Industrial valves are integral components in various manufacturing processes, ensuring the control of liquids and gases within pipelines. Drawing from years of experience in designing and implementing valve technologies, it's crucial to understand their roles, functionalities, and innovations that are shaping the industry today.
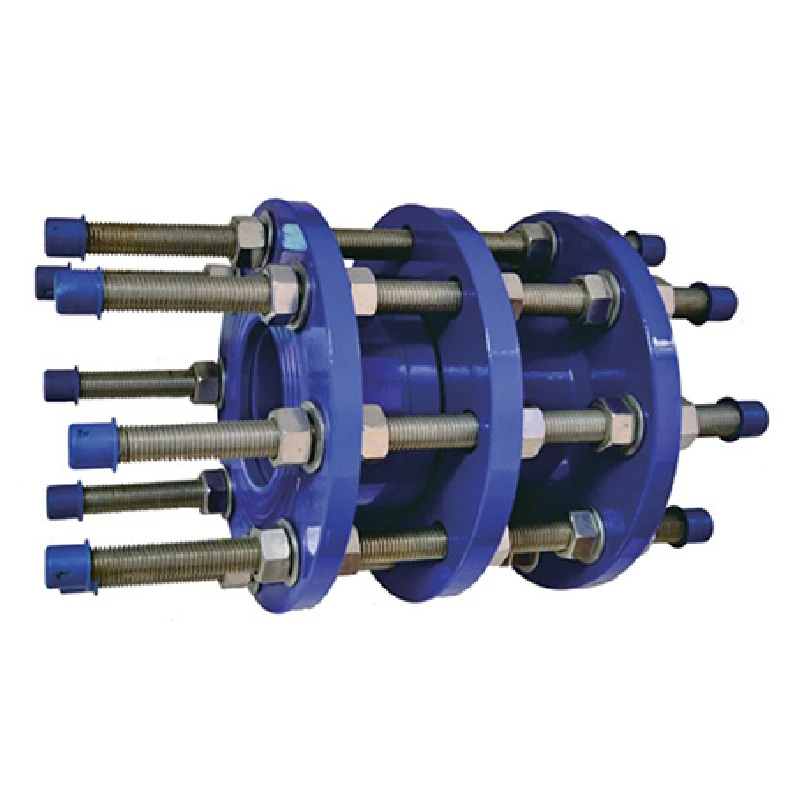
Valves, at their core, serve the essential function of controlling flow rates, regulating pressure, directing flow, and ensuring safety within a system. These components come in various forms, including gate valves, globe valves, ball valves, butterfly valves, and check valves, each uniquely suited to specific tasks. The choice of valve affects not only the efficiency but also the safety and overall cost-effectiveness of industrial operations.
Gate valves, renowned for their ability to control flow with minimal pressure loss, are ideal for applications needing a full flow area. This type of valve is often employed in scenarios where fluids need to stop or start than throttle. On the other hand, globe valves, with their ability to precisely control flow rate, are preferred in industries where flow regulation is paramount, such as chemical processing.
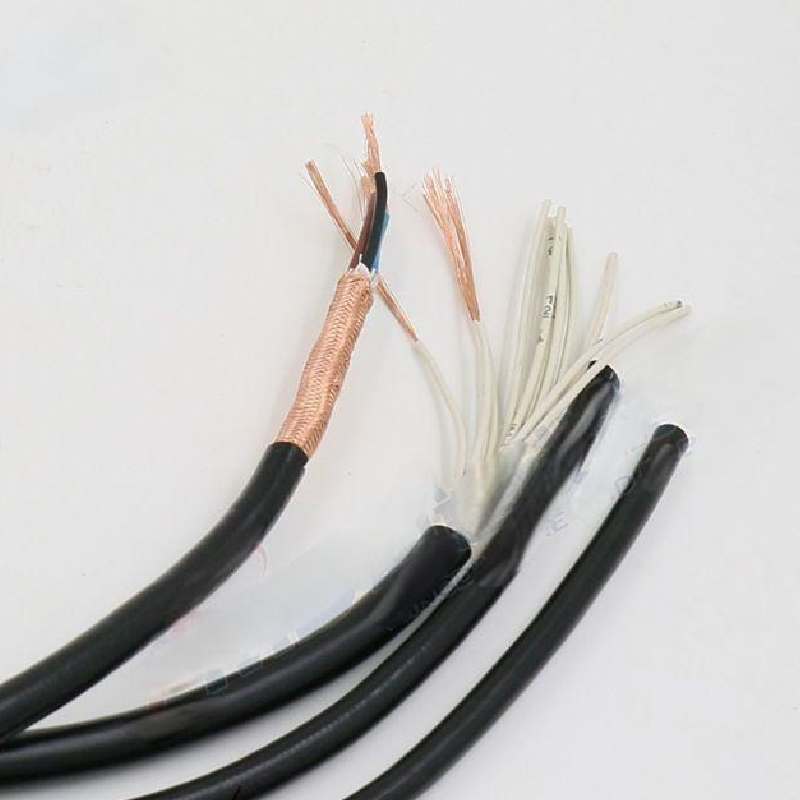
In recent years, technological advancements have spurred the evolution of industrial valves, enhancing their capabilities and applications. Smart valves, for instance, are a breakthrough in the industry, integrating sensors for real-time monitoring and automated controls to optimize performance and maintenance schedules. These intelligent systems significantly reduce downtime and operational costs by predicting failures before they occur.
Moreover, material innovations have extended the lifespan and resilience of industrial valves. High-performance materials such as stainless steel, Hastelloy, and titanium are increasingly used for their durability and corrosion resistance, especially in extreme environments. This ensures reliability under high pressure and temperature conditions, a testament to expertise in materials engineering.
industrial valve
Selecting the right valve demands a combination of industry knowledge and authoritative understanding of the operational environment. Valves must withstand the media's chemical composition, as inappropriate material selection can lead to rapid deterioration and failure. Therefore, expertise in both fluid dynamics and material science is indispensable for manufacturers aiming to produce valves with high trustworthiness.
Sourcing valves from reputable manufacturers guarantees not only quality but also compliance with industry standards. A manufacturer's adherence to international standards and certifications, such as API, ISO, and ANSI, further establishes their authority and capability in producing reliable valve solutions. Thus, building partnerships with seasoned manufacturers is critical for industrial entities seeking to optimize their operational infrastructure.
Furthermore, the integration of energy-efficient valve systems can contribute to sustainable industrial practices. With growing emphasis on reducing carbon footprints, valves designed to minimize energy loss and enhance operational efficiency are becoming increasingly important. This development aligns with global sustainability efforts, reflecting an industry's commitment to ecologically responsible practices.
In conclusion, the industrial valve industry is a vivid landscape of innovation and expertise, combining decades of technological advancements with deep-rooted industry knowledge. As valves play a pivotal role in the safe and efficient operation of countless industries, continuous developments in materials, technology, and standards underscore their importance. Valuable partnerships and an informed approach to valve selection and maintenance are paramount for any organization looking to enhance its operational reliability and sustainability. By leveraging these advancements, businesses not only bolster their operational effectiveness but also solidify their role in a rapidly evolving industrial world.