The world of electric cable wire manufacturing is both vast and intricate, and it calls for keen attention to detail and deep expertise to truly excel. In the landscape of manufacturing, specifically concerning electric cables and wires, numerous factors influence the process and the quality of the final products, ensuring their suitability for countless applications in both commercial and residential settings. For anyone venturing into this industry or seeking products for high-stakes projects, understanding the nuances of cable manufacturing is paramount.
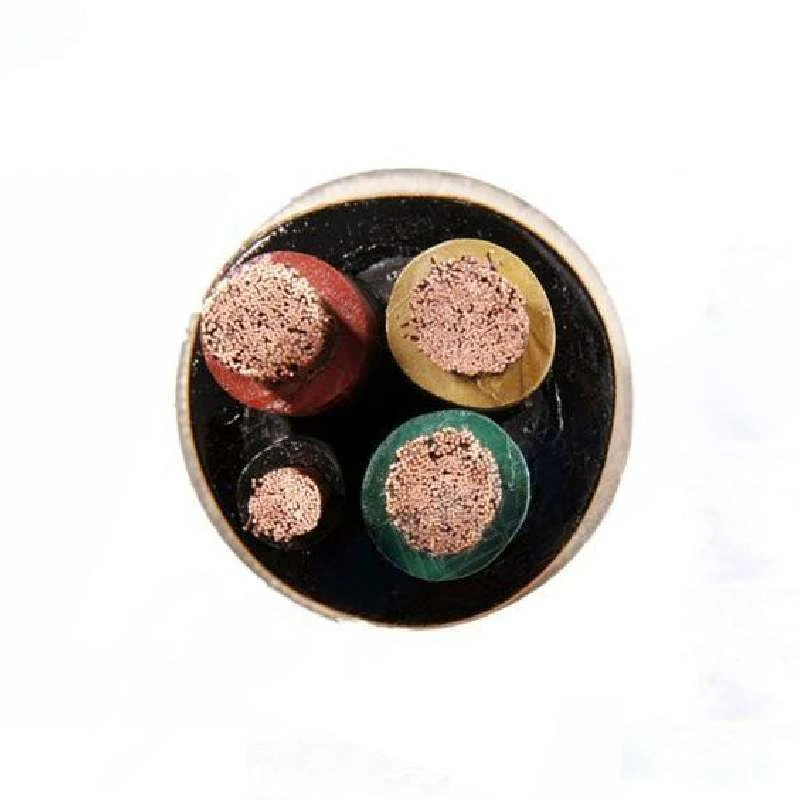
Electric wire and cable manufacturers play an essential role in the global infrastructure framework. The first step in the process involves the meticulous selection of raw materials, primarily copper or aluminum, given their exemplary conductivity and flexibility. A reputable manufacturer will prioritize the purity and quality of these raw materials. Ensuring that the copper or aluminum meets industry standards in terms of conductivity can significantly impact the efficiency and safety of the wires produced.
Once the raw materials are secured, manufacturers engage in the drawing process whereby the metals are pulled through dies to reach the desired thickness or gauge. Precision during this step is vital, as inconsistencies in wire gauge can lead to compatibility issues or potential safety hazards in their eventual application. Manufacturers equipped with cutting-edge technology and machinery can achieve greater consistency, thereby boosting the wire's reliability.
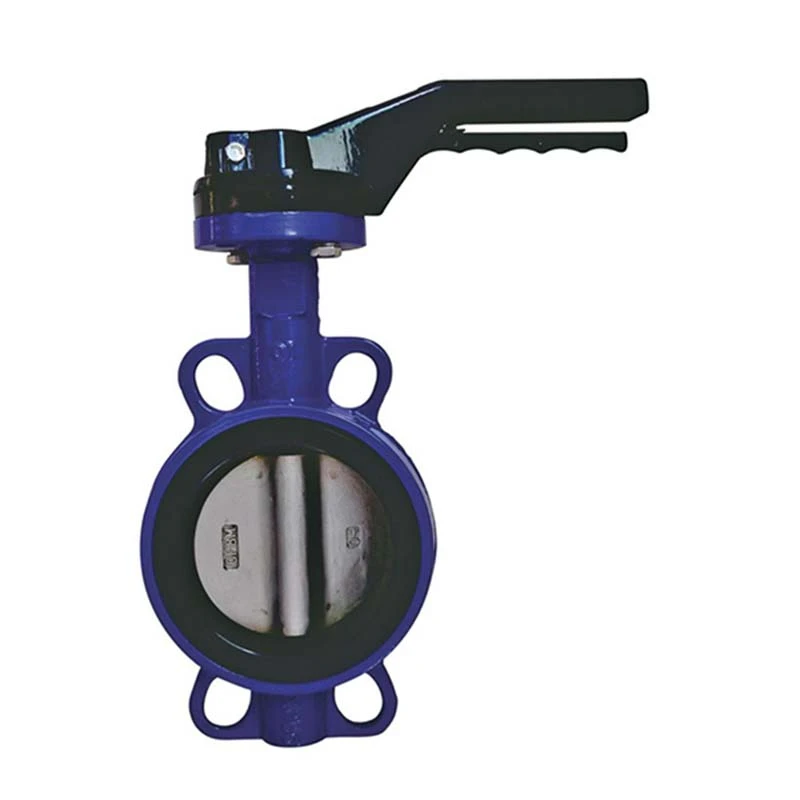
The next critical phase is the annealing process, a heat treatment that enhances the ductility of metals after drawing. Expert manufacturers excel in controlling the temperature and duration of annealing, directly impacting the pliability and longevity of the wire. Properly annealed wires perform better under stress and resist wear over time, underscoring the importance of expertise and experience in this stage.
A vital aspect of manufacturing electric cables is insulation. Manufacturers use a variety of insulation materials such as PVC, XLPE, or PTFE, chosen based on the wire’s intended application, environmental conditions, and voltage requirements. The insulation process, conducted with precision, not only safeguards the conductor but also enhances its functional capabilities by providing resistance against electrical leakage, moisture, and chemical exposure. High-quality insulation is non-negotiable, especially for applications in challenging environments where wires are exposed to extreme temperatures or corrosive elements.
electric cable wire manufacturer
In terms of authority and trustworthiness, manufacturers who embrace industry standards such as ISO certification demonstrate a commitment to quality and safety. These standards influence every layer of the manufacturing process, from initial design to final inspection, ensuring the product meets stringent reliability and performance benchmarks. Moreover, manufacturers who engage in continuous research and development foster innovation, constantly improving their products' efficiency and sustainability. This forward-thinking approach is essential in an increasingly eco-conscious market where demand is growing for environmentally friendly materials and energy-efficient solutions.
Moreover, an established manufacturer will have a transparent traceability system that allows clients to verify the provenance and compliance of their products. This transparency fosters trust and solidifies the manufacturer's stand in a competitive market. Providing detailed test reports and quality assurance documentation is indicative of a company that values its reputation and clients' peace of mind.
Manufacturers that emphasize customer experience differentiate themselves by providing personalized services such as custom cable design and technical support. They work closely with clients to understand their specific needs, offering bespoke solutions that are both innovative and practical. This client-centric approach ensures that every product not only meets technical requirements but also aligns seamlessly with the client’s project goals.
To remain relevant and authoritative, leading manufacturers also invest in training and development, ensuring their teams remain at the forefront of industry advancements. Whether it's adopting new technologies, updating manufacturing processes, or refining quality control protocols, manufacturers must stay agile and informed of the latest trends and scientific breakthroughs.
In conclusion, the expertise and experience that a manufacturer brings to the table dramatically influence the quality and reliability of electric cables and wires. Those committed to excellence in manufacturing set themselves apart through stringent adherence to industry standards, innovative practices, and an unwavering commitment to customer satisfaction. In an industry where the margin for error is nil, choosing the right manufacturer can make all the difference in ensuring infrastructural resilience and operational safety. Such dedication to quality not only wins trust but also solidifies the manufacturer’s status as a leader in the ever-evolving landscape of electric cable production.