Hydraulic control valves are crucial components in fluid power systems, offering precision and efficiency in managing flow and pressure. Through years of experience, professionals across industries have realized their indispensable role in enhancing operational effectiveness. This comprehensive examination delves into their functionalities, applications, and the benefits that set them apart from other control mechanisms.
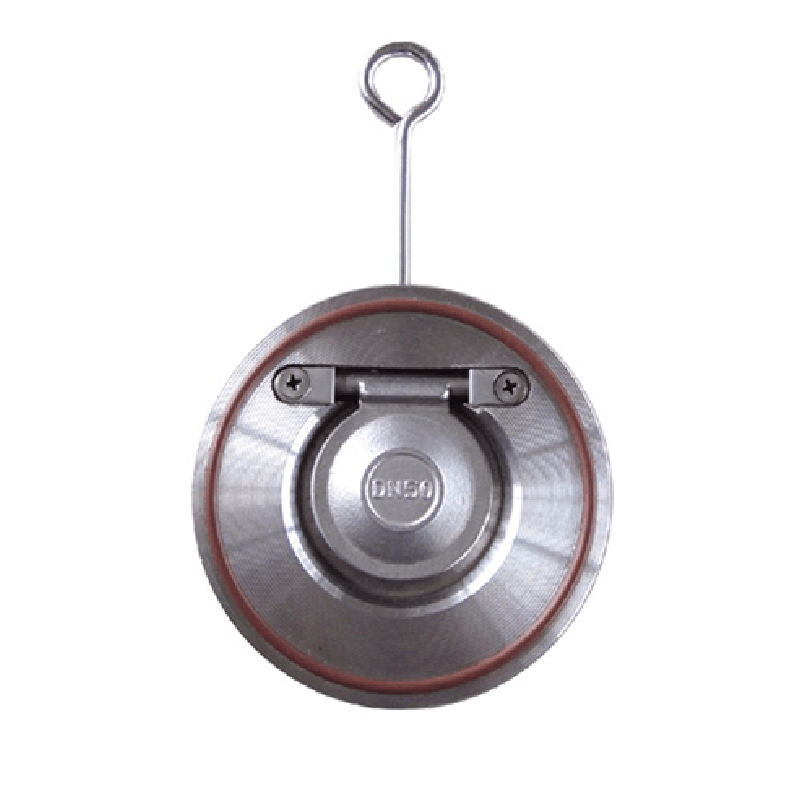
Hydraulic systems, by virtue of their design, require precise control over the flow and pressure of the fluid used to transmit power. Hydraulic control valves are meticulously engineered devices that regulate this flow, ensuring the system operates smoothly and efficiently. Drawing from years of expertise, these valves have been developed with precision tolerances and robust materials to withstand varying pressure and temperature conditions, thereby extending the lifespan of hydraulic systems.
One unique aspect of hydraulic control valves is their adaptability. They are designed to handle various types of hydraulic fluids, which enhances their versatility across different industrial applications. Whether managing the movements of large-scale machinery in construction or the fine control needed in aerospace technologies, these valves provide the necessary control to maintain operation standards. Industry experts rely on hydraulic control valves for their consistent performance under heavy-duty operations, attesting to their authority in fluid power systems.
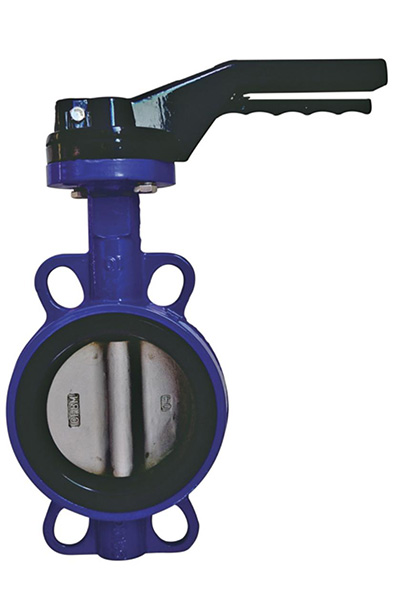
The technical superiority of hydraulic control valves lies in their multi-functional capabilities. They are capable of throttling, directional control, and pressure regulation, all essential for the seamless operation of hydraulic circuits. Valves such as directional control valves, pressure relief valves, and flow control valves each serve specialized functions but can be integrated into a single system to work in tandem, optimizing performance. Such integration requires a deep understanding of hydraulic principles and demonstrates the expertise manufacturers bring to designing these components.
hydraulic control valve
Trustworthiness in hydraulic control valves is non-negotiable as these components directly influence system safety and reliability. High-quality valves adhere to stringent industry standards, often meeting certifications from organizations like the International Organization for Standardization (ISO) and the American National Standards Institute (ANSI). These certifications indicate that the valves have undergone rigorous testing to verify their performance under defined conditions, ensuring operators can rely on them for critical applications.
In an evolving market where technological advancements bring forth new challenges, hydraulic control valves continue to adapt. Modern developments include the incorporation of smart technologies in valve systems, enhancing their functionality with features like remote monitoring and diagnostics. These advancements contribute to a predictive maintenance ethos, reducing the likelihood of system failure and downtime. Such innovations are borne from a combination of experience and deep-seated expertise in the field of hydraulics.
Ultimately, selecting the right hydraulic control valve requires an understanding of system requirements and a preference for trusted manufacturers. The complex nature of hydraulic systems means that expertise is essential not only in the selection but also in the installation and maintenance of hydraulic control valves. This ensures that systems operate efficiently and safely, providing maximum return on investment.
In summary, hydraulic control valves are an integral part of today's industrial landscape, offering unmatched precision and control. Their design, adaptability, and technological integrations highlight their evolution and enduring relevance. Through continuous innovation and adherence to quality standards, hydraulic control valves maintain their position as essential components in fluid power systems.