In the ever-evolving field of fluid control systems, the wafer type butterfly valve stands out as a pivotal component due to its compact design and efficiency in handling various media. The wafer type butterfly valve, characterized by its simplicity and ease of use, finds application across industries such as water treatment, pharmaceutical, food and beverage, and oil and gas. Its adaptable nature allows it to flourish in both high-pressure and low-pressure systems, making it an indispensable asset in any engineer's toolkit. Here, we delve into the dimensions of the wafer type butterfly valve, an aspect critical to its integration and performance in your pipeline systems.
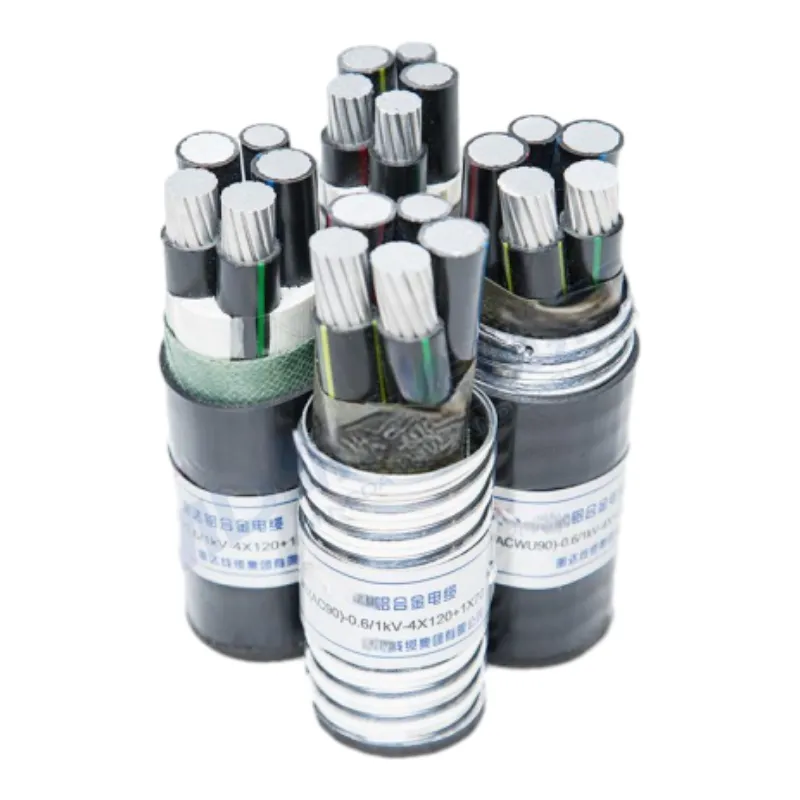
When considering a wafer type butterfly valve for your system, dimensional accuracy is paramount. The dimensions dictate the valve's fitment and influence both the fluid dynamics within the system and the ease of maintenance. One of the primary advantages of the wafer design is its space-saving nature. Unlike lug-style valves, wafer type butterfly valves are designed to sit between two flanges, offering a streamlined solution that minimizes space and material usage.
The key dimensions to focus on include the nominal pipe size (NPS), the outer diameter, face-to-face dimensions, and the bolt circle diameter. These determine the compatibility with the existing piping infrastructure, ensuring seamless integration. For instance, a valve intended for an NPS of 8 will have different dimensions compared to one designed for a 12-inch pipe. Standardized dimensions help maintain consistency across diverse installations, but custom dimensions are occasionally necessary for more complex systems.
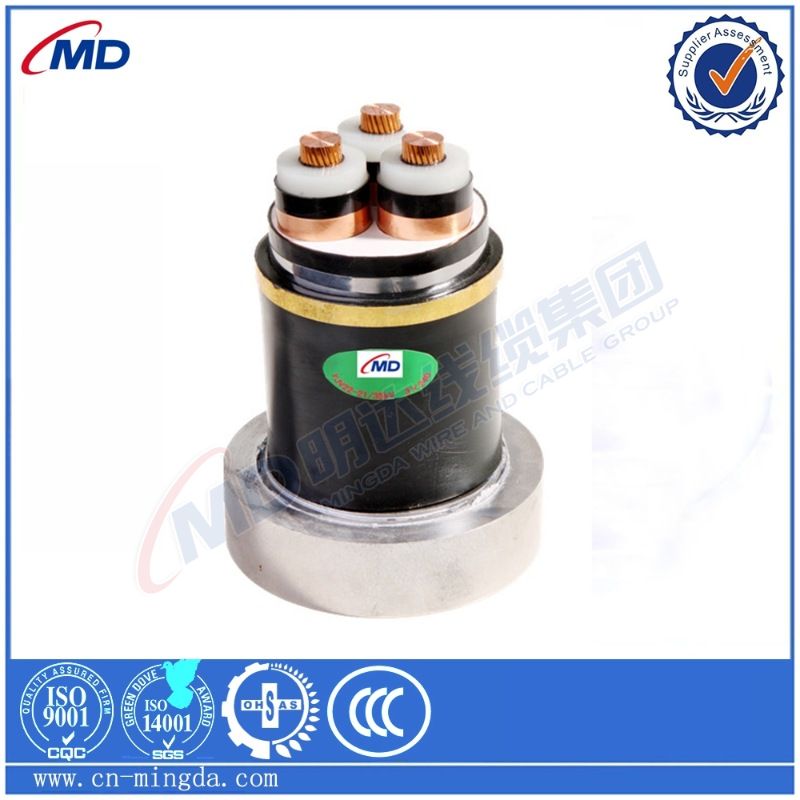
Accuracy in these dimensions also aids in achieving optimal flow control. The wafer design, though straightforward, must ensure that it doesn’t disrupt the flow excessively, which could lead to cavitation or other efficiency losses. Therefore, precise measurements reduce the risk of such issues, safeguarding the system's integrity and performance.
In terms of real-world use, experience highlights that every application has unique demands. For example, in applications where corrosion resistance is crucial, the valve's disc and liner material may alter its dimensions slightly, depending on the chosen materials. Engineers must also consider the actuation method—manual, electric, or pneumatic—as this affects the overall footprint and operational efficiency of the valve.
wafer type butterfly valve dimension
From an expertise perspective, mastering the dimensions of the wafer type butterfly valve ensures optimal configuration and performance of the fluid system. Engineers and procurement specialists must remain vigilant of the compatibility between valve sizes and pipework to mitigate potential mismatches that can lead to increased downtime or system failure. Manufacturers often provide detailed dimensional data sheets; however, consultation with an expert may be warranted for bespoke applications.
Furthermore, the authoritativeness in the selection of a wafer type butterfly valve can be fortified by choosing reputable manufacturers known for stringent quality control processes and global certification adherence. Products should ideally comply with international standards such as the API609, which outlines the design and testing specifications for butterfly valves.
Lastly, trustworthiness is cultivated through maintaining transparency in the communication of dimensional specifications and operational limits of the valve. Suppliers who offer not only a reliable product but also post-purchase training and support tend to foster stronger trust with their client base.
In conclusion, the dimensions of a wafer type butterfly valve are crucial to its effective application and integration into your system. A comprehensive understanding of these dimensions, aligned with industry best practices and standards, will inform wise procurement choices and enhance the operational reliability of your fluid control systems. Whether part of a new installation or a retrofit, selecting the correctly sized valve ensures a synergy between components, ultimately leading to a streamlined process and cost savings over the valve's life cycle.