Industrial ball valves are an integral component in the infrastructure of numerous industries worldwide, playing a critical role in fluid management systems. Precision-engineered and designed for durability, these valves are essential for regulating the flow of liquids and gases, ensuring operational efficiency and safety across diverse applications.
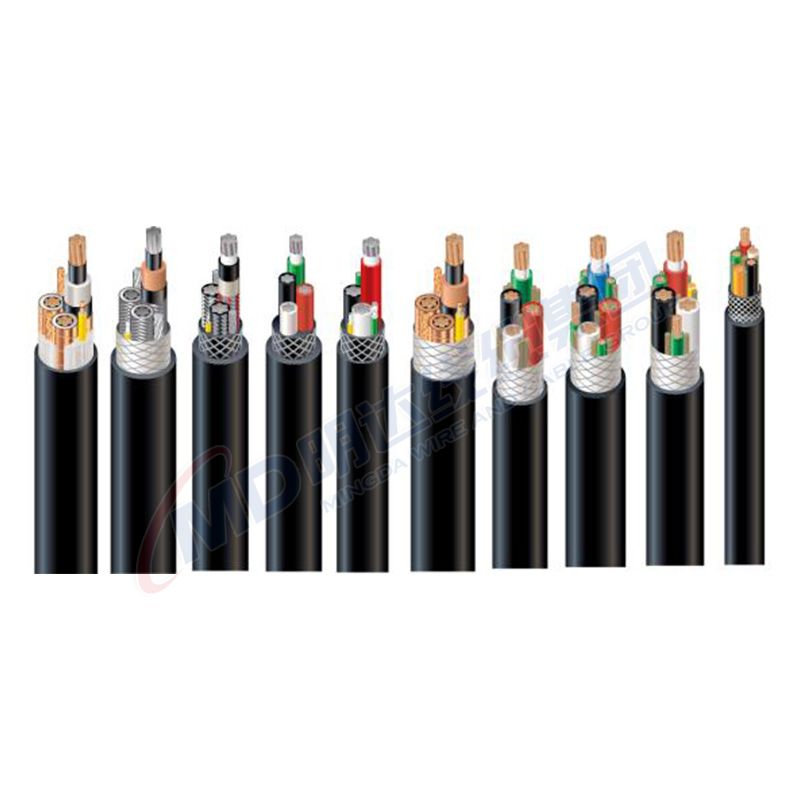
Understanding the technicalities and specifications of industrial ball valves is paramount for engineers, procurement professionals, and facilities managers who aim to enhance the performance and reliability of their operational systems. These valves are characterized by their simple, robust design, which includes a spherical disc to control flow. The ball, with a hole through the middle, sits in a seat within the valve body, allowing for efficient sealing and long-lasting performance. Their design enables quick and easy actuation, which is why they are preferred in situations requiring rapid operation.
Expertise in various types of industrial ball valves can significantly impact decision-making processes. Common variants include two-way and three-way valves, offering flexibility in directing and controlling flow paths in piping systems. Furthermore, understanding the material composition—ranging from stainless steel to brass and PVC—can greatly influence the valve’s performance in different environments. Each material has its strengths and ideal use cases, such as stainless steel for high-temperature and high-pressure applications or PVC for corrosive and chemical-rich environments.
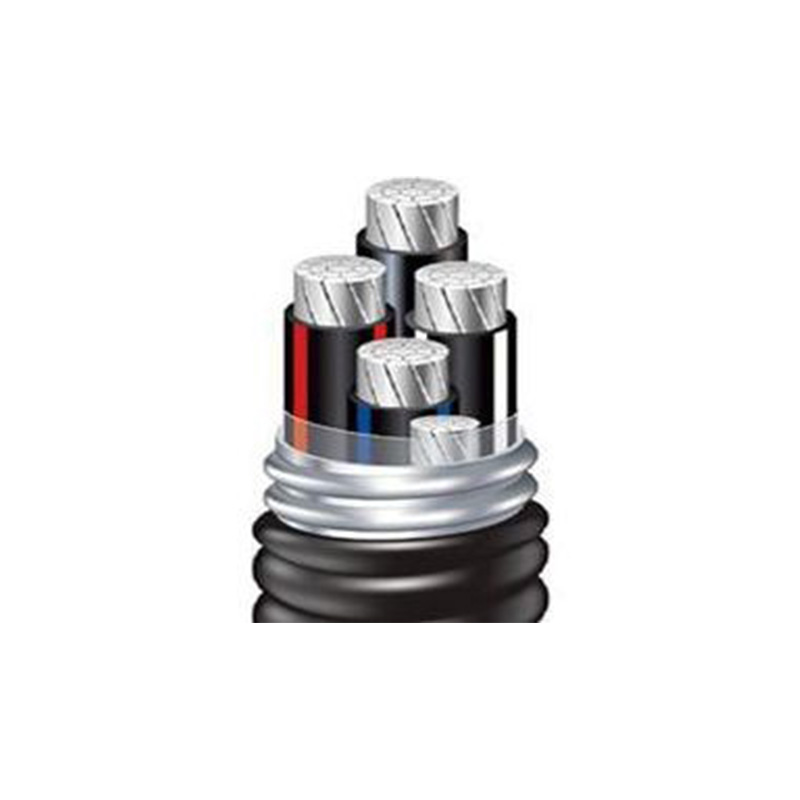
The authoritativeness of a supplier is a vital consideration when selecting industrial ball valves. Reputable manufacturers adhere to stringent quality standards and provide comprehensive documentation, including pressure ratings, temperature ranges, and certifications from industry bodies like ASME or API. This assurance of quality is critical for industries such as petrochemical, oil and gas, and water treatment, where valve failure can lead to catastrophic consequences.
For facilities managers and engineers, trustworthiness in performance is achieved through regular maintenance and inspection of industrial ball valves. While these components are designed for longevity, factors such as fluid composition and operating pressures can affect their lifespan. Employing predictive maintenance strategies, such as condition monitoring and periodic testing, can prevent unexpected downtimes and extend the service life of the valves.
industrial ball valve
The implementation of industrial ball valves is not merely about installation; it involves comprehensive planning and assessment to ensure compatibility with existing systems and processes. Engineers must consider flow characteristics, such as Cv values, to ensure the valve delivers the desired flow rate and energy efficiency. Integration with control systems is another critical aspect, as automation plays an increasingly significant role in modern industrial operations.
Case studies and real-world applications provide valuable insights into the efficacy of industrial ball valves. For instance, in the energy sector, ball valves are often employed in pipeline systems to manage the flow of crude oil, natural gas, and other energy resources. The ability of these valves to operate in harsh environments with minimal maintenance leads to significant cost savings and operational improvements.
In water treatment facilities, the precision afforded by industrial ball valves facilitates the fine-tuning required for water filtration and purification processes. Their ability to provide a perfect seal reduces the risk of contaminant ingress, maintaining system integrity and ensuring regulatory compliance.
Ultimately, the choice and deployment of industrial ball valves have far-reaching implications for the operational success and safety of industrial infrastructures. By leveraging the comprehensive experience, expertise, authoritativeness, and trustworthiness that these components offer, industries can achieve not only enhanced operational efficiency but also safeguard their processes against potential disruptions. This meticulous approach to valve selection and maintenance epitomizes best practices in industrial fluid management and underscores the critical role that industrial ball valves play in supporting the global industrial landscape.