When it comes to efficient fluid control in industrial and domestic applications, silent check valves have emerged as a critical component ensuring smooth operations. Engineered to prevent reverse flow in a piping system, silent check valves are distinguished by their ability to function with minimal noise, a feature highly valued in environments sensitive to sound disturbances. This essay delves into the intricacies of silent check valves, highlighting their design, applications, benefits, and pivotal role in modern engineering.
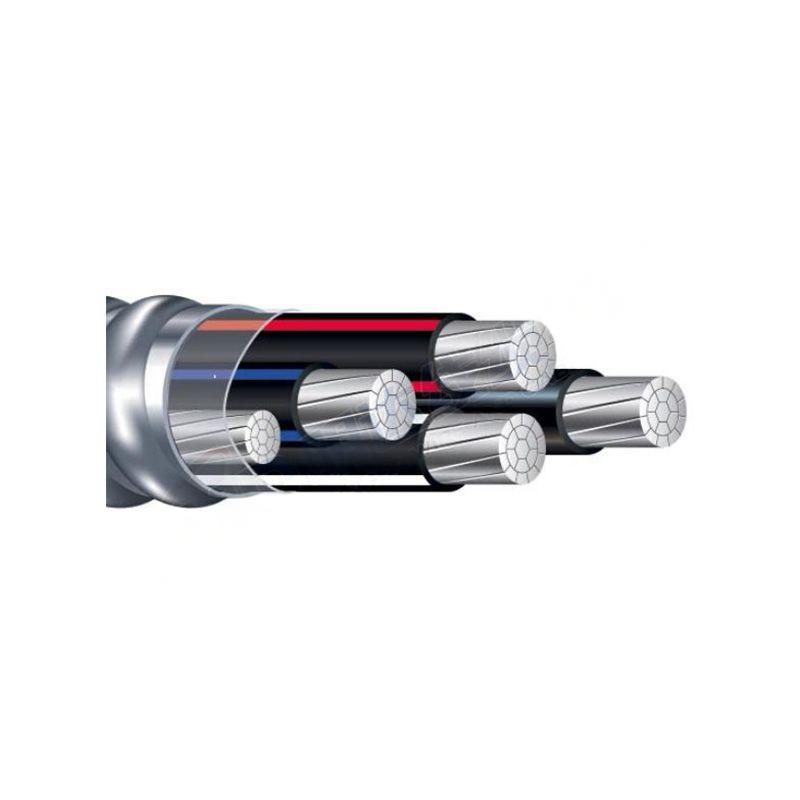
At the heart of silent check valve technology lies a spring-assisted disc mechanism that responds fluidly to changes in pressure. Unlike conventional swing check valves, which can slam shut and create water hammer—a shockwave that can damage pipes and fittings—silent check valves close gradually. This gradual closing is primarily due to the spring assistance that pushes the disc toward the seat, preventing any backflow. This mechanism not only reduces noise to near silence but also diminishes potential wear and tear on infrastructure.
The expertise in the design of silent check valves stems from precise engineering principles that focus on longevity and reliability. Manufacturers devote significant research and development resources to perfect the balance between flow efficiency and noise reduction. Materials such as stainless steel, brass, and PVC are carefully selected for their durability and corrosion resistance, ensuring the valve's performance across diverse environments. Advanced computational fluid dynamics (CFD) software is often employed to simulate flow through the valve, optimizing the design for minimal pressure drop and optimal closure times.
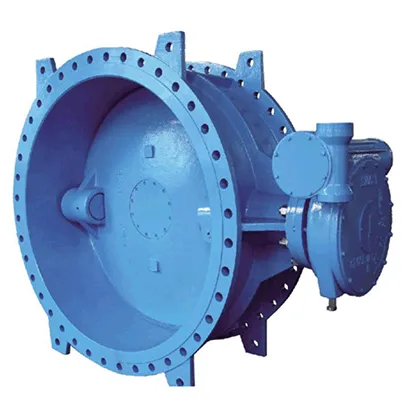
Silent check valves are authoritative in numerous applications. In HVAC systems, where constant circulation of fluids is vital, they maintain seamless operation without disrupting the ambient silence expected in residential and office spaces. Industrial facilities handling corrosive liquids or extreme temperatures rely on these valves to uphold system integrity by preventing reverse flow, which could otherwise lead to catastrophic failures. Additionally, in municipal water systems, silent check valves play a critical role in maintaining consistent water pressure and preventing contamination from reverse flows, thereby safeguarding public health.
Trustworthiness in silent check valves is evidenced by stringent industry standards and certifications. Compliance with standards such as API, ANSI, and ASME reassures engineers and operators of the valve's quality and compatibility with existing systems. Manufacturers often subject these valves to rigorous testing for pressure resilience, longevity, and accurate operation, providing comprehensive documentation and traceability to back their claims. Furthermore, many brands offer extended warranties, reflecting confidence in their product's reliability and performance.
silent check valve
Interestingly, the evolution of silent check valves has seen an increase in smart valve technology integration. Smart valves equipped with sensors and connectivity modules provide real-time data on flow rates, pressure changes, and valve positioning. This technological leap enhances preventive maintenance, as operators can anticipate issues before they manifest, ensuring uninterrupted service and extended equipment lifespan.
For stakeholders considering the adoption of silent check valves, real-world experience underscores their value. Many facilities report significant reductions in maintenance costs and system downtime after replacing traditional check valves with silent alternatives. Their unobtrusive nature also contributes to a more comfortable acoustic environment, which can be critical in locations where noise pollution is a concern.
Investing in silent check valves is not merely about current operational improvements; it is a forward-thinking approach that aligns with sustainability goals. Reduced wear and tear extend the valve's life, minimizing frequent replacements and the associated carbon footprint of manufacturing and transport. Their efficiency in maintaining steady flow contributes to energy savings, a non-negligible factor considering the rising global energy demands.
In conclusion, silent check valves encapsulate a blend of expert engineering, authoritative application, and reliable performance. Their design not only addresses the need for quiet operation but also elevates system integrity and efficiency. As industries evolve and demand precision and silence in equal measure, silent check valves stand out as indispensable components, embodying a seamless fusion of innovation and practicality. Whether in high-stakes industrial setups or everyday water supply systems, the silent check valve is undeniably a hallmark of advanced fluid management technology.