Industrial check valves play a crucial role in the seamless operation of countless industrial systems and are indispensable for ensuring the safety and efficiency of fluid management processes. These devices allow fluids to flow in one direction while preventing reverse flow, which can otherwise lead to system failures or operational inefficiencies. Known for their simple yet effective design, check valves are integral to preventing backflow in industries ranging from water treatment to petrochemical processing.
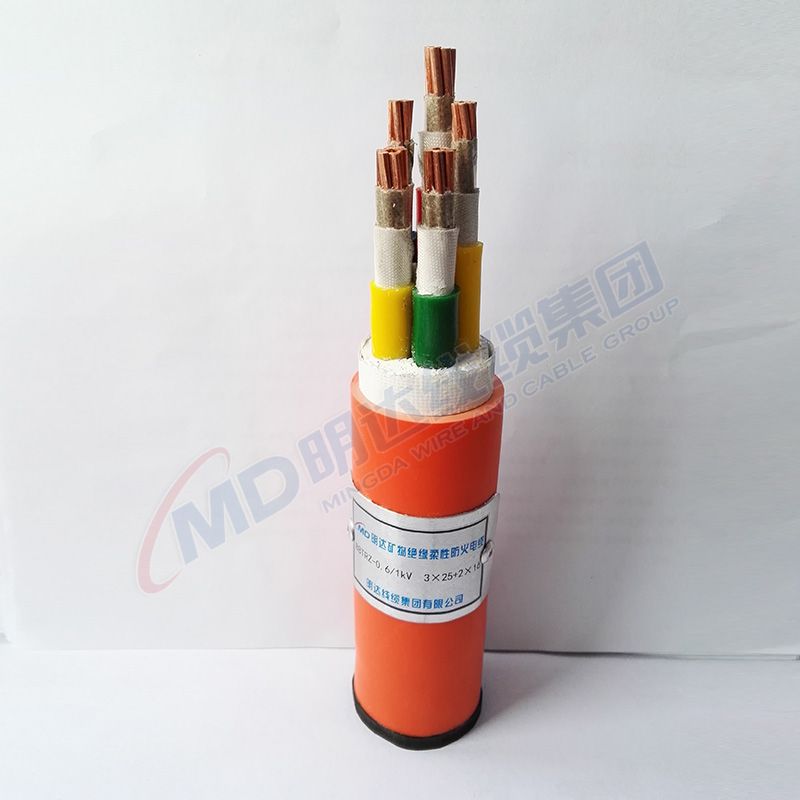
One of the standout features of industrial check valves is their robust construction. Designed to withstand high-pressure environments and corrosive materials, these valves are typically made from durable metals such as stainless steel, brass, and cast iron. This ensures they can operate effectively even under challenging conditions, providing long-lasting and dependable performance. For industries that deal with highly aggressive chemicals, special alloys or polymer coatings can be used to enhance the valve's resistance, further extending their lifespan and reliability.
The selection of an appropriate check valve model is paramount for optimizing performance and safety. Depending on the application, various types of check valves, such as swing, lift, and wafer check valves, can be utilized. Swing check valves, for example, are preferred in scenarios involving low-pressure drops and steady flow conditions due to their low-pressure loss characteristics. On the other hand, lift check valves, which operate in a piston-like motion, are better suited for systems with high-pressure environments. Wafer check valves, praised for their compact and lightweight design, are ideal for applications with space constraints.
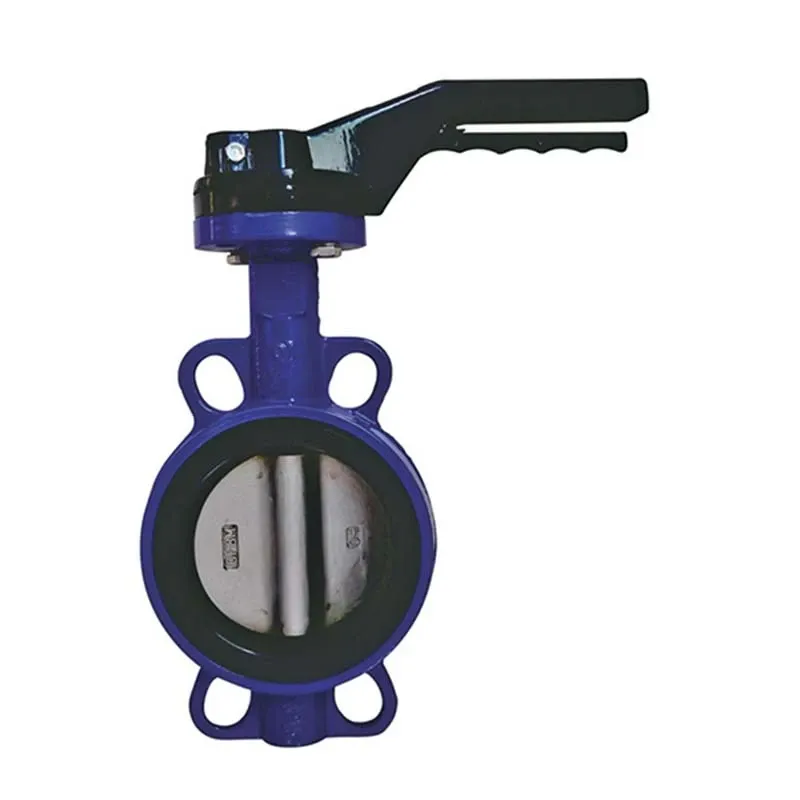
The expertise in choosing the correct check valve also extends to understanding the common issues that can arise during their operation. Water hammer, a phenomenon caused by sudden fluid stoppages, can severely damage a system if not properly mitigated. Using a slow-close check valve or a valve with a built-in dampening mechanism can effectively reduce the impact of water hammer. Regular maintenance checks, including inspections for wear and tear or any misalignment, are essential practices to ensure the system's integrity and prevent unexpected downtime.
industrial check valve
From an authoritative standpoint, the importance of industrial check valves is underscored by numerous standards and regulations that govern their design and application. Organizations such as the American Society of Mechanical Engineers (ASME) and the International Organization for Standardization (ISO) have established guidelines to ensure these components meet safety and performance benchmarks. Compliance with these standards not only secures operational safety but also enhances the credibility of manufacturers and suppliers in the competitive market landscape.
Trustworthiness in the selection and use of industrial check valves is rooted in transparency provided by manufacturers regarding product specifications and certifications. Procuring valves from reputable vendors who offer detailed product information, warranties, and support services can greatly reduce the risk of equipment failure. It is advisable to consult with industry professionals or hydraulic engineers who have a proven track record to aid in making informed purchasing decisions that align with specific industrial needs.
Finally, despite being relatively low-profile components, the role of check valves in ensuring uninterrupted system operation should not be underestimated. Their proper deployment and maintenance can lead to improvements in the operational efficiency and safety of major industrial sectors, including oil and gas, chemical processing, and water treatment. For engineers and plant managers aiming to optimize fluid control systems, investing in high-quality check valves is not simply a recommendation—it is a necessity.
In conclusion, industrial check valves are pivotal to achieving optimal flow management and pressure regulation in a wide array of industrial settings. Their design and material selection can significantly impact system performance and longevity, underscoring the need for expert knowledge in their application. By adhering to established standards and engaging with qualified professionals, industries can foster an environment where safety, efficiency, and innovation thrive.