Double eccentric flange butterfly valves have gained significant traction in various industrial sectors due to their superior performance in fluid control systems. As industries continue to innovate and enhance operational efficiencies, understanding the distinct advantages and applications of these valves becomes crucial. With first-hand expertise and in-depth analysis, let’s dive into the world of double eccentric flange butterfly valves, unraveling their unique features and the reasons behind their growing popularity.
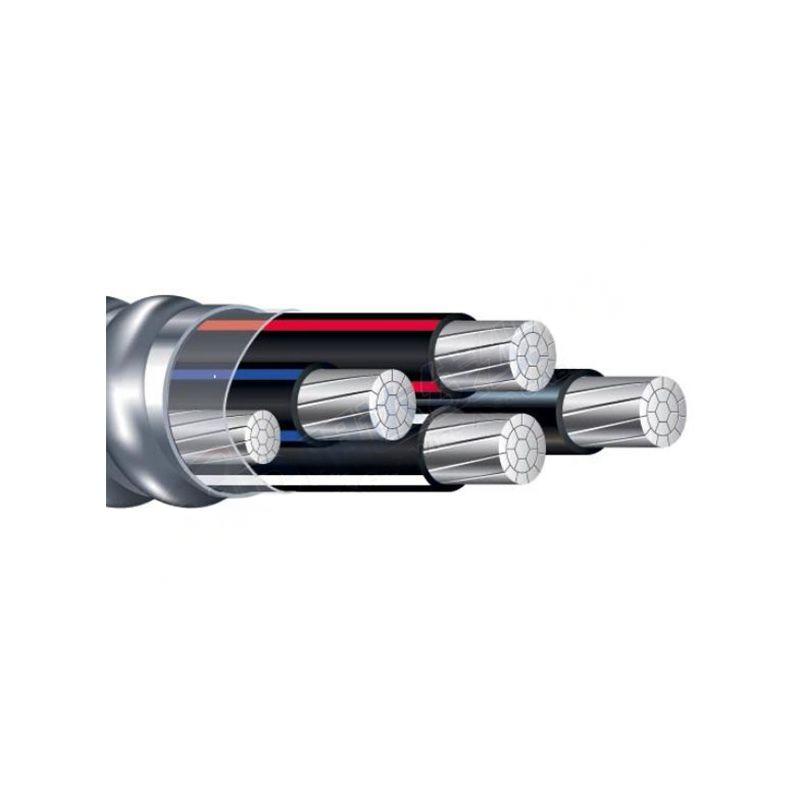
At the core of every efficient fluid control system lies a robust valve mechanism, essential for regulating the flow of liquids or gases. The double eccentric flange butterfly valve is lauded for its distinctive dual eccentric design that reduces sealing surface contact throughout its operational cycle. This design minimizes wear and tear, thereby enhancing the valve's longevity. The primary eccentricity allows the shaft centerline to deviate from the sealing line of the disc and seat, while the secondary eccentricity involves offsetting the rotating axis from the pipeline centerline. This unique construction negates binding during the opening operation and significantly decreases frictional forces.
In sectors such as petroleum, chemical, and wastewater treatment, operational reliability and cost-effectiveness are paramount.
Double eccentric flange butterfly valves cater to these needs. Their durability in handling extreme pressures and temperatures ensures consistent performance without frequent maintenance, a feature corroborated by industry leaders and experienced engineers. These valves also provide excellent shut-off capabilities, crucial for preventing leakage in high-stakes applications. The dependable sealing technology ensures safety and efficacy, especially in hazardous and corrosive environments.
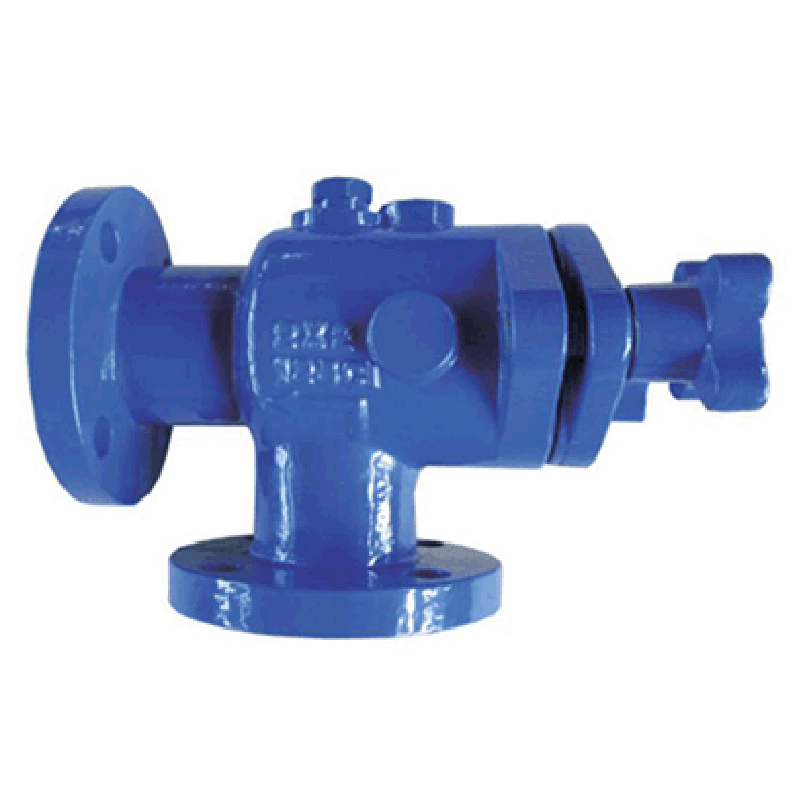
The material construction of double eccentric flange butterfly valves further underscores their adaptability to various operational conditions. Typically, these valves are constructed from high-grade metals such as stainless steel or alloy, offering excellent resistance to corrosion and erosion. This makes them ideal for applications involving abrasive or corrosive substances. Their flanged ends allow for secure installation and easy integration into existing pipelines, a feature particularly valued in retrofitting projects or where modification of current systems is economically unfeasible.
double eccentric flange butterfly valve
Experts within the field emphasize the importance of precision in the manufacturing process of these valves. Advanced engineering and meticulous quality control ensure that each valve meets stringent industry standards. The end result is a product that not only meets but often exceeds regulatory requirements, reinforcing its authority as a trusted component within industrial operations.
Furthermore, leveraging automation technology, contemporary double eccentric flange butterfly valves often incorporate smart systems that enable remote operation and real-time monitoring. These smart valves contribute to enhanced operational efficiency, paving the way for predictive maintenance and minimizing downtime. Industry professionals often recommend these intelligent systems for businesses looking to optimize fluid control processes through data-driven insights.
Testimonies from seasoned professionals highlight the dual benefits of installing double eccentric flange butterfly valves operational efficiency and cost savings. Reduced maintenance demands and extended service life translate directly into lower operational costs, offering a compelling return on investment. The ability to perform consistently under various operational pressures attests to their reliability and solidifies their reputation as a preferred choice among engineers and industrial designers.
In conclusion, double eccentric flange butterfly valves represent a merger of innovative design and reliable functionality. Their unique construction, robust material use, and potential for automation position them as indispensable components in modern industrial applications. Whether driven by the need for operational efficiency, cost reduction, or advanced control, these valves deliver exceptional performance valued across multiple sectors. With ongoing technological advancements, they will continue to redefine the standards for quality and efficiency in fluid control solutions.