Engineering marvels often operate quietly behind the scenes, ensuring the smooth functioning of countless industries. Among these quiet operators are industrial valves, pivotal components that regulate, direct, or control the flow of fluids in various applications. Delving into the nuances of these essential devices reveals a fascinating world marked by precision engineering, material science, and relentless innovation.

Industrial valves, key to operational efficiency in sectors ranging from oil & gas to water treatment, represent the intersection of advanced engineering and applied chemistry. Crafted from durable materials like stainless steel, brass, and advanced polymers, these valves endure extreme pressures and temperatures. Their durability is a testament to the scientific rigor employed in their design and manufacturing processes, underscoring the authority these pieces hold in industrial applications.
Expertise in valve design is paramount. Ball valves, butterfly valves, gate valves, and globe valves each serve distinct functions, suitable for different industrial needs. Selecting the appropriate type involves understanding fluid dynamics, pressure conditions, and the specific requirements of the industrial process. For instance, ball valves offer excellent shut-off capabilities and are ideal for systems that demand a tight seal. In contrast, globe valves provide superior throttling capabilities, crucial for processes where precise flow control is necessary.
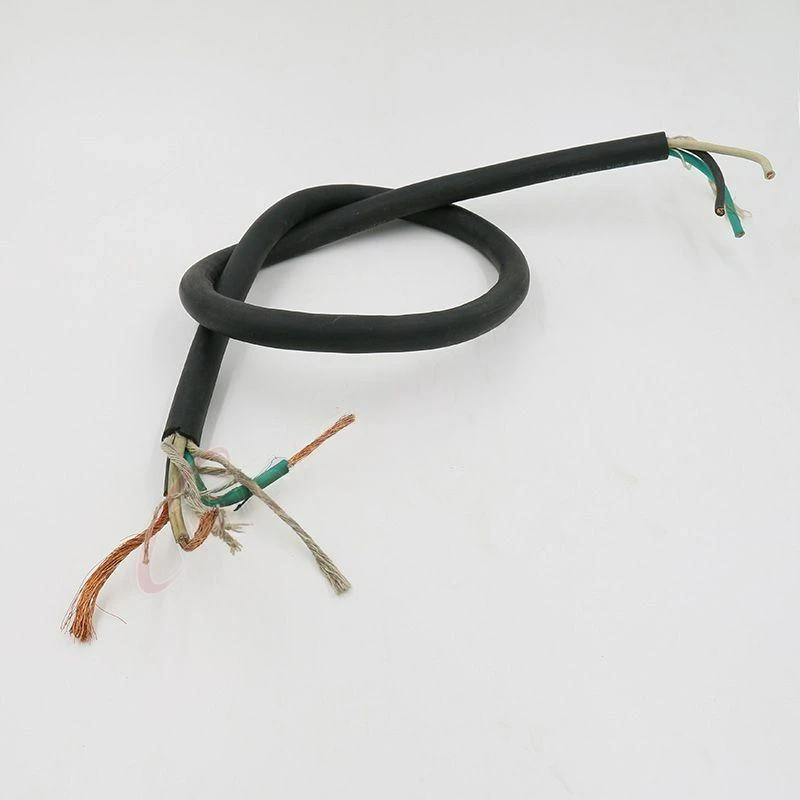
Trustworthiness of industrial valves is inherent in their design and implementation within infrastructure. Leading manufacturers employ stringent quality control measures, adhering to international standards such as ISO and API. These standards ensure that valves can withstand their operational environments, thereby safeguarding operations and maintaining system integrity. The reliability of an industrial valve is non-negotiable, as any compromise can result in significant operational setbacks, financial losses, or safety hazards.
industrial valve
Real-world experiences further underscore the critical nature of these components. Consider the profound impact of a single malfunctioning valve in a chemical processing plant. A minor failure could lead to uncontrolled fluid discharge, posing safety risks and operational halts. This scenario highlights why routine maintenance and regular inspections, led by seasoned professionals, are critical. It’s not merely about maintaining the equipment but ensuring that the people, and environments involved in these operations, remain safe.
However, innovation does not rest. The industrial valve sector is continually evolving, integrating technology to enhance functionality and safety. Smart valves, equipped with sensors and connectivity features, are emerging as game-changers. They provide real-time data, aiding in predictive maintenance and operational efficiency. These advancements reflect the industry's commitment to marrying traditional engineering excellence with digital innovation, laying the groundwork for more responsive and efficient systems.
In conclusion, industrial valves are not mere components; they are the backbone of industrial fluid management. Their successful application depends on understanding their fundamental principles, a commitment to quality standards, and a forward-thinking approach to technological adoption. Professionals engaged in their utilization stand at the helm of operational excellence, balancing expertise with the wisdom of experience to maintain safe and efficient industrial ecosystems.