When it comes to effectively managing fluid flow in various industries, the full lug butterfly valve stands out as a versatile and reliable option. Designed to control, regulate, and isolate fluid flow, these valves have found their niche in systems that require robust performance and easy maintenance. As an industry professional with deep expertise in fluid dynamics and valve engineering, I can attest to the significance of choosing the right butterfly valve for your setup.
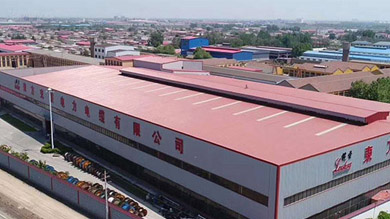
The full lug butterfly valve is distinguished by its ability to be installed in dead-end service without relying on a downstream flange. This feature makes it particularly advantageous in scenarios where system layout might change, providing flexibility in design. Unlike other valve types that necessitate complete system shutdowns for maintenance, a full lug design allows for maintenance on one side of the system while it continues to operate on the other—a benefit that maximizes uptime and efficiency, critical in industries such as water treatment and chemical processing.
From an engineering perspective, the choice of materials and construction significantly impacts the valve's performance. Typically, full lug butterfly valves are constructed from durable materials such as stainless steel, ductile iron, or PVC. The selected material must be compatible with the intended application environment to ensure longevity and avoid corrosion or wear. For instance, a stainless steel valve might be ideal in food and beverage applications due to its resistance to chemicals and ease of sanitation.
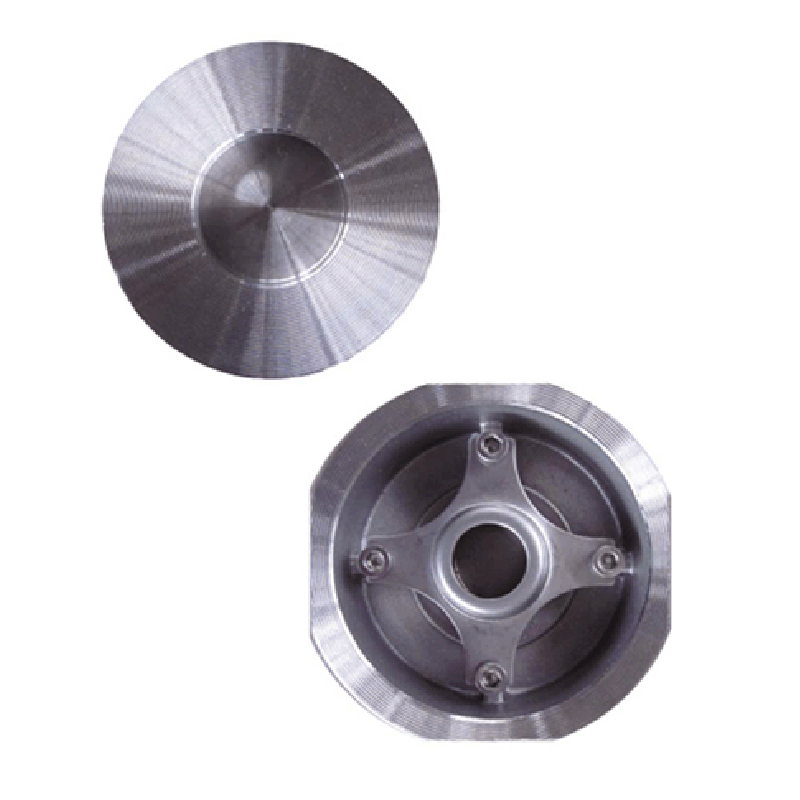
Operational efficiency is further enhanced by the valve's disc and seat design. The disc within the full lug butterfly valve pivots around its axis to control flow, offering a quick shut-off capability that is both efficient and reliable. However, it's the seat—often made from resilient materials like EPDM, NBR, or PTFE—that provides the necessary seal. The precision in seat engineering ensures minimal leakage, making these valves highly effective at maintaining pressure and avoiding costly fluid loss.
full lug butterfly valve
Furthermore, as someone who has collaborated with a wide range of clients across various sectors, I've seen firsthand the importance of proper valve sizing. Incorrect sizing can lead to either insufficient or excessive flow rates, affecting overall system performance. Conducting a comprehensive analysis that considers flow rate, pressure, and temperature parameters is vital to determining the correct valve size. Such precision not only optimizes performance but also extends the valve's lifecycle, thereby providing long-term cost savings.
In terms of authority, leading manufacturers of full lug butterfly valves invest in rigorous testing protocols to certify their products for industry-specific standards. This commitment to quality assurance builds trust among consumers and compliance with ANSI, API, and ISO standards is frequently sought to ensure that the valve performs to the highest expectations in demanding applications.
Trustworthiness is further assured through the transparency of performance data and warranty provisions. A manufacturer that provides detailed product specifications and offers generous warranty coverage signals confidence in their product, facilitating informed purchasing decisions among professionals. Moreover, brands that offer comprehensive support, including installation guidance and maintenance tips, empower users to maximize valve performance and lifespan.
As a cornerstone in fluid management systems, the full lug butterfly valve represents a blend of innovative engineering and practical functionality. By considering factors such as material selection, valve sizing, and manufacturer reputation, professionals can make informed decisions that enhance operational efficiency and system reliability. This strategic approach ultimately leads to significant improvements in industrial fluid handling, underscoring the full lug butterfly valve's critical role in modern process engineering.