Flanged ball valves are pivotal components in various industrial applications, known for their efficiency and reliability. Their widespread use across different industries such as oil and gas, water treatment, and chemical processing underscores their significance. A robust understanding of their features, applications, and maintenance is essential to appreciate their role in optimizing industrial operations.
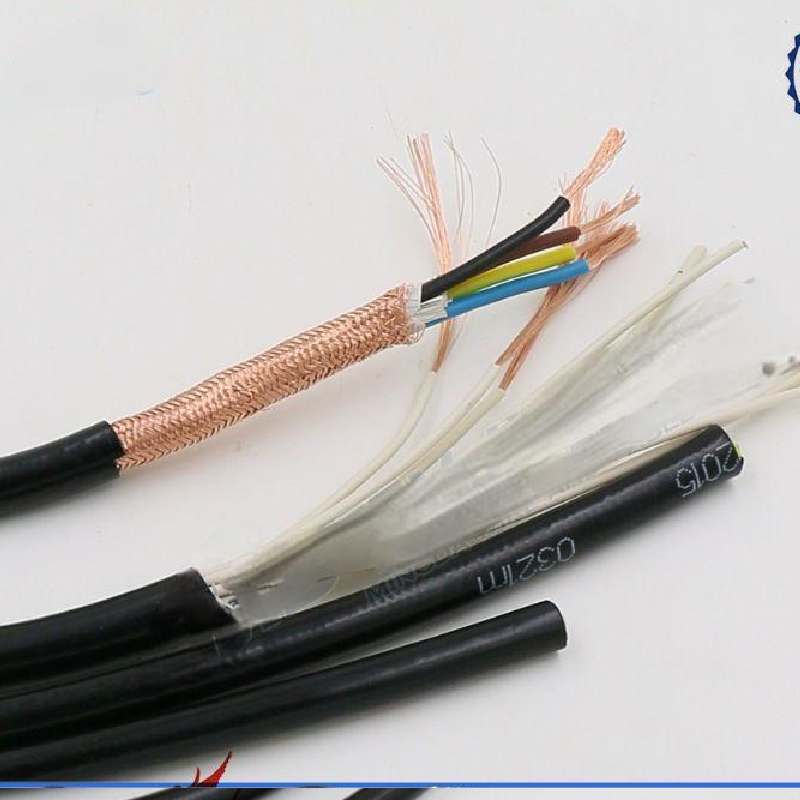
Expertise in engineering and design marks the superiority of flanged ball valves. Unlike conventional valves, these valves boast a spherical disc with a hole in the middle, which controls the flow of liquids and gases. The flange design allows for ease of connection to pipe systems, ensuring a secure fit that minimizes leakage risks. The valves can easily handle high pressure and temperature, making them indispensable in critical operations where reliability is paramount.
Their accuracy in controlling the flow rate offers significant operational advantages. By simply turning the actuator, the ball inside the valve opens or closes the passage, providing precise control over fluid dynamics. This mechanism not only facilitates efficient flow management but also contributes to energy conservation by minimizing pressure drops. Companies that integrate flanged ball valves into their systems often experience enhanced process control, which translates into operational cost savings and increased throughput.
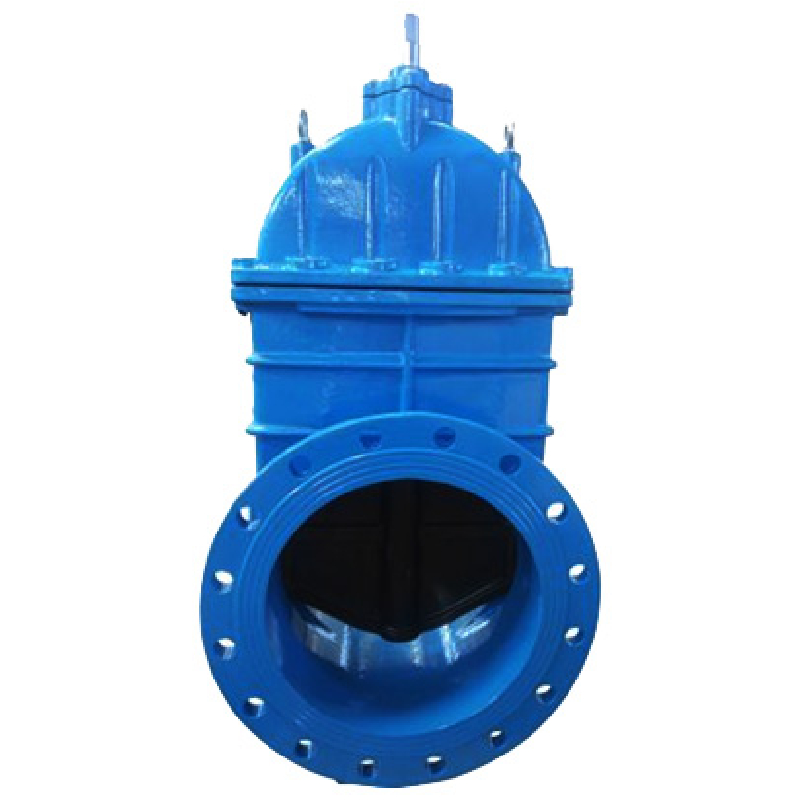
Experience in industries that rely on flanged ball valves reveals their durability and low maintenance requirements. Typically constructed from high-quality materials like stainless steel, carbon steel, or PVC, these valves are designed to withstand corrosive substances. This resistance to wear and tear ensures longevity, which is critical for maintaining continuous operations without frequent disruptions for repairs. The ease of maintenance – often requiring just routine checks and lubrication – further bolsters their appeal, allowing companies to focus resources on production rather than repairs.
flanged ball valve
Authoritativeness in the production and supply of flanged ball valves is demonstrated by compliance with international standards and regulations. Reputable manufacturers ensure their products meet or exceed standards set by organizations such as ANSI, API, and ISO. This compliance guarantees users that their operations will adhere to safety and quality benchmarks, reducing the risk of accidents and enhancing operational trust.
Trustworthiness is built upon a proven track record of performance and customer satisfaction. Case studies and client testimonials often highlight the reliability of flanged ball valves in diverse challenging environments. Industry professionals consistently report positive experiences with lifecycle cost efficiencies and minimal downtime. Furthermore, comprehensive warranties and responsive customer service from manufacturers and suppliers help reinforce client confidence in the product's reliability.
In summary, flanged ball valves are a quintessential component in industrial flow control systems. Their expert design, operational efficiency, and low maintenance requirements make them a vital investment for industry leaders. Their compliance with authoritative standards and the trust they garner from consistent, positive user experiences further cement their status as a foundational tool in achieving both operational excellence and economic efficiency. As industries continue to evolve, the role of flanged ball valves in supporting sustainable and efficient operations remains as crucial as ever.