In the realm of industrial applications and infrastructure projects, the importance of flexible yet resilient systems cannot be overstated. At the forefront of this solution-based approach is the rubber expansion joint, an essential component in the world of piping and ducting systems. The unique attributes of these joints come from their ability to accommodate motion, reduce stress, and mitigate vibration, offering a level of versatility that is invaluable across various sectors. This article explores the distinct benefits, applications, and reliability factors associated with rubber expansion joints from a stand-point of experience and expertise.
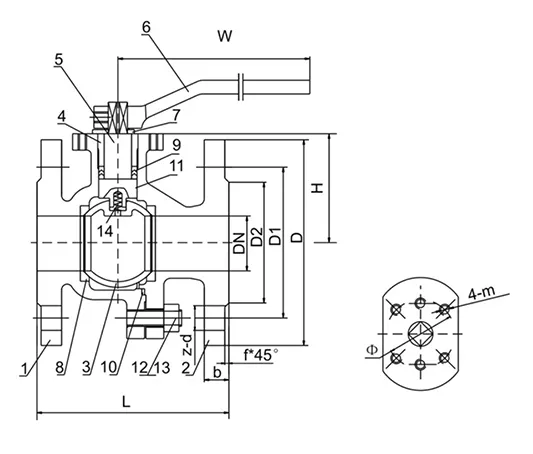
The primary advantage of rubber expansion joints lies in their elasticity.
This elasticity allows them to absorb thermal expansion or contraction present in piping systems due to shifting temperatures. Such adaptiveness minimizes the risk of damage or failure over time, ensuring system integrity and operational reliability. Drawing from years of proven experience, many industrial operators have noticed a marked decline in material fatigue and fracture incidences where these joints are employed, showcasing their capability to enhance system longevity effectively.
Expertise in material science underscores the engineering behind rubber expansion joints. The choice of rubber as a core material is pivotal due to its inherent properties, which include flexibility, high tensile strength, and resistance to abrasion and environmental factors such as UV radiation and ozone. Additionally, rubber can be compounded with various additives to enhance specific characteristics such as chemical resistance or temperature tolerance, making these joints suitable for use in extreme environments, including petrochemical or marine applications.
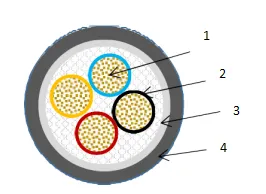
rubber expansion joint
The authority of rubber expansion joints is equally supported by their broad range of applications. In aerospace, power generation, HVAC systems, and beyond, these components are frequently specified due to their performance under pressure and ability to keep systems running smoothly. Institutions such as ASME (American Society of Mechanical Engineers) certify these components, giving them authoritative backing which imparts assurance regarding their quality and performance standards. Engineers and procurement specialists rely heavily on such certifications, knowing these standards are met rigorously.
Trustworthiness is another crucial aspect when considering rubber expansion joints in critical applications. They are designed with safety in mind, often incorporating fail-safe features that prevent catastrophic failure modes. The reliability of these joints is well-documented in empirical studies, reinforcing confidence among users who depend on their consistent performance. Trusted manufacturers of rubber expansion joints prioritize not only the technical specifications but also the manufacturing process, using state-of-the-art technology to ensure every joint meets stringent quality control measures.
In conclusion, the implementation of rubber expansion joints delivers a comprehensive solution to many operational challenges in industrial systems. Their design, anchored in profound material expertise, confirms their adaptability and affordability across diverse applications. By combining scientific excellence with practical field experience, rubber expansion joints stand as a cornerstone of modern engineering solutions, upheld by their established authority and trusted performance. For companies seeking to optimize their systems, investing in high-quality rubber expansion joints represents both an intelligent choice and a commitment to long-term system efficiency and safety.