Understanding the nuances of gate valves, especially the non-rising stem (NRS) variant, is essential for making informed decisions about installation and maintenance. These components play a critical role in controlling fluid flow in a variety of applications, ranging from water treatment facilities to chemical processing plants.
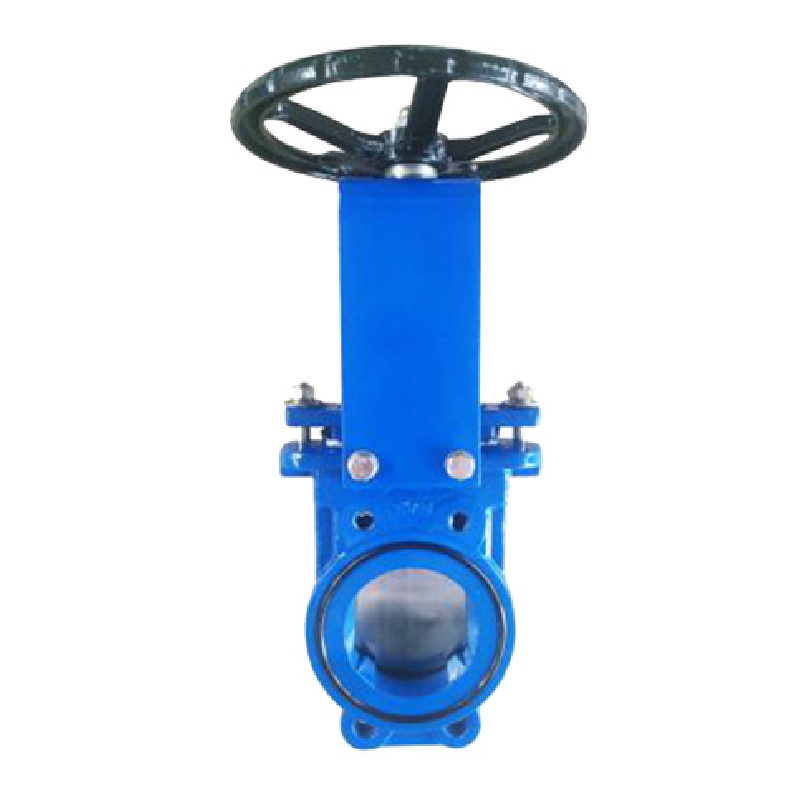
The NRS gate valve is designed with a stem that remains stationary during the operation of opening or closing the gate. This design is particularly beneficial in scenarios where vertical space is limited, as the non-rising stem moves inside the valve. One of the defining advantages of this design is its compact nature, making it ideal for underground or space-constrained installations. Additionally, the enclosed stem design helps protect against external damage and reduces exposure to the elements, boosting its longevity.
A personal journey into the world of gate valves reveals the complexity and essential nature of product choice. After years in the industrial equipment sector, I have witnessed firsthand the pivotal role gate valves play in ensuring smooth and efficient operations. When implemented correctly,
an NRS gate valve can offer unparalleled reliability. However, selecting the right valve is not merely about understanding its immediate functionality but involves an appreciation of its broader impact on system efficiency and cost savings.
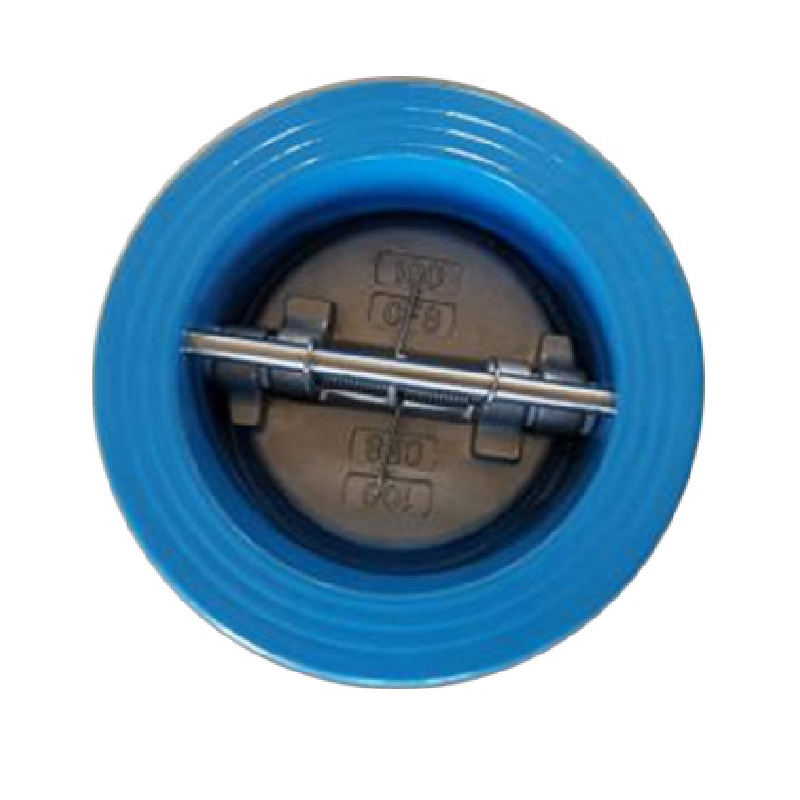
Professionals in fluid management industries can attest to the critical nature of precise valve selection. Expertise in this realm goes beyond simple installation—knowing the exact specifications required for specific environments is paramount. The non-rising stem gate valve, for instance, is often constructed from robust materials such as stainless steel or cast iron, each material offering varying benefits of corrosion resistance or strength. This depth of material choice ensures that regardless of the application, there is a suitable variant that can withstand the specific demands of the environment.
gate valve nrs
Authority in the field of gate valve technology is often established by a continuous commitment to innovation and adaptation. The industry is rife with rapidly evolving technologies that promise enhanced performance and sustainability. Keeping abreast of these changes is crucial for maintaining relevance and ensuring consumers have access to the best possible solutions. Industry leaders routinely invest in research and development to refine valve designs, improve efficiency and reduce environmental impact.
With trust as a cornerstone of industrial product selection, choosing a reputable manufacturer can greatly enhance overall satisfaction and safety. Trustworthiness is cultivated through years of demonstrated success, rigorous quality assurance processes, and adherence to international standards. Products backed by certifications from recognized organizations provide an extra layer of security and peace of mind to users. Offering detailed support and transparent warranties further solidifies a company’s commitment to its customer's ongoing success.
For someone engaging deeply in the technical aspects of gate valves, it becomes clear that the decision-making process should be informed by a combination of user experience and professional advice. Balancing practical insights with academic expertise creates a nuanced understanding of product capabilities and limitations. A holistic approach, considering not only the technical specifications but also the installation environment, routine maintenance needs, and long-term operational goals, ensures the successful integration of NRS gate valves.
In conclusion, the non-rising stem gate valve exemplifies an efficient and practical solution to complex fluid management problems. By integrating personal experience, professional expertise, authoritative innovations, and reliable trustworthiness, stakeholders can make informed decisions that optimize performance while safeguarding resources for future needs. Thus, investing in the right gate valve technology is not just about addressing current demands but preparing for a sustainable and more efficient operational future.