Lugged butterfly valves have emerged as indispensable components in the realm of industrial fluid control systems. Not just notable for their sleek design and efficient functionality, lugged butterfly valves are celebrated for their versatility and reliability in various applications. This article delves into their unique features, applications, and the reasons they are favored in industries requiring precise fluid management.

At the core of the lugged butterfly valve's design is its unique mechanism which includes a circular disc mounted on a rotating shaft. When the valve is closed, the disc seats tightly against a ring within the valve body, effectively blocking the flow. Its lugged design enhances the valve's installation flexibility, allowing it to connect seamlessly with both upstream and downstream flanges, or functioning independently at the end of a piping system. This capability makes it particularly beneficial for systems needing section isolation or maintenance without full pipeline drainage.
One of the primary advantages of lugged butterfly valves is their installation and maintenance simplicity. Unlike other valve types that may require intricate assembly and significant upkeep, the lugged butterfly valve's structure lends itself to quick and straightforward installation. The lugs, resembling protruding ears, contain threaded inserts that permit flange alignment without additional gasket materials. This feature significantly reduces labor costs and installation time—critical considerations in large-scale industrial operations.
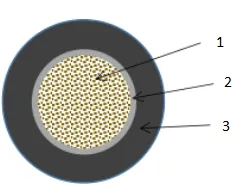
From food processing and chemical industries to water treatment facilities and HVAC systems, the applications of lugged butterfly valves are extensive. They are designed to handle a broad spectrum of substances, including corrosive chemicals, gases, and slurries, which makes them an ideal choice for industries dealing with hazardous materials. Their capacity to maintain a leak-free seal even in high-pressure environments underscores their reliability and robust performance, cementing their status as trusted components in demanding settings.
lugged butterfly valve
The expert consensus supports the selection of lugged butterfly valves not just for their operational efficiency but also for their long-term durability. Constructed from durable materials such as stainless steel, ductile iron, and PVC, these valves endure the harshest operational conditions, offering extended life spans which are essential for minimizing downtime in critical systems. Furthermore, their compact build contributes to cost-efficiency by requiring less space and support infrastructure compared to bulkier valve types.
In terms of innovation, manufacturers continue to enhance lugged butterfly valve designs with smart technology integrations. Modern valves are increasingly capable of remote operation and monitoring, incorporating sensors and IoT technology to provide real-time data on system performance. This advancement adds a layer of predictive maintenance, allowing operators to anticipate and rectify potential issues before they escalate, thereby improving system reliability and operational safety.
Trustworthiness and authority in valve selection are crucial particularly when safety and environmental standards are at stake. Leading valve manufacturers adhere to stringent quality control measures and international standards, assuring end-users of product integrity. By choosing products from reputable suppliers with proven track records, businesses align their operational goals with safety and efficiency standards, thereby securing not only reliability in performance but also regulatory compliance.
As technology and industry standards continue to evolve, lugged butterfly valves remain fundamentally unchanged in their purpose yet consistently refined in their application. This unique balance of stability and innovation is why they continue to hold an authoritative position in the fluid control domain. Their role is undeniably vital, and their contribution to both everyday operations and more complex systems remains substantial, making them an asset worthy of serious consideration in any fluid management strategy.