Flow control check valves are essential components in various industrial systems, playing a critical role in regulating and maintaining the directionality of fluid flow. These devices ensure that flow moves in a singular direction,
thereby preventing backflow and potential system failure. Given their importance, understanding the functionality, applications, and benefits of flow control check valves can empower industries to optimize their operations and prioritize system integrity.
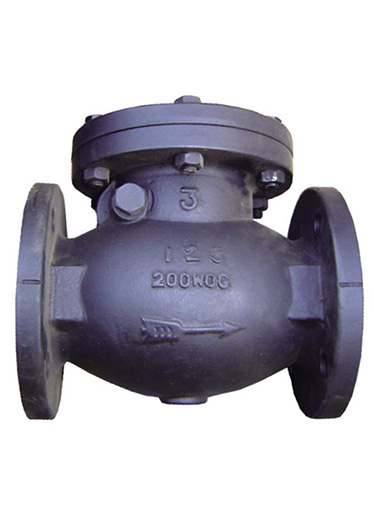
Expertise in the selection and utilization of flow control check valves requires a profound understanding of the mechanics involved. These valves operate automatically; their design allows them to respond to the changes in flow pressure and direction. There are several types of check valves used across industries, including swing check valves, lift check valves, and dual plate check valves, each offering unique benefits depending on the specific application and fluid type involved.
In terms of practical application, flow control check valves are predominantly used in systems where backflow contamination must be avoided. For instance, in water treatment facilities, these valves are crucial as they help maintain hygiene and system efficiency by preventing contaminants from entering clean water supplies. Likewise, in the oil and gas industry, they prevent reverse flow, which could otherwise lead to equipment damage and safety hazards.
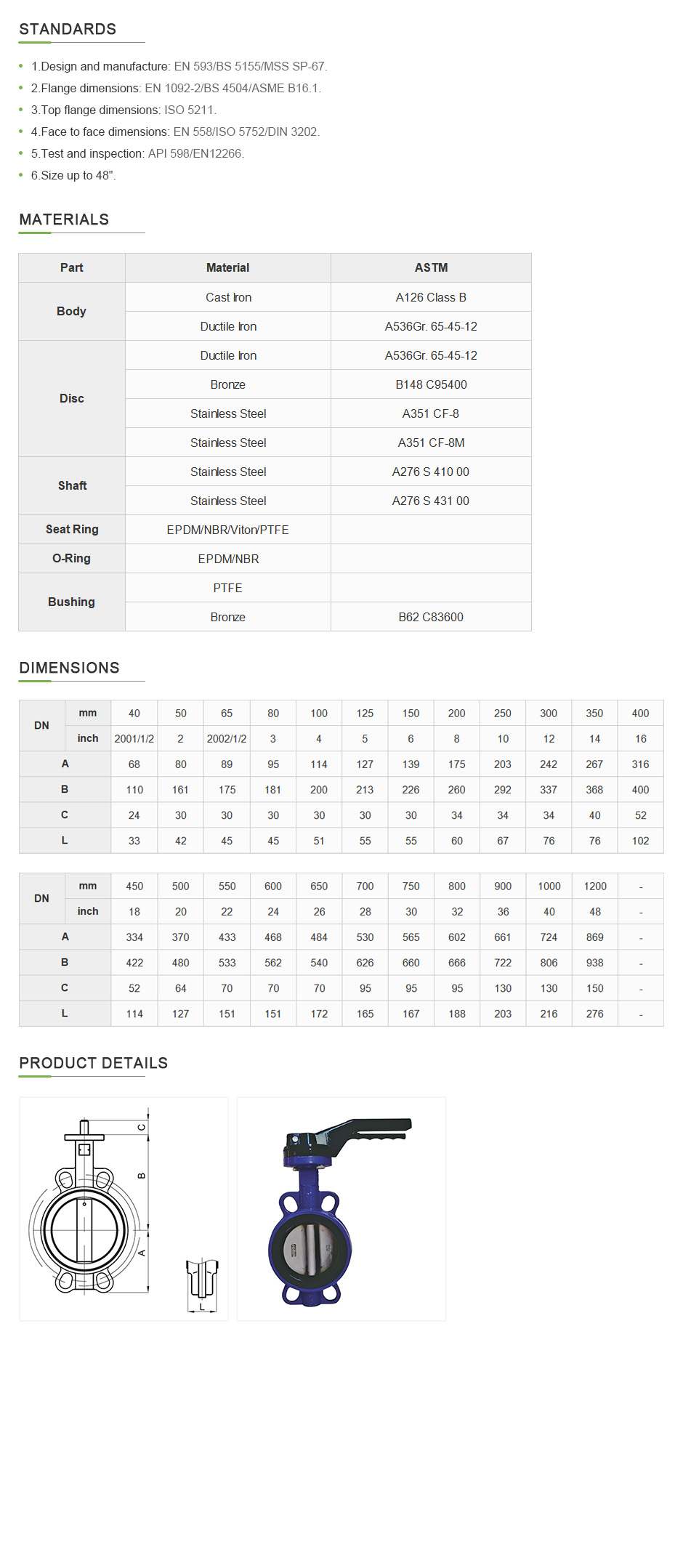
Authoritativeness in the field comes from understanding these applications and recognizing the standards and regulations governing their use. The American Society for Testing and Materials (ASTM) and the American National Standards Institute (ANSI) provide guidelines ensuring that check valves meet safety and functionality requirements. Familiarity with these standards helps in choosing the right valve for any given system, guaranteeing compliance and enhancing operational safety.
Trustworthiness is built by relying on both transparent communication from manufacturers and consistent performance of the check valves under varied operational conditions. Manufacturers with a track record of innovation and quality assurance, such as those producing valves with advanced composite materials, offer reliable solutions. These materials provide enhanced resistance to corrosion and wear, even under extreme temperatures or aggressive fluids.
flow control check valve
When discussing real-world experiences, it is worth noting how businesses have leveraged flow control check valves to drive efficiency and cost-effectiveness. Successful implementation can lead to reduced maintenance costs, prolonged equipment life, and minimized downtime. A dairy processing plant, for example, was able to decrease contamination risks and increase productivity by integrating high-quality check valves that provided seamless and reliable performance.
Continuous advancements in flow control check valve technology are broadening the possibilities for various applications. Recent innovations include the development of intelligent check valves integrated with sensors that provide real-time data on flow conditions. This technological leap allows for predictive maintenance and enhanced system monitoring, further elevating the reliability and efficiency of industrial operations.
Finally, ensuring the right fit for system requirements necessitates a strategic approach to valve selection. Considerations such as pressure ratings, temperature limits, material compatibility, and flow characteristics are crucial in choosing the appropriate valve. By aligning these factors with operational demands, industries can ensure optimized performance, sustainability, and safety.
Adept management of flow control check valves within any system is indicative of expertise, underscoring a company’s commitment to excellence and operational robustness. In summation, understanding the intricacies of flow control check valves not only supports engineering acumen but fosters a culture of trustworthiness and reliability, driving industry standards and expectations.