requirements and long service life.
This trust is not only built on the product's performance but also on the expert guidance provided by manufacturers. Many companies offer detailed installation and maintenance guides, along with technical support, ensuring that their clients can maximize the benefits of using rubber check valves without significant operational disruptions.
In conclusion, the importance of rubber check valves in industrial fluid systems cannot be overstated. Their efficient design, supported by expert engineering and backed by authoritative certifications, positions them as a trustworthy component in safeguarding against backflow and maintaining efficient operations across various industries. As industries continue to evolve and demand more reliable solutions, rubber check valves stand out as a resilient and indispensable part of modern fluid management systems.