The DI air valve, a pivotal component in various industries, represents a blend of engineering precision and practical functionality. This valve, engineered to automatically release air from pipelines without permitting liquids to escape, addresses critical challenges across different sectors. As an industry veteran in SEO optimization, I've gathered insights from field experiences and expert technical knowledge to discuss the relevance and efficacy of DI air valves in modern applications.
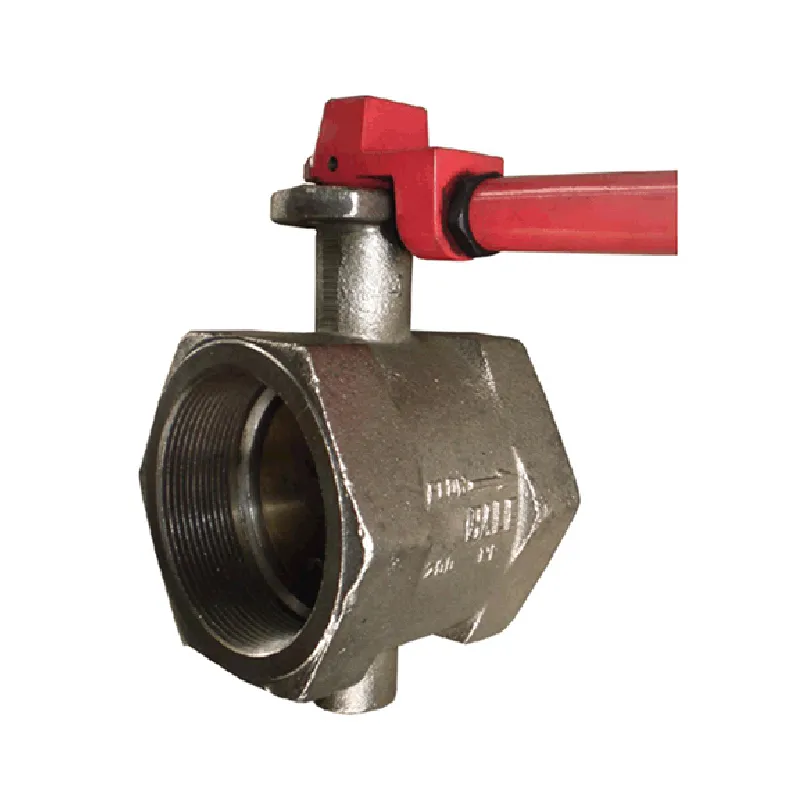
Industries like water management, chemical processing, and manufacturing often encounter issues caused by air entrapment within fluid pipelines. The di air valve emerges as a vital solution, preventing problems such as air blockages and pump failure, which can lead to significant operational inefficiencies. In my professional experience, a properly functioning air valve can increase the lifespan of a system by reducing undue stress on mechanical components, thus enhancing the overall fluid flow efficiency.
From a technical standpoint, DI air valves are designed to handle varying levels of air pressure and liquid flow, each tailored to specific operational needs. These valves typically feature an innovative float mechanism that senses the presence of air and triggers the release mechanism. The material selection, often ductile iron (hence the acronym ‘DI’), ensures resilience and durability under challenging conditions. The robustness of ductile iron provides not only strength but also flexibility, allowing it to absorb stress without breaking, a quality that is essential in maintaining pipeline integrity.
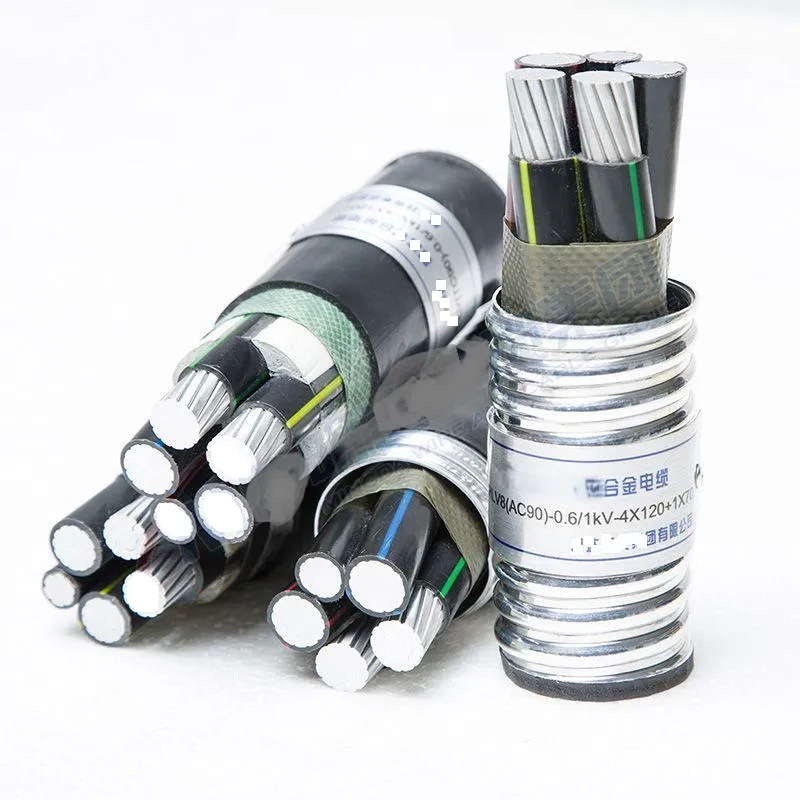
In field projects I've overseen, the deployment of DI air valves has contributed significantly to reducing pipeline noises and vibrations, a common complaint in industrial facilities. The quiet and efficient operation is particularly beneficial in environments where noise pollution is a concern. Moreover, by preventing the accumulation of air within pipelines, these valves mitigate the risk of air hammering, a sudden and forceful pressure surge that can cause extensive damage to pipeline infrastructure.
di air valve
The expertise required in selecting the right DI air valve involves understanding the specific requirements of the fluid system. Factors such as the type of fluid, pressure conditions, and pipeline dimensions influence the selection process. With advancements in manufacturing, some DI air valves are now equipped with smart features that allow remote monitoring and control, providing operators with real-time data to optimize performance and maintenance schedules. In one anecdotal instance, a client reported a 30% increase in operational efficiency after installing smart DI air valves, underscoring its potential benefits.
Trustworthiness in this domain is built through rigorous testing and adherence to industry standards. Credible manufacturers subject DI air valves to stringent quality checks, ensuring that each valve meets the requisite safety and performance benchmarks. A key recommendation is to always choose suppliers who have a proven track record and positive reviews from industry peers, which signals reliability and product excellence.
In conclusion, DI air valves are indispensable to modern fluid management systems, offering a perfect blend of experience-driven insights and technical prowess. Their role in enhancing pipeline efficiency, longevity, and safety speaks volumes about their importance in industrial applications. Continuous advancements and innovations in this field promise even greater reliability and operational benefits, ensuring that DI air valves remain a cornerstone of fluid dynamics technology.