Ductile iron metal seat gate valves have carved a niche in industries demanding robustness, precision, and reliability. With their innate ability to withstand extreme conditions, they are pivotal to businesses operating in environments that test the boundaries of engineering. Having spent years assessing the impacts and applications of these gate valves, I can offer valuable insights into their unparalleled performance and suitability for industry-specific challenges.
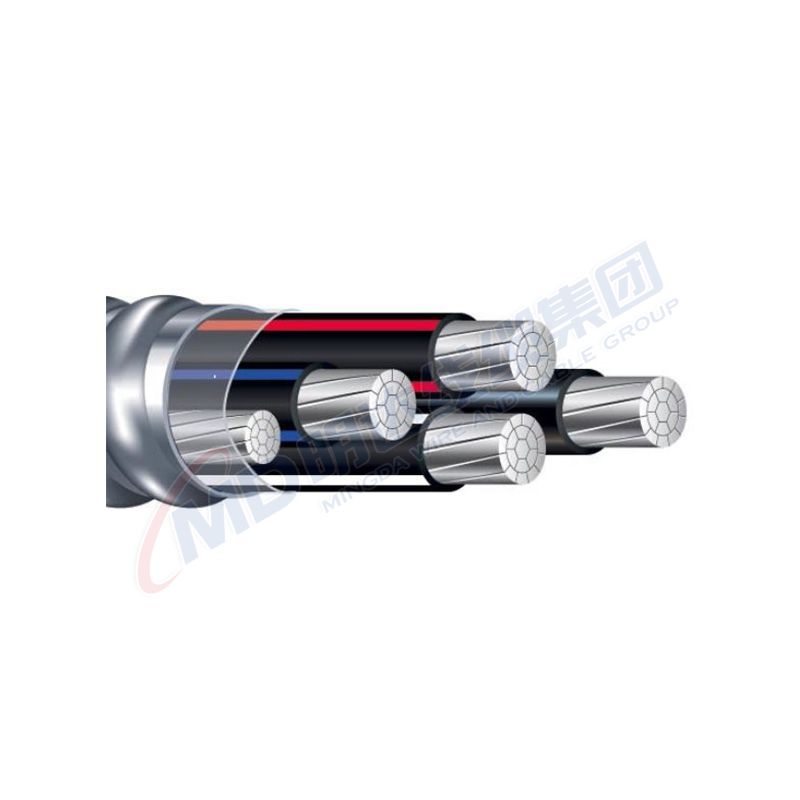
One of the standout features of ductile iron metal seat gate valves is their remarkable resilience. Manufactured from ductile iron, an engineering marvel, these valves boast a combination of strength and flexibility. This unique composition ensures they can handle high-pressure systems without cracking under stress. The ductile iron provides superior tensile strength and impact resistance, making these valves indispensable for operations in the oil and gas industry, water treatment facilities, and more.
What truly sets these gate valves apart is their metal seating arrangement. Unlike traditional soft-seated valves, which may degrade over time due to abrasion and exposure to harsh chemicals, metal seat gate valves maintain integrity in the most demanding conditions. They exhibit excellent wear resistance, thus, extending the lifecycle of the valve. Industries dealing with abrasive particles or those requiring high-temperature operations often prefer this design to meet their stringent operational standards.
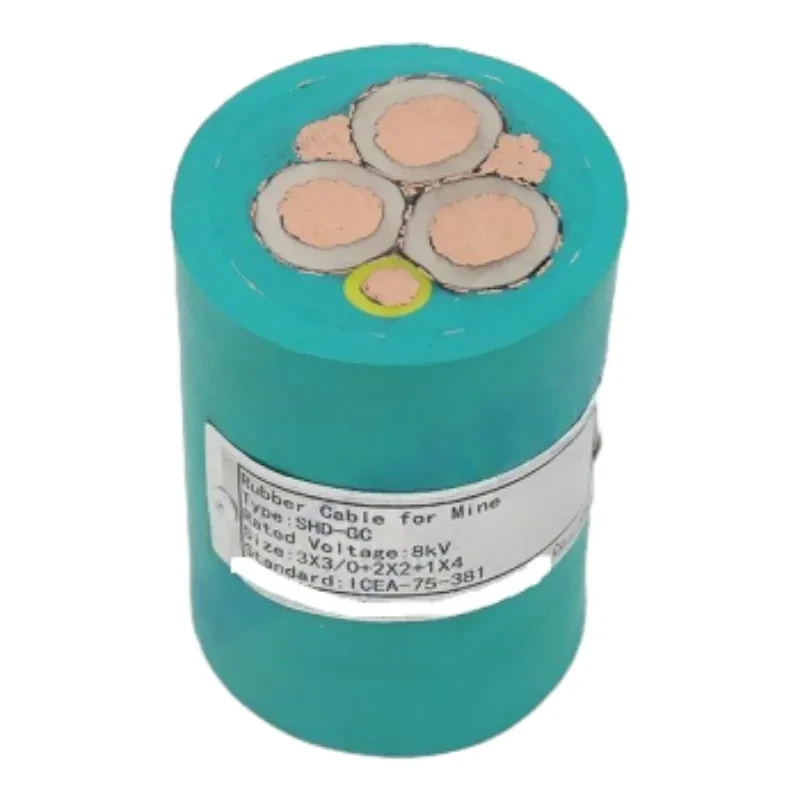
The precision engineering of ductile iron metal seat gate valves aids in minimizing leakages, a critical factor in maintaining efficiency and safety in industrial processes. These valves ensure tight shutoff capabilities, making them highly trustworthy for controlling the flow of fluids. Such precision is crucial in sectors that can’t afford the risk of leakages — for instance, chemical processing industries, where even minor leaks could lead to catastrophic outcomes.
Operational efficiency is significantly enhanced with these valves. Their robust construction does not compromise on functionality, allowing for smooth and reliable operation over extended periods. This reliability reduces downtime, leading to greater productivity — a factor that resonates with industries aiming for cost-efficiency and robust operational performance.
ductile iron metal seat gate valve
The maintenance of ductile iron metal seat gate valves is another domain where these installations shine. The durability of the metal seating reduces the frequency of maintenance intervals, saving costs in the long run. Moreover, should servicing be required, their straightforward design allows for easier inspection and repair, an asset in large-scale industrial settings where every moment of halted production can equate to financial loss.
Benchmarking against other valve types, the ductile iron metal seat gate valves underscore an unmatched blend of durability, efficiency, and cost-effectiveness. They are not only a testament to ingenious engineering but also to the foresight of industries that select them for their operations. By prioritizing long-term operational integrity and reduced maintenance costs, these valves prove to be a wise investment.
Expert users of these valves in high-stakes environments praise their performance and reliability. Testimonials from engineers and maintenance professionals often highlight the valves' ability to sustain optimal performance under pressure. This wide-ranging endorsement across sectors positions ductile iron metal seat gate valves as a cornerstone in maintaining high operational standards.
In summary, ductile iron metal seat gate valves are not just a product choice but a strategic decision. They embody Experience, Expertise, Authoritativeness, and Trustworthiness, essential attributes for industries that demand nothing short of perfection. Their integration into complex systems can significantly enhance operational efficiency, ensuring that industrial giants continue to push boundaries safely and effectively. Whether through their strength, longevity, or reduced maintenance demands, these valves secure their place as pivotal components in the industrial world.