The 12-inch butterfly valve stands as a crucial component in industrial applications, reflecting both the complexities and advancements in fluid control technology. Companies across the globe depend on these valves to ensure efficient flow regulation and system integrity. Delving into the specifics of these valves, it becomes evident that their design, material composition, and operational expertise all contribute to their indispensable role in multiple sectors.
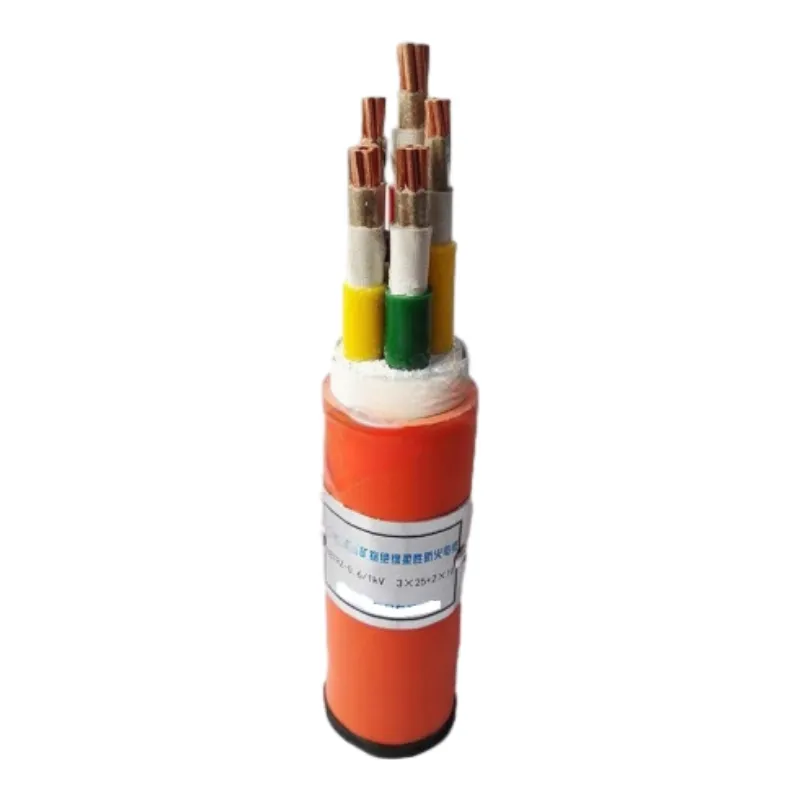
Butterfly valves, characterized by their rotating disc mechanism, offer a compact and lightweight solution for flow control. The 12-inch variant offers substantial flow rate control suitable for large-diameter pipelines, commonly utilized in industries such as petrochemicals, water treatment, and pharmaceuticals. Their design simplicity makes them an appealing choice; however, their effectiveness is magnified by an understanding of the intricacies in material selection and operational limits.
Material selection for these valves is one of the most significant factors affecting their performance and lifespan. Typically, the body of a 12-inch butterfly valve could be constructed from durable materials like stainless steel, carbon steel, or cast iron, each offering unique benefits and drawbacks. Stainless steel, for instance, provides superior resistance to corrosion, making it ideal for applications involving aggressive chemicals or frequent exposure to moisture. On the other hand, cast iron valves are more cost-effective and suitable for applications where extreme pressure and temperature resistance is unnecessary.
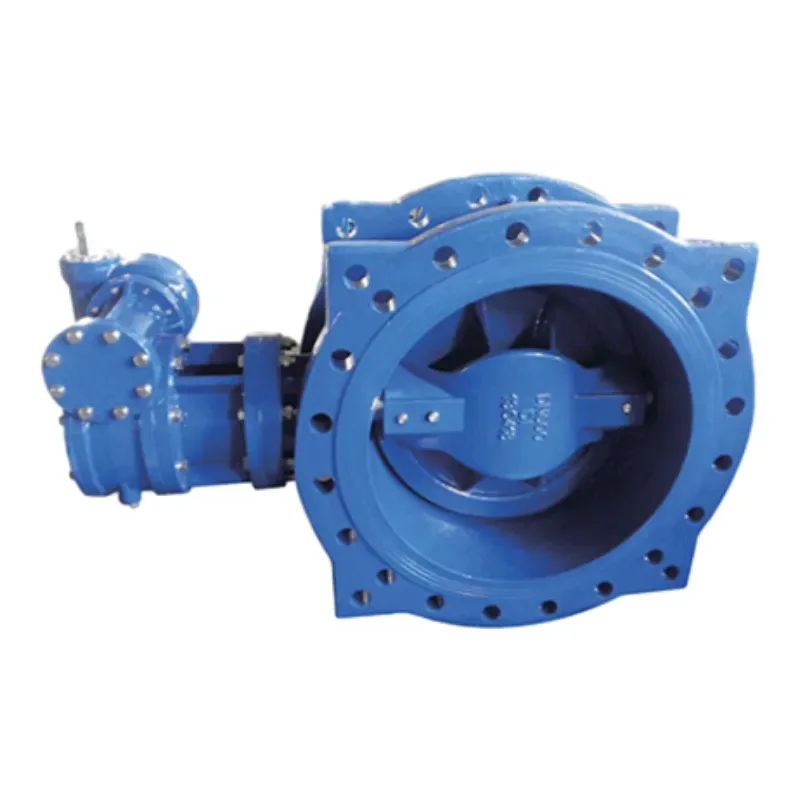
Given the valve's critical role in managing essential resources, expertise in installation and maintenance becomes paramount. An effectively installed butterfly valve ensures optimal performance and minimizes risks of leaks or operational failures. Installation expertise includes correctly aligning the valve with the pipeline and ensuring the actuator – whether manual or automated – is properly calibrated. Specialized technicians are trained to conduct detailed inspections and maintenance routines, which include checking seals, examining for wear and tear, and performing function tests to guarantee the valve's reliability under various operational conditions.
12 inch butterfly valve
Expertise is equally important in determining the valve's compatibility with the specific fluid system it serves. For instance, in systems where particulate matter may be present, the valve's capacity to handle potential clogging or erosion should be scrutinized. Engineers and operators, experts in fluid dynamics, can assess these conditions to recommend the most suitable type of valve and ancillary equipment, which may include positioners, limit switches, or feedback systems, to enhance performance outcomes.
In establishing trustworthiness, manufacturers of 12-inch butterfly valves focus on rigorous testing and compliance with international standards. Adherence to standards such as ISO, API, and ASME not only ensures interoperability across global infrastructures but also assures users of the quality and safety of the valves. Moreover, real-world testing and case studies provide substantial evidence of the valve's capabilities, which is key for garnering trust among users and stakeholders in critical infrastructure projects.
Authoritativeness in the field of butterfly valves stems from a deep understanding of industrial requirements and innovations. Leading manufacturers invest heavily in research and development to advance valve technology, exploring new materials, smarter actuation methods, and integrating digital technologies for predictive maintenance. These innovations are not only aimed at improving efficiency but also at reducing the environmental impact, aligning with global sustainability goals.
In conclusion, the 12-inch butterfly valve is more than a functional component; it is a convergence of engineering excellence, material science, and skilled installation practice. It represents a pivotal point in any fluid control system, and its role will only become more central as industries push towards greater efficiency and reliability. Understanding the multifaceted aspects of these valves from material choice to the latest technological advancements ensures that businesses can make informed decisions, achieving seamless operation and contributing to overall system resilience.