Butterfly valves are an essential component in many industrial applications, due largely to their simple design, functionality, and cost-effectiveness. Among the varieties available, wafer type butterfly valves are particularly prominent. These valves provide an efficient solution for regulating flow in pipes, making them ideal for diverse industries, including water treatment, chemical processing, and food production. Understanding the dimensions and correct application of wafer type butterfly valves is crucial for ensuring optimal performance and longevity.
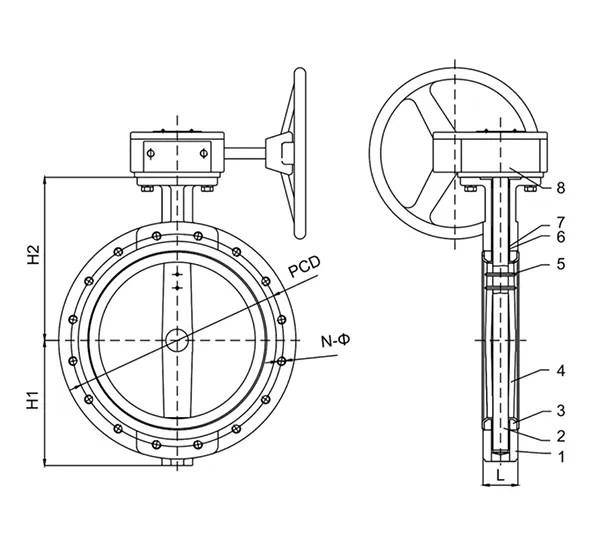
Wafer type butterfly valves are designed to fit between two flanges in a piping system. Unlike lug-style butterfly valves, wafer style valves do not have protruding lugs for bolts, instead, they rely on the bolts connecting the pipe flanges to hold the valve in place. This design makes them lighter, simpler, and often cheaper, suiting many non-critical service applications where they are not subject to excessive stress.
Typically, these valves consist of several key components a valve body, disc, stem, and seat. The disc is a rotating element that controls the flow of the medium through the valve, while the seat ensures tight closure, preventing any leaks when the valve is in the closed position. The wafer design is advantageous because it allows for easy installation and maintenance, often requiring less space compared to other valves.
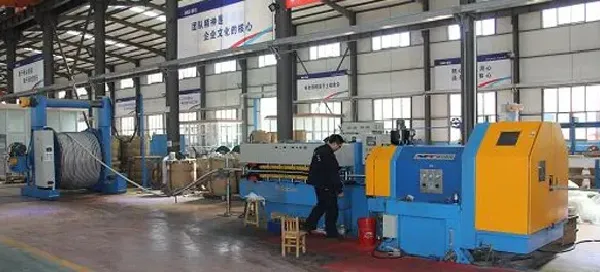
Dimensions play a critical role in ensuring the valve performs correctly and efficiently. Industry standards, such as those from the American National Standards Institute (ANSI) or the International Organization for Standardization (ISO), often govern these dimensions. Key measurement aspects of a wafer type butterfly valve include the bore diameter, face-to-face length, and outer dimensions to fit between the flanges.
Bore diameter is perhaps the most vital dimension, as it determines the flow rate capacity of the valve. It must match the pipeline size to minimize pressure drop and maximize efficiency. Similarly, the face-to-face measurement, which is the length end-to-end of the valve when installed between flanges, is critical for ensuring the valve fits correctly in the pipeline without applying undue stress that could cause leaks or premature wear.
Sealing performance relies significantly on the dimension accuracy of the valve, particularly when considering the disc’s diameter and its seating precision. Correct alignment ensures that the valve operates smoothly with minimal resistance, reducing wear and extending the lifespan of both the valve and the overall piping system.
wafer type butterfly valve dimension
A notable advantage of wafer type butterfly valves is their versatility in various applications. Because they maintain a compact profile, these valves are particularly beneficial in scenarios where space and weight are considerations, such as in ships or offshore environments. Their design accommodates consistent performance even under significant pressure and temperature variations, as long as the materials of construction are adequately selected according to the operating conditions.
However, one must consider the limitations associated with wafer type butterfly valves. They typically do not provide the same level of support for the piping system as lug type could, making them less suitable for systems that require frequent disassembly or systems that may be subjected to high stresses. This is an important consideration for engineers and procurement specialists when designing or retrofitting systems.
Authored by experts in the field of industrial flow control solutions, this examination of wafer type butterfly valve dimensions underscores their significance to achieving efficient operation. Specialists recommend utilizing reliable engineering resources and consulting with valve manufacturers or certified distributors to verify compatibility with existing systems and specific industrial applications.
To ensure the highest level of operational reliability and cost-effectiveness, proper material selection based on the fluid medium, temperature, pressure, and environmental conditions is also critical. Advanced technologies in valve design continue to evolve, offering enhanced performance and durability, thus remaining a staple in the array of industrial flow control solutions available to professionals today.
In summary, wafer type butterfly valves present a cost-effective, space-saving solution for managing flow within pipelines. Accurately understanding their dimensions and practical implementations can drastically impact performance, making expertise in their application an invaluable asset in industrial settings. Aim at thorough evaluations, context-specific adaptations, and adherence to recognized standards to exploit the full benefits these components offer to modern engineering systems.