Wafer type butterfly valves are an essential component in the modern industrial world, providing efficient flow control solutions across various sectors such as water treatment, chemical processing, and HVAC systems. Having spent over a decade in the field of fluid dynamics engineering, I've seen firsthand how the design and function of these valves can significantly impact operational efficiency and system longevity.
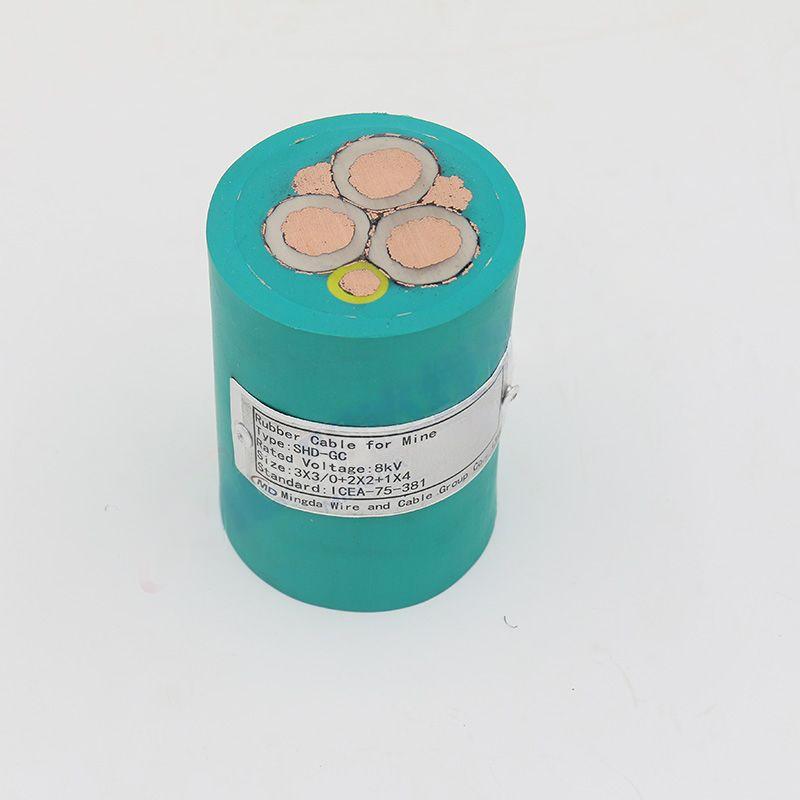
The wafer type butterfly valve is uniquely designed to be sandwiched between two flanges. Its compact design makes it an ideal choice for systems where space is limited. The primary components of this valve include a disc that rotates around a central axis to either allow or block the flow of fluid. This seemingly straightforward mechanism is empowered with engineering innovation that demands expertise and reliability.
In my experience, selecting the right material for the valve construction is paramount to its success in harsh environments. Common materials for the disc and body include stainless steel, ductile iron, and upvc, each offering distinct advantages depending on the application. Stainless steel provides excellent corrosion resistance, which is indispensable in chemical processing, while ductile iron is ideal for water distribution due to its durability and strength.
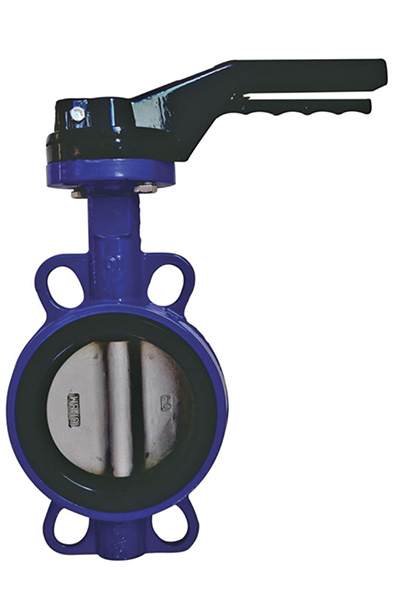
A crucial aspect of wafer type butterfly valves is their ability to support bidirectional flow. This feature is especially beneficial in dynamic systems where fluid direction changes frequently. The valve’s reduced weight compared to other valve types leads to easier installation and maintenance, a factor contributing heavily to lowered operational costs.
One might ask about the sealing mechanism in wafer type butterfly valves and its efficacy in preventing leaks. High-performance variants are equipped with elastomer-based seats or a metal-to-metal seal, each engineered to endure different pressure ratings. An elastomer seat provides an excellent seal in low to medium pressure systems, while the metal-to-metal seal withstands higher pressures and temperatures, offering expert-level assurance against leakage even in severe conditions.
wafer type butterfly valve
Simplicity and cost-effectiveness do not compromise sophistication.
Advanced variants of this butterfly valve incorporate automation technologies, allowing integration with modern control systems. Automation enhances accuracy in process control, optimizing system performance, which aligns with the industry's move toward Industry 4.0. The ability to remotely control these valves also adds a layer of safety, minimizing the need for manual operation in potentially hazardous environments.
Beyond technical specifications, the credibility of the manufacturer plays an integral role in the effectiveness of the valve. Choosing a manufacturer with a proven track record ensures access to robust products backed by rigorous testing and quality assurance. It's essential to collaborate with manufacturers who not only comply with industry standards such as ISO and API but also consistently innovate based on user feedback and technological advancements.
Finally, trustworthiness in wafer type butterfly valves extends to their adaptability in diverse applications. Their simplicity in design allows them to be tailored for various service requirements with minimal modifications. Whether it's retrofitting an existing system for increased capacity or designing a new build, the wafer type butterfly valve remains a trusted solution due to its versatility and reliability.
In conclusion, wafer type butterfly valves are an effective solution due to their engineering efficiency, material versatility, and operational reliability. With a blend of simplicity and the capacity for sophistication through automation, they accommodate the growing demands of modern industries. Selecting these valves with a focus on expert manufacturer credibility and matching valve configurations with specific operational needs ensures long-lasting and trustworthy system performance.