Flange adaptors and dismantling joints are indispensable components in the domain of pipeline engineering, serving pivotal roles in ensuring the effective and efficient management of fluid movement across complex pipeline systems. Through years of industry observations and expertise, the utilization and intricacies of these essential tools can be explored and understood in profound ways, underscoring their relevance to anyone vested in industrial solutions.
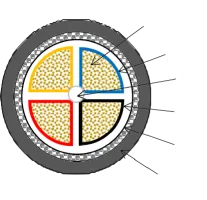
Flange adaptors are ingenious devices designed to connect pipes of different diameters swiftly and securely. This capability to join disparate pipeline infrastructures without the need for extensive modifications makes them a sought-after solution in pipeline design and repair. The expertise in their application ensures seamless integration and extends the longevity of pipelines, reducing downtime and potential financial losses. A testament to their versatility, flange adaptors are prized in various sectors from water treatment plants to fire protection and power generation facilities.
Notably, the material choice for flange adaptors is a calculated decision based on system requirements and the type of media being transported. Typically fabricated from robust materials like stainless steel, ductile iron, or PVC, their corrosion-resistant properties are evaluated under rigorous standards. This ensures the joint's integrity over long periods and against potential chemical interactions. Industry professionals consistently emphasize the importance of procuring adaptors from manufacturers with certifications that uphold international quality standards, which enhances trustworthiness in their application.
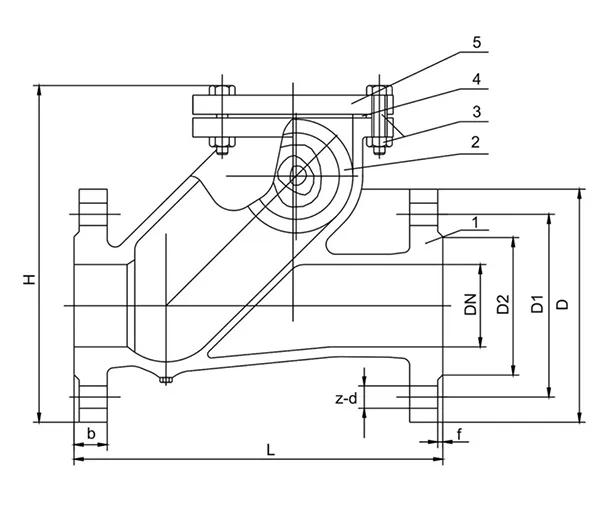
In parallel, dismantling joints are engineered to perform a dual function joining sections of pipeline systems and facilitating maintenance or equipment replacement with relative ease. The design of dismantling joints allows for axial movement, which is critical during installation or removal processes. This feature significantly reduces labor intensity and time spent, fortifying their value proposition in modern pipeline infrastructure. Moreover, due to their ability to absorb intense axial and transverse stresses, dismantling joints are crucial in environments subjected to high vibrations or thermal variations.
flange adaptor and dismantling joint
From an authoritative perspective, dismantling joints are integral to municipal infrastructure projects where continuity and reliability of service are non-negotiable. They serve as a protective mechanism against potential pipeline failures by accommodating structural shifts due to various environmental factors. Experience shows that without these essential components, pipeline systems would be prone to frequent service disruptions, undermining public trust and safety.
In regions susceptible to seismic activity, the robustness and flexibility offered by flange adaptors and dismantling joints are indispensable. Their capability to provide an adaptive solution in shifting terrains enhances a pipeline's resilience against natural disasters. Such deployment underlines a commitment to infrastructural integrity, showcasing a knowledge-based approach in engineering circles to anticipate and mitigate potential risks.
To gain the most from flange adaptors and dismantling joints, collaboration with seasoned engineers and maintenance experts is critical. Such collaboration ensures that these components are fitted precisely according to engineering specifications, and regular inspections are advised to detect wear and uphold safety standards. Furthermore, investing in advanced coating technologies for these joints can offer additional protection against corrosion, significantly extending their operational lifespan and ensuring long-term reliability.
In conclusion, flange adaptors and dismantling joints exhibit an extraordinary confluence of engineering prowess, practical application, and industry endorsement. Their crucial role in infrastructure highlights the need to balance robust design with adaptability, ensuring pipelines serve communities effectively and efficiently. The commitment to quality, demonstrated through rigorous testing and adherence to global standards, resonates with stakeholders, reinforcing confidence in their lasting capabilities. As such, they remain a cornerstone of modern pipeline infrastructure, testament to innovation meeting necessity.